Introduction
Choosing the wrong stainless steel can lead to costly failures, reduced performance, and premature replacement in critical applications. For professionals in construction, manufacturing, and product design, understanding material differences is not just important—it’s essential for long-term success and profitability.
This guide dives into the core distinctions between 304 vs 316 stainless steel, two of the most widely used grades. We will uncover their unique strengths, weaknesses, and ideal applications, cutting through the noise to help you make truly informed decisions. By understanding these subtle yet critical differences, you can avoid common pitfalls and ensure your projects are built to last, saving both time and money.
Essential Factors: Unlocking 304 vs 316 Stainless Steel Performance
Understanding the core chemical makeup of stainless steel is crucial for anyone working with metal. This chapter will dive into the elemental differences between 304 and 316 stainless steel. These compositions are not just random numbers; they directly dictate how each grade performs in various environments. Knowing these distinctions can help you pick the right material for your project, preventing costly errors and ensuring long-lasting durability.
For industrial professionals, making an informed choice between 304 vs 316 stainless steel means optimizing project costs and reducing material waste. While many resources discuss general properties, a practical, in-depth comparison of these two common grades, especially for specific industry applications, is often hard to find.
The Role of Chromium and Nickel in Stainless Steel
Chromium is the main ingredient that makes stainless steel “stainless.” It creates a thin, protective layer on the surface that resists corrosion. Both 304 and 316 stainless steel contain significant amounts of chromium, typically around 16-18%. This layer, called the passive film, repairs itself when scratched, offering continuous protection against rust and stains. Without enough chromium, steel would simply rust away like regular iron.
Nickel is another vital element, especially in austenitic stainless steels like 304 and 316. It enhances ductility and toughness, meaning the steel is easier to form and less likely to become brittle. Nickel also boosts corrosion resistance, particularly in acidic conditions. Type 304 stainless steel typically has around 8-10% nickel, contributing to its widespread use and good all-around performance.
Molybdenum: The Key Differentiator in 316 Stainless Steel
The primary difference in 316 stainless steel composition is the addition of molybdenum. While 304 stainless steel relies on chromium and nickel for its properties, 316 includes about 2-3% molybdenum. This small but mighty addition significantly improves corrosion resistance, especially against chlorides and other harsh chemicals. Molybdenum helps the steel resist pitting and crevice corrosion, which are common problems in marine environments or areas exposed to saltwater and industrial cleaners.
“Understanding a material’s chemical composition is like knowing its DNA; it reveals its strengths and weaknesses, enabling precise engineering decisions.”
This is why 316 is often called marine-grade stainless steel; it’s better equipped to handle salty air and corrosive liquids. The inclusion of molybdenum makes 316 a top choice for challenging applications where 304 might not hold up. This added resistance is crucial for industries like chemical processing, food handling, and pharmaceutical manufacturing, where exposure to aggressive substances is common.
Minor Alloying Elements and Their Impact
Beyond chromium, nickel, and molybdenum, both 304 and 316 stainless steel contain smaller amounts of other elements. Carbon is present in both, usually in low percentages to maintain corrosion resistance and good weldability. Too much carbon can make the steel more susceptible to sensitization, a condition where it corrodes along grain boundaries, especially after welding. Nitrogen is sometimes added to improve strength and stability.
These minor components, while small in quantity, play a role in fine-tuning the steel’s properties. For instance, controlled levels of manganese and silicon contribute to deoxidation during the steelmaking process. They also affect the steel’s formability and overall mechanical properties. Even trace elements are carefully monitored to ensure the final product meets specific performance standards for various applications. Over time, manufacturers have refined these compositions to balance cost, performance, and ease of fabrication.
ASTM and International Standards for 304 and 316
The chemical compositions of 304 stainless steel composition and 316 stainless steel composition are not left to chance; they are strictly defined by international standards. The American Society for Testing and Materials (ASTM) is one of the most recognized organizations, with specifications like ASTM A240 covering both plate and sheet forms. These standards outline the precise ranges for each element, ensuring consistency and quality across different manufacturers.
