Introduction
Choosing the right stainless steel can make or break your project—corrosion, cost, and performance hang in the balance. Engineers and decision-makers often wrestle with whether **austenitic stainless steel** or ferritic fits their needs, especially under tight budgets and tough conditions.
This comparison breaks down their differences—chemical makeup, strength, and real-world uses. From austenitic’s edge in harsh environments to ferritic’s budget-friendly appeal, you’ll get clear insights to pick the best type. Companies like HnL Steel ensure quality and fast delivery, making material selection smoother.
Introduction to Austenitic and Ferritic Stainless Steel
What is Stainless Steel? A Brief Overview
Stainless steel is a family of iron-based alloys known for their resistance to corrosion and staining. These special metals contain at least 10.5% chromium, which forms a thin layer of chromium oxide on the surface, protecting against rust. Different types of stainless steel offer varying levels of strength, workability, and resistance to heat and chemicals. These qualities make stainless steel vital in many industries, from food processing to chemical plants.
Austenitic and ferritic stainless steels represent two major families with distinct properties, each offering unique advantages that make them suitable for specific industrial applications.
Defining Austenitic Stainless Steel: Core Characteristics
Austenitic stainless steel stands out as the most common type, making up about 70% of stainless steel production worldwide. It contains high levels of chromium (16-26%) and nickel (6-22%), giving it a face-centered cubic crystal structure. This structure provides excellent formability and weldability, letting fabricators shape it easily. The nickel content in austenitic stainless steel boosts its corrosion resistance, especially in harsh environments. Common grades include 304 (18-8) and 316, which are workhorses in many industries from food processing to chemical manufacturing.
Defining Ferritic Stainless Steel: Core Characteristics
Ferritic stainless steel contains chromium (10.5-30%) but little or no nickel. This gives it a body-centered cubic crystal structure similar to carbon steel. Without nickel, ferritic stainless steel typically costs less than austenitic types, making it budget-friendly for many projects. It offers good resistance to stress corrosion cracking and performs well at high temperatures. However, it has lower ductility and weldability compared to austenitic grades. Common ferritic grades include 430 and 439, often used in automotive exhaust systems and indoor appliances.
Why Compare These Two Types? Importance for Industry Professionals
Understanding the differences between austenitic and ferritic stainless steel helps engineers and buyers make informed decisions. Material selection impacts project cost, performance, and lifespan. The right choice depends on specific needs: operating temperature, exposure to chemicals, required strength, and budget constraints. Making the wrong choice can lead to premature failure or unnecessary expenses.
Comprehensive Comparison of Austenitic and Ferritic Stainless Steel Properties
Property | Austenitic (304) | Austenitic (316) | Ferritic (430) | Ferritic (441) | Industry Standard |
---|---|---|---|---|---|
Chromium Content (%) | 18-20 | 16-18 | 16-18 | 17-19.5 | Min. 10.5% |
Nickel Content (%) | 8-10.5 | 10-14 | 0-0.75 | 0-1.0 | Varies by type |
Tensile Strength (MPa) | 515-720 | 485-690 | 450-600 | 415-585 | 380-720 |
Magnetic Properties | Non-magnetic | Non-magnetic | Magnetic | Magnetic | Depends on structure |
Max Service Temp (°C) | 870 | 870 | 815 | 850 | 650-870 |
Corrosion Resistance | Good | Excellent | Moderate | Good | Application dependent |
HnL Steel supplies both austenitic and ferritic stainless steel that meet international standards including GB/T, ASTM, and JIS. Our technical team helps clients select the right type for their specific needs, ensuring optimal performance and cost-efficiency for global projects.