Other global bodies, such as ISO (International Organization for Standardization) and EN (European Norm), also publish standards for various stainless steel grades. Adhering to these standards is essential for trustworthy material sourcing. It provides a common language for engineers and suppliers worldwide, ensuring that when you order a specific stainless steel grade, you receive a product with predictable properties. For instance, the exact chemical differences between 304 and 316 stainless steel regarding their carbon, chromium, nickel, and molybdenum content are all meticulously detailed in these official documents, verifying that industry requirements are met. This standardization also helps in global trade, acting as a quality checkpoint that builds confidence between buyers and sellers.
Knowing these standards helps professionals confidently select materials. It ensures that the steel will perform as expected in its intended application, from construction and automotive to medical devices and kitchenware. For instance, if you are looking for stainless steel grades for food processing equipment, compliance with specific ASTM or ISO standards ensures the material is safe and resistant to common food acids. It helps avoid materials that might be a bait and switch and ensure product quality.
Stainless Steel Comparison: Elemental Composition
Element | 304 Stainless Steel (wt. %) | 316 Stainless Steel (wt. %) | Measurement Method | Typical Industry Requirement |
---|---|---|---|---|
Chromium (Cr) | 17.5 – 19.5 | 16.0 – 18.0 | X-ray Fluorescence (XRF) | 16-20% for corrosion resistance |
Nickel (Ni) | 8.0 – 10.5 | 10.0 – 14.0 | Inductively Coupled Plasma (ICP) | 8-14% for ductility & toughness |
Molybdenum (Mo) | 0.0 – 0.5 | 2.0 – 3.0 | Atomic Absorption (AA) | >2% for pitting resistance (316 only) |
Carbon (C) | 0.08 max | 0.08 max | Combustion Analysis | <0.08% for weldability |
Manganese (Mn) | 2.0 max | 2.0 max | Optical Emission Spectrometry (OES) | <2% for deoxidation |
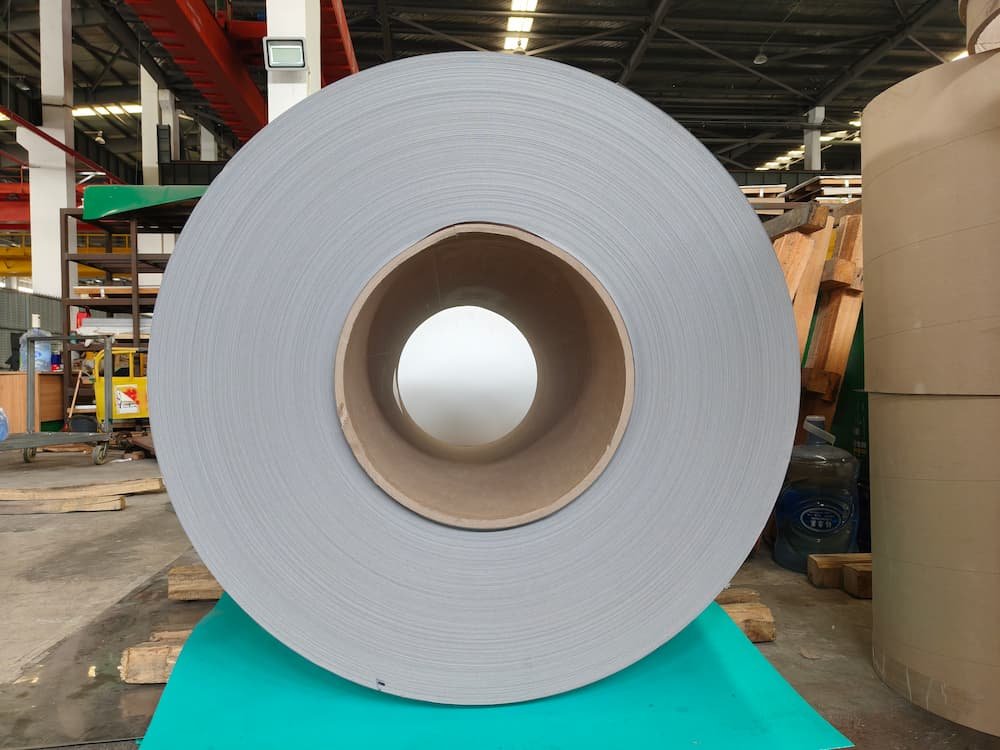
The Role of Chromium and Nickel in Stainless Steel
Chromium is the main ingredient that makes stainless steel “stainless.” It creates a thin, protective layer on the surface that resists corrosion. Both 304 and 316 stainless steel contain significant amounts of chromium, typically around 16-18%. This layer, called the passive film, repairs itself when scratched, offering continuous protection against rust and stains. Without enough chromium, steel would simply rust away like regular iron.
Nickel is another vital element, especially in austenitic stainless steels like 304 and 316. It enhances ductility and toughness, meaning the steel is easier to form and less likely to become brittle. Nickel also boosts corrosion resistance, particularly in acidic conditions. Type 304 stainless steel typically has around 8-10% nickel, contributing to its widespread use and good all-around performance.
Molybdenum: The Key Differentiator in 316 Stainless Steel
The primary difference in 316 stainless steel composition is the addition of molybdenum. While 304 stainless steel relies on chromium and nickel for its properties, 316 includes about 2-3% molybdenum. This small but mighty addition significantly improves corrosion resistance, especially against chlorides and other harsh chemicals. Molybdenum helps the steel resist pitting and crevice corrosion, which are common problems in marine environments or areas exposed to saltwater and industrial cleaners.
“Understanding a material’s chemical composition is like knowing its DNA; it reveals its strengths and weaknesses, enabling precise engineering decisions.”
This is why 316 is often called “marine-grade” stainless steel; it’s better equipped to handle salty air and corrosive liquids. The inclusion of molybdenum makes 316 a top choice for challenging applications where 304 might not hold up. This added resistance is crucial for industries like chemical processing, food handling, and pharmaceutical manufacturing, where exposure to aggressive substances is common.
Minor Alloying Elements and Their Impact
Beyond chromium, nickel, and molybdenum, both 304 and 316 stainless steel contain smaller amounts of other elements. Carbon is present in both, usually in low percentages to maintain corrosion resistance and good weldability. Too much carbon can make the steel more susceptible to sensitization, a condition where it corrodes along grain boundaries, especially after welding. Nitrogen is sometimes added to improve strength and stability.
These minor components, while small in quantity, play a role in fine-tuning the steel’s properties. For instance, controlled levels of manganese and silicon contribute to deoxidation during the steelmaking process. They also affect the steel’s formability and overall mechanical properties. Even trace elements are carefully monitored to ensure the final product meets specific performance standards for various applications. Over time, manufacturers have refined these compositions to balance cost, performance, and ease of fabrication.
ASTM and International Standards for 304 and 316
The chemical compositions of 304 stainless steel composition and 316 stainless steel composition are not left to chance; they are strictly defined by international standards. The American Society for Testing and Materials (ASTM) is one of the most recognized organizations, with specifications like ASTM A240 covering both plate and sheet forms. These standards outline the precise ranges for each element, ensuring consistency and quality across different manufacturers.
Other global bodies, such as ISO (International Organization for Standardization) and EN (European Norm), also publish standards for various stainless steel grades. Adhering to these standards is essential for trustworthy material sourcing. It provides a common language for engineers and suppliers worldwide, ensuring that when you order a specific stainless steel grade, you receive a product with predictable properties. For instance, the exact chemical differences between 304 and 316 stainless steel regarding their carbon, chromium, nickel, and molybdenum content are all meticulously detailed in these official documents, verifying that industry requirements are met. This standardization also helps in global trade, acting as a quality checkpoint that builds confidence between buyers and sellers.
Knowing these standards helps professionals confidently select materials. It ensures that the steel will perform as expected in its intended application, from construction and automotive to medical devices and kitchenware. For instance, if you are looking for stainless steel grades for food processing equipment, compliance with specific ASTM or ISO standards ensures the material is safe and resistant to common food acids. It helps avoid materials that might be a bait and switch and ensure product quality.