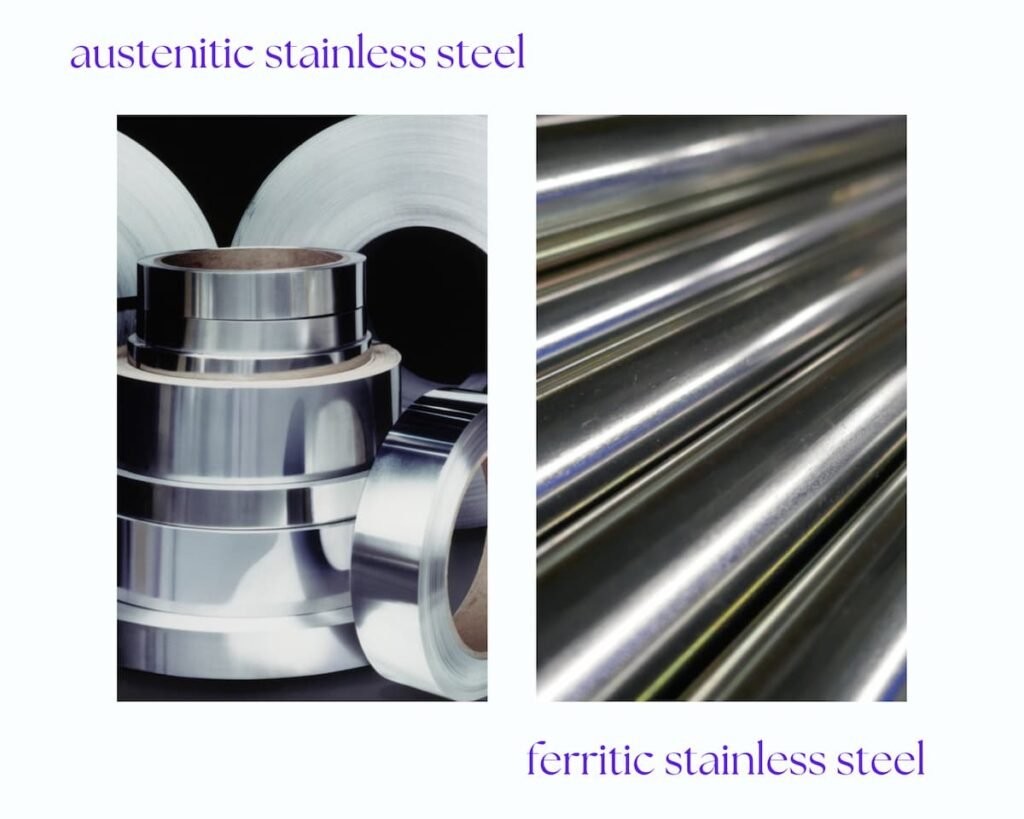
Chemical Composition and Structural Differences
Austenitic Stainless Steel: Nickel, Chromium, and Face-Centered Cubic Structure
Austenitic stainless steel derives its properties from a specific mix of metals. It contains high amounts of nickel (8-20%) and chromium (16-26%), creating a face-centered cubic (FCC) crystal structure. In this arrangement, atoms sit at cube corners and face centers. This structure gives austenitic stainless steel excellent formability, toughness at low temperatures, and non-magnetic properties. These qualities make it perfect for medical equipment, food processing, and chemical tanks where corrosion resistance is critical.
The chemical composition of stainless steel directly influences its microstructure, which determines its mechanical properties, corrosion resistance, and suitability for specific industrial applications.
Ferritic Stainless Steel: Lower Nickel, Higher Chromium, and Body-Centered Cubic Structure
Ferritic stainless steel contains minimal nickel (usually below 0.5%) while maintaining high chromium levels (10.5-30%). This composition creates a body-centered cubic (BCC) crystal structure, with atoms positioned at cube corners and the cube center. This structural arrangement gives ferritic steel excellent resistance to stress corrosion cracking but typically lower ductility than austenitic types. The reduced nickel content makes ferritic stainless steel more economical and less susceptible to price changes when nickel markets fluctuate.
Role of Alloying Elements in Performance
In any stainless steel comparison, understanding how specific elements affect performance is crucial. Chromium forms a protective oxide layer that provides basic corrosion resistance—more chromium means better protection. Nickel stabilizes the austenitic structure and improves formability. Molybdenum enhances resistance to pitting in harsh environments. Nitrogen increases strength in austenitic grades. Meanwhile, titanium and niobium in ferritic grades prevent chromium carbide formation during welding, reducing the risk of deterioration over time.