Stainless Steel Comparison: Elemental Composition
Element | 304 Stainless Steel (wt. %) | 316 Stainless Steel (wt. %) | Measurement Method | Typical Industry Requirement |
---|---|---|---|---|
Chromium (Cr) | 17.5 – 19.5 | 16.0 – 18.0 | X-ray Fluorescence (XRF) | 16-20% for corrosion resistance |
Nickel (Ni) | 8.0 – 10.5 | 10.0 – 14.0 | Inductively Coupled Plasma (ICP) | 8-14% for ductility & toughness |
Molybdenum (Mo) | 0.0 – 0.5 | 2.0 – 3.0 | Atomic Absorption (AA) | >2% for pitting resistance (316 only) |
Carbon (C) | 0.08 max | 0.08 max | Combustion Analysis | <0.08% for weldability |
Manganese (Mn) | 2.0 max | 2.0 max | Optical Emission Spectrometry (OES) | <2% for deoxidation |
Common Uses for 304 Stainless Steel (e.g., kitchenware, architectural trim)
Type 304 stainless steel is the most widely used and versatile of all stainless steels. Its excellent corrosion resistance, formability, and appealing finish make it ideal for numerous applications where strong resistance to general corrosion is needed, but exposure to chlorides is minimal. A common example is kitchenware, including sinks, pots, and pans, due to its hygiene properties and ease of cleaning. It’s also found in food processing equipment, where it handles various acids present in food without issue.
Beyond the kitchen, 304 stainless steel is a popular choice for architectural trim, roofing, and wall panels due to its aesthetic appeal and atmospheric corrosion resistance. Its weldability and fabrication characteristics make it a go-to material for many general-purpose applications. While it offers good durability in normal conditions, it’s not designed for the harshest environments. For everyday items and indoor applications, though, it’s a **”go-to”** material.
Ideal Applications for 316 Stainless Steel (e.g., marine, medical, chemical processing)
When conditions get tougher, 316 stainless steel steps up. Its added molybdenum content significantly boosts its resistance to pitting and crevice corrosion, particularly in chloride-rich environments. This makes it the preferred material for marine applications, such as boat fittings, railings, and fixtures, as it withstands saltwater exposure much better than 304. For this reason, it is often referred to as marine-grade stainless steel.
“Choosing the correct stainless steel grade for an application can save significant long-term costs by preventing premature material degradation and ensuring operational reliability.”
In the medical field, 316L (a low-carbon version of 316) is extensively used for surgical instruments and implants due to its superior corrosion resistance against bodily fluids and harsh sterilization chemicals. Chemical processing industries also rely heavily on 316 for tanks, pipes, and valves that handle various aggressive chemicals. Its enhanced properties ensure longer service life and safer operations in these critical settings.
Scenarios Where Either Grade is Acceptable (and why)
There are instances where both 304 and 316 stainless steel might technically function, but choosing the more cost-effective option makes commercial sense. For example, in indoor non-coastal architectural elements like handrails or decorative panels, 304 stainless steel often provides adequate corrosion resistance at a lower price point. Its overall attractiveness and durability in common atmospheric conditions are perfectly suitable. The primary consideration often becomes the balance between cost and performance.
Another example is some general manufacturing equipment where exposure to aggressive chemicals or chlorides is intermittent or very low. Selecting 316 in these scenarios might be overkill, leading to unnecessary material expenses. Engineers and procurement teams must carefully evaluate the environmental stressors and project budget to make the most economical yet functional choice. HnL Steel, specializing in various steel products, helps clients assess these needs, ensuring they get reliable solutions that align with their profitability goals.
Industry-Specific Examples and Case Studies
Let’s consider specific industry needs when comparing applications of 304 stainless steel and uses of 316 stainless steel. In dairy processing, equipment often exposed to milk acids and cleaning solutions might use 304 for general surfaces, but 316 is preferred for direct contact areas like pasteurizers due to more aggressive cleaning agents. For outdoor street furniture in urban areas without heavy de-icing salt use, 304 is often sufficient. However, for applications near coastal regions or where road salts are common, 316 would be a better investment to prevent premature rust.
In pulp and paper mills, where harsh acidic and bleaching chemicals are prevalent, 316 stainless steel is almost exclusively used for critical components. Conversely, in residential potable water systems, 304 provides more than enough corrosion resistance for pipes and fittings. These examples highlight why a simple stainless steel comparison often doesn’t capture the nuanced decision-making required. Each industry and application presents unique challenges, making a one-size-fits-all approach impractical. Understanding these nuances helps professionals make choices that enhance product longevity and client satisfaction, preventing costly replacements down the line and ensuring structures remain reliable solutions you can build upon.
Stainless Steel Grade Selection Guide
Application Category | Typical Environment | Recommended Grade | Justification | Expected Lifespan (Years) |
---|---|---|---|---|
Kitchen Sinks & Appliances | Indoor, domestic, mild acids | 304 | Good general corrosion resistance, cost-effective | 20+ |
Marine Fittings (Saltwater) | Outdoor, high chloride exposure | 316 | Superior pitting and crevice corrosion resistance | 15-25 |
Food Processing Equipment | Varied, sanitizing chemicals, organic acids | 304 (general), 316 (critical contact) | 304 for general, 316 for higher acid/cleaning resistance | 10-20 |
Architectural Trim (Non-coastal) | Outdoor, atmospheric exposure | 304 | Good aesthetic retention, sufficient atmospheric resistance | 30+ |
Chemical Storage Tanks | Indoor/Outdoor, aggressive chemicals | 316 | Necessary for resistance to strong acids and chlorides | 10-20 (depending on chemical) |
Cost Comparison: Initial vs. Lifespan Value of 304 vs. 316
When comparing the cost of stainless steel grades, the initial purchase price is only one piece of the puzzle. Generally, 316 stainless steel is more expensive than 304. This price difference stems from the addition of molybdenum in 316, which is a more costly alloying element. The immediate cost implication might make 304 seem like the cheaper option, and in many applications, it is.
However, it’s crucial to consider the total cost of ownership (TCO) over the product’s lifespan. In environments prone to corrosion, such as those with high chloride exposure, 304 stainless steel might fail prematurely. This leads to replacement costs, maintenance expenses, and potential operational downtime. In such scenarios, the higher initial investment in 316 stainless steel can result in significant long-term savings due to its superior corrosion resistance and extended service life. It’s about choosing a solution that is durable and cost-effective in the long run.
Global Availability and Supply Chain Dynamics for Each Grade
Both 304 and 316 stainless steel are widely produced and globally available. Type 304 is the most common stainless steel grade, meaning its supply chain is typically robust and less susceptible to minor disruptions. This prevalence often translates to better lead times and more competitive pricing for large-volume orders. Its extensive use in diverse industries ensures a consistent global supply.
“Strategic procurement of stainless steel hinges on calculating total cost of ownership, accounting for material durability, and ensuring supply chain reliability, ultimately leading to significant long-term savings.”
While also widely available, 316 stainless steel may have slightly shorter supply lines or be subject to more price volatility due to fluctuations in molybdenum prices. Suppliers often stock both, but quantities of 304 are generally higher. For specialized forms or large volumes of 316, it might require more advanced planning or sourcing from specific suppliers. When sourcing stainless steel for manufacturing, understanding these dynamics helps in predicting procurement timelines and managing budgets effectively. This isn’t just about finding the material but ensuring its consistent availability, allowing for smooth production schedules.
Machinability, Weldability, and Fabrication Costs
The choice between 304 and 316 stainless steel also impacts fabrication costs, which include machining and welding. Both grades exhibit good machinability, but the presence of molybdenum in 316 can make it slightly harder to machine compared to 304. This difference is usually minor and won’t significantly affect costs for most standard machining operations. However, for complex parts requiring extensive intricate machining, this might translate to slightly increased tool wear or longer machining times.