How Structure Impacts Material Behavior
The crystalline structure fundamentally determines material behavior under stress. Austenitic stainless steel’s FCC structure provides excellent ductility and toughness, allowing complex forming operations without cracking. It “handles like a champ” in fabrication shops due to its workability. The advantages of austenitic stainless steel over ferritic include better weldability, superior corrosion resistance, and higher temperature strength. Ferritic’s BCC structure offers better thermal conductivity and lower thermal expansion—valuable in heat exchangers and automotive exhaust systems. Additionally, ferritic grades are magnetic, while most austenitic varieties remain non-magnetic even after processing.
Detailed Comparison of Chemical Composition and Properties: Austenitic vs Ferritic Stainless Steel
Element/Property | Austenitic 304 | Austenitic 316 | Ferritic 430 | Ferritic 444 | Effect on Performance |
---|---|---|---|---|---|
Chromium (%) | 18-20 | 16-18 | 16-18 | 17-20 | Corrosion resistance, oxidation protection |
Nickel (%) | 8-10.5 | 10-14 | ≤0.75 | ≤1.0 | Structure stability, ductility improvement |
Molybdenum (%) | – | 2-3 | – | 1.75-2.5 | Pitting resistance, high-temperature strength |
Carbon (%) | ≤0.08 | ≤0.08 | ≤0.12 | ≤0.025 | Strength, hardness, weldability (lower is better) |
Nitrogen (%) | ≤0.10 | ≤0.10 | ≤0.05 | ≤0.035 | Strength enhancement, austenite stabilization |
Magnetic Properties | Non-magnetic | Non-magnetic | Magnetic | Magnetic | Equipment compatibility, EMI shielding |
At HnL Steel, we ensure consistent nickel and chromium content in all our stainless steel products. Our quality control processes monitor elemental composition throughout production, delivering materials that meet exact specifications under GB/T, ASTM, and JIS standards. This attention to composition ensures our clients receive materials with predictable performance, even in challenging environments where material integrity is critical to project success.
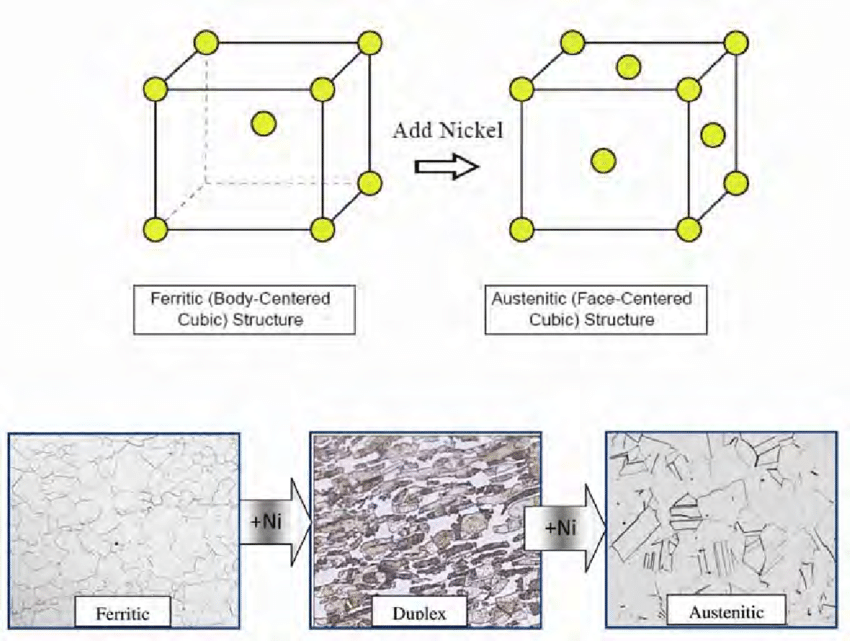
Mechanical Properties and Performance Comparison
Corrosion Resistance: Austenitic’s Edge in Harsh Environments
When it comes to fighting corrosion, austenitic stainless steel holds a significant advantage. Its higher nickel content creates a more stable passive layer that resists chemical attack. This makes it ideal for challenging environments like coastal installations, chemical processing facilities, and food production lines. Austenitic stainless steel performs exceptionally well in acidic conditions and against chloride attacks, which would quickly damage ordinary metals. The combination of chromium and nickel provides superior protection against pitting, crevice corrosion, and stress corrosion cracking—critical factors when designing equipment for long-term industrial applications.