In terms of weldability, both 304 and 316 are generally easy to weld, especially their low-carbon versions (304L and 316L), which reduce the risk of sensitization. However, 316 stainless steel often requires careful control of heat input during welding to prevent hot cracking. Again, these are minor considerations for experienced fabricators but can add to the overall fabrication cost through specialized welding procedures or increased inspection. Understanding how much more expensive 316 stainless steel can be to work with compared to 304 involves factoring in these downstream processes. It’s not just the raw material price but also the labor and tooling involved.
The Role of Reputable Suppliers (e.g., HnLsteel)
Partnering with a reputable stainless steel supplier is paramount for successful procurement. A reliable supplier offers quality assurance, ensuring the material meets international standards and specifications. They also provide flexible payment terms and fast delivery, which are crucial for managing project timelines and cash flow. For instance, HnLsteel prides itself on building honest, long-term relationships with customers by providing high-quality steel products and exceptional service, including Aluzinc steel coils, structural steel beams, pipes, and customized metal solutions.
A good supplier acts as a technical consultant, helping you choose the best grade for your specific application and addressing any after-sales problems. They can guide you on the global availability of 304 and 316 stainless steel, market trends, and help tailor solutions to your business growth. Businesses like HnLsteel help make purchasing decisions based on total cost of ownership, supply reliability, and custom fabrication needs. Their commitment to integrity and quality sets them apart as a supply chain partner. Choosing the right supplier means you’re getting not just metal, but a reliable solution you can build upon. It’s about securing a “smooth sailing” procurement process.
Procurement Considerations for 304 vs. 316 Stainless Steel
Factor | 304 Stainless Steel | 316 Stainless Steel | Impact on Procurement (Details) | Risk Level (1-5) |
---|---|---|---|---|
Initial Material Cost | Lower | Higher (15-30% more) | Direct impact on upfront budget; affects initial project cost. | 3 (for budget overruns if 316 is needed) |
Long-Term Value / TCO | Lower in harsh environments | Higher in harsh environments | Reduces lifecycle costs for demanding applications; minimizes replacements. | 1 (if correctly specified) |
Global Availability | Very High | High | Easier to source; less prone to supply chain disruptions due to commonality. | 1 |
Molybdenum Price Volatility | Not affected | Sensitive | Prices can fluctuate with Mo market; requires careful monitoring. | 3 |
Fabrication Complexity | Standard | Slightly more complex (machining, welding) | May incur marginal increases in tooling and labor costs. | 2 |
Making the Right Choice: Expert Recommendations and Future Considerations
Choosing between 304 and 316 stainless steel is a critical decision that impacts project success, longevity, and cost. This chapter aims to synthesize the key differences discussed in previous sections, offering clear, actionable recommendations for professionals. By providing a structured approach to material selection, we empower you to make informed decisions that avoid future costs and enhance project durability, ultimately ensuring everything runs smoothly from start to finish.
While many articles detail the characteristics of stainless steel, there’s often a gap in providing practical, actionable guidance for specific industrial situations. This guide bridges that gap, helping you confidently choose stainless steel grade that aligns with your project’s demands and long-term goals.
Decision Matrix: When to Choose 304 vs. 316
The decision to use 304 vs 316 stainless steel primarily hinges on the operating environment and performance requirements. Choose 304 stainless steel when the application involves moderate environments without high exposure to chlorides or aggressive chemicals. This includes general architectural applications, kitchen equipment, and most indoor or dry outdoor settings. Its lower cost makes it a more economical choice where its corrosion resistance is sufficient.
Opt for 316 stainless steel when the application demands superior corrosion resistance, particularly against chlorides. This includes marine environments, chemical processing plants, medical equipment, and highly corrosive industrial settings. The added molybdenum in 316 provides the necessary protection against pitting and crevice corrosion, significantly extending the material’s lifespan and reducing maintenance needs in harsh conditions. While initially more expensive, the advantages of using 316 stainless steel often outweigh the cost over time.
Case Studies: Successful Grade Selection in Diverse Projects
Consider a large-scale public art installation near a coastline. Initial budget considerations might push for 304, but expert advice would strongly recommend 316. The constant exposure to saltwater spray and atmospheric chlorides would quickly degrade 304, leading to visible corrosion and costly repairs, ruining the aesthetic appeal. A project that selected 316 for its entire structure would exhibit minimal corrosion years later, proving the long-term value of the higher-grade material.
“Making the right material choice initially, rather than focusing solely on upfront cost, is the cornerstone of long-term project success and cost-efficiency in any industrial application.”
Conversely, a food processing plant for dry goods might initially consider 316 for all equipment. However, an analysis of the environment reveals minimal moisture and no corrosive chemicals. In this scenario, using 304 for general handling equipment would be a perfectly suitable and more cost-effective choice. This allows the budget to be allocated to other critical areas, demonstrating how precise stainless steel selection guide can optimize resources without compromising performance.
Practical Tips for Material Specification and Testing
When specifying stainless steel, always clearly define the operating conditions, including temperature, chemical exposure, and presence of chlorides. Don’t assume; always verify. Request certifications from your supplier that confirm the chemical composition and mechanical properties of the steel. This quality assurance step ensures you receive the exact material specified. HnLsteel, for example, emphasizes quality control, with products manufactured in strict accordance with domestic and international standards, providing assurance to their clients.
Consider conducting small-scale tests or consulting with material engineers for highly critical or unusual applications. This expert advice on 304 vs 316 can provide invaluable insights before committing to a large order. Remember to specify the appropriate surface finish, as it can also impact corrosion resistance and ease of cleaning. Proper documentation and traceability throughout the procurement process are also paramount for problem-solving or future audits.
Future Outlook: Innovations and Sustainability in Stainless Steel Production
The stainless steel industry is continuously evolving, driven by demands for better performance, cost-efficiency, and environmental responsibility. Innovations are leading to new stainless steel grades with enhanced properties, such as higher strength or improved corrosion resistance with less expensive alloying elements. Research into advanced manufacturing techniques, like additive manufacturing (3D printing), is also opening new possibilities for complex stainless steel components.
Sustainability is another growing focus. Stainless steel is 100% recyclable, and efforts are ongoing to reduce the carbon footprint of its production. Manufacturers are investing in cleaner energy sources and more efficient processes. These trends suggest a future where stainless steel remains a vital material, offering even more precise solutions for various applications while minimizing environmental impact. For professionals looking to select stainless steel for corrosive environments, staying updated on these advancements will be key. Engaging with an expert like Iris from HnLsteel can provide access to tailored solutions and insights into these emerging trends, helping you explore opportunities to expand your business together and stay ahead of the curve. It’s about being on the cutting edge of material science.
Stainless Steel Grade Selection Decision Matrix
Factor | Low Risk/Cost (304) | Moderate Risk/Cost | High Risk/Cost (316) | Decision Metric |