The fundamental difference in mechanical properties between austenitic and ferritic stainless steels stems from their crystalline structures, with each type offering distinct advantages in specific operating environments.
Strength and Toughness: Nickel’s Impact on Austenitic Steel
Austenitic stainless steel typically offers better ductility and toughness than ferritic varieties. This superior formability comes from its face-centered cubic structure, allowing it to absorb significant impact without fracturing. The nickel content provides excellent work hardening properties, meaning it actually gets stronger when formed or bent. Meanwhile, ferritic stainless steel tends to have higher yield strength in its annealed condition but lacks the low-temperature toughness of austenitic grades. This makes ferritic options suitable for applications requiring rigidity without extreme impact resistance.
Temperature Tolerance: Ferritic’s Heat Resistance vs. Austenitic’s Cryogenic Strength
Temperature performance is where these materials show their specialized nature. Ferritic stainless steel “keeps its cool” with excellent resistance to high-temperature oxidation and thermal cycling. Its lower thermal expansion reduces warping in heat applications, making it perfect for automotive exhaust systems and heat exchangers. Conversely, austenitic stainless steel maintains its toughness even at cryogenic temperatures, making it one of the best use cases for austenitic stainless steel in liquid natural gas equipment and other ultra-cold environments where most metals would become dangerously brittle.
Magnetism and Formability: Practical Implications
Ferritic stainless steel is naturally magnetic, which can be either an advantage or limitation depending on the application. This magnetic property makes it unsuitable for environments sensitive to electromagnetic interference but beneficial for applications requiring magnetic attachment. Austenitic varieties are generally non-magnetic in their annealed state, though they may develop some magnetism when cold-worked. Regarding formability, austenitic stainless steel offers superior performance in deep drawing and stretching operations, while ferritic types may crack under severe forming.
Comprehensive Performance Property Comparison of Stainless Steel Types
Property | Austenitic 304 | Austenitic 316 | Ferritic 430 | Ferritic 444 | Application Impact |
---|---|---|---|---|---|
Tensile Strength (MPa) | 515-720 | 515-690 | 450-600 | 415-585 | Load capacity, structural integrity |
Yield Strength (MPa) | 205-310 | 205-310 | 275-450 | 275-415 | Resistance to permanent deformation |
Elongation (%) | 40-60 | 40-60 | 20-25 | 20-25 | Formability, ductility during fabrication |
Pitting Resistance (PREN) | 18-20 | 24-28 | 16-18 | 23-28 | Resistance to localized corrosion |
Thermal Conductivity (W/m·K) | 16.2 | 16.3 | 26.1 | 23.9 | Heat transfer efficiency |
Thermal Expansion (µm/m·°C) | 17.2 | 16.0 | 10.4 | 10.0 | Dimensional stability at varying temperatures |
At HnL Steel, we provide both austenitic and ferritic stainless steel tested to ensure consistent mechanical properties across all shipments. Our quality control measures include tensile testing, hardness evaluation, and corrosion resistance verification to international standards. This consistency is essential for engineers who must predict performance with absolute confidence. We understand that material reliability directly impacts safety margins and operational lifespans in critical industrial applications, which is why we maintain rigorous quality assurance protocols from sourcing through delivery.