---|---|---|---|---|
Chloride Exposure | No/Minimal (e.g., indoor) | Occasional (e.g., urban outdoor) | Frequent/High (e.g., marine, chemical) | Concentration (ppm) |
Corrosive Chemicals | Mild (e.g., food acids) | Some (e.g., weak industrial acids) | Aggressive (e.g., strong acids, medical sterilants) | pH, Chemical Type |
Temperature Range | Ambient | Moderate fluctuations | High/Extreme (e.g., industrial processes) | Operating Temp (°C) |
Required Lifespan | Standard (5-10 yrs) | Extended (10-20 yrs) | Very Long (20+ yrs) | Expected Service Life |
Fabrication Complexity | Simple forming/welding | Moderate operations | Complex machining/welding | Manufacturing Process |
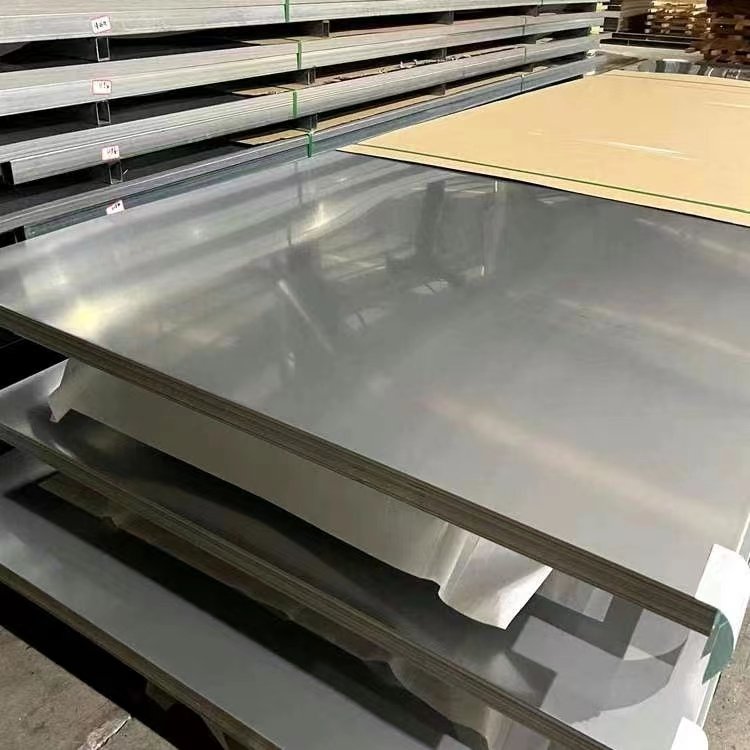
Conclusion
After more than a decade in this industry, I’ve learned that choosing the right stainless steel isn’t just about technical specifications; it’s about making a smart investment in your project’s future. Overlooking the subtle differences between 304 and 316 can lead to costly mistakes down the road.
My experience has shown me that quality assurance and expert guidance are key players in material selection. When you get it right, you save time, money, and headaches. It’s why I always recommend partnering with a supplier who understands your specific needs and can back their products with solid service.
Ultimately, selecting the best stainless steel grade means ensuring your projects are built to last. It’s about securing reliable solutions you can truly build upon for years to come.
FAQ
Q1: What is the difference between 304 and 316 stainless steel?
A1: The primary difference between 304 and 316 stainless steel is the addition of molybdenum in 316 stainless steel, which enhances its corrosion resistance, especially against chlorides and marine environments.
Q2: Which grade of stainless steel is most corrosion resistant?
A2: 316 stainless steel is recognized for its superior corrosion resistance, particularly in harsh environments such as coastal or marine applications due to its molybdenum content.
Q3: What are the applications of 304 stainless steel?
A3: 304 stainless steel is commonly used in kitchen equipment, storage tanks, and piping, as it provides good corrosion resistance and is easy to fabricate.
Q4: What are the applications of 316 stainless steel?
A4: 316 stainless steel is ideal for environments exposed to chlorides, making it suitable for marine applications, chemical processing equipment, and medical devices.
Q5: How does the cost of 304 and 316 stainless steel compare?
A5: 316 stainless steel is generally more expensive than 304 due to its additional alloying elements, which enhance its corrosion resistance.
Q6: Is 304 stainless steel easier to machine than 316?
A6: Yes, 304 stainless steel is typically easier to machine compared to 316 due to its lower nickel content, which can make 316 more difficult to work with.
Q7: What factors should be considered when choosing stainless steel grades?
A7: When choosing stainless steel grades, consider factors like corrosion resistance, mechanical properties, cost, and the specific application environment.
Q8: Which stainless steel grade is recommended for food processing?
A8: Both 304 and 316 stainless steels are used in food processing, but 316 is preferred for applications with high chlorine exposure or saltwater.
External Links
- Stainless steel | Definition, Composition, Types, & Facts | Britannica
- Introduction to stainless steels – worldstainless
- Types of Stainless Steel: Properties, Grades and Applications
- Stainless Steel: Grades, Composition, Properties & Types
- Stainless Steel Properties, Benefits, and 8 Main Uses
- Stainless Steel – Properties, Grades and Applications | Fractory
- What Is Stainless Steel?: Definition, Types, Characteristics
- What is Stainless Steel – Definition | Material Properties
2 Responses