Real-World Applications and Industry Use Cases
Austenitic in Precision Industries: Medical Devices and Food Processing
In environments where cleanliness is non-negotiable, austenitic stainless steel shines. Medical device manufacturers choose grades like 316L for surgical instruments, implants, and equipment frames due to its exceptional corrosion resistance and biocompatibility. The material withstands repeated sterilization without degradation. Similarly, food processing facilities rely on austenitic stainless steel for tanks, piping, and preparation surfaces. Its non-porous surface prevents bacterial growth, while its resistance to acidic foods and cleaning chemicals ensures long service life. These advantages of austenitic stainless steel over ferritic make it the standard for applications where hygiene and chemical resistance are paramount.
Both austenitic and ferritic stainless steels excel in specific applications, with selection criteria typically based on operating environment, cost considerations, and performance requirements rather than one type being universally superior.
Ferritic in Cost-Sensitive Sectors: Automotive Exhausts and Decorative Trims
The automotive industry has embraced ferritic stainless steel for exhaust systems, where its heat resistance, oxidation resistance, and lower cost provide significant advantages. Grades like 409 and 439 withstand the high temperatures and thermal cycling of exhaust gases without warping. Ferritic stainless steel also appears in decorative applications such as architectural trim, kitchen appliances, and consumer goods where its bright finish and magnetic properties offer practical benefits. The cost savings from lower nickel content makes ferritic grades “budget-friendly” for high-volume products while still delivering acceptable corrosion resistance in less demanding environments.
Case Study: Austenitic Steel in Marine Environments
A coastal desalination plant in Southeast Asia demonstrates why austenitic stainless steel dominates marine applications. Initially installed with standard carbon steel components, the facility faced rapid deterioration from saltwater exposure. After replacing critical components with 316L austenitic stainless steel, maintenance costs dropped by 60% and equipment downtime decreased by 85%. The superior chloride resistance of austenitic stainless steel prevented pitting and crevice corrosion despite constant exposure to seawater. This real-world example shows how proper material selection dramatically impacts operational efficiency and lifetime costs in harsh environments.
Case Study: Ferritic Steel in High-Heat Applications
A commercial bakery replaced their conventional steel conveyor systems with Grade 430 ferritic stainless steel and experienced immediate benefits. The ferritic stainless steel resisted oxidation at the bakery’s operating temperatures (up to 300°C) while maintaining dimensional stability due to its lower thermal expansion rate. Additionally, the magnetic properties allowed for easier attachment of sensors and monitoring devices. The bakery reported a 40% longer service life for their equipment and reduced maintenance intervals, demonstrating ferritic stainless steel’s value in high-temperature industrial applications where extreme corrosion resistance isn’t required.
Industry-Specific Applications and Material Selection Guide
Industry | Common Applications | Preferred Grade | Key Selection Factors | Alternative Option | Cost Consideration |
---|---|---|---|---|---|
Food Processing | Storage tanks, piping, preparation surfaces | 304 (Austenitic) | Sanitization requirements, acid resistance | 430 (Ferritic) for dry areas | Medium-high initial cost, low maintenance |
Automotive | Exhaust systems, trim components | 409/439 (Ferritic) | Heat resistance, cost efficiency | 301 (Austenitic) for structural parts | Low-medium initial cost, medium lifetime |
Chemical Processing | Reaction vessels, heat exchangers | 316/316L (Austenitic) | Chemical resistance, pressure tolerance | 444 (Ferritic) for less aggressive media | High initial cost, very low maintenance |
Marine/Offshore | Structural components, fasteners | 316L (Austenitic) | Chloride resistance, weldability | 2205 (Duplex) for higher strength | Very high initial cost, negligible maintenance |
Architectural | Facades, railings, decorative elements | 430/443 (Ferritic) | Appearance, weather resistance | 304 (Austenitic) for coastal areas | Medium initial cost, low maintenance |
HnL Steel supplies both austenitic and ferritic stainless steel products for these diverse industrial applications. Our extensive inventory includes specialized grades meeting international standards for marine environments, food-grade applications, and high-temperature systems. With fast delivery capabilities and customization options, we help clients select the optimal stainless steel type for their specific operating conditions, balancing performance requirements with budget considerations.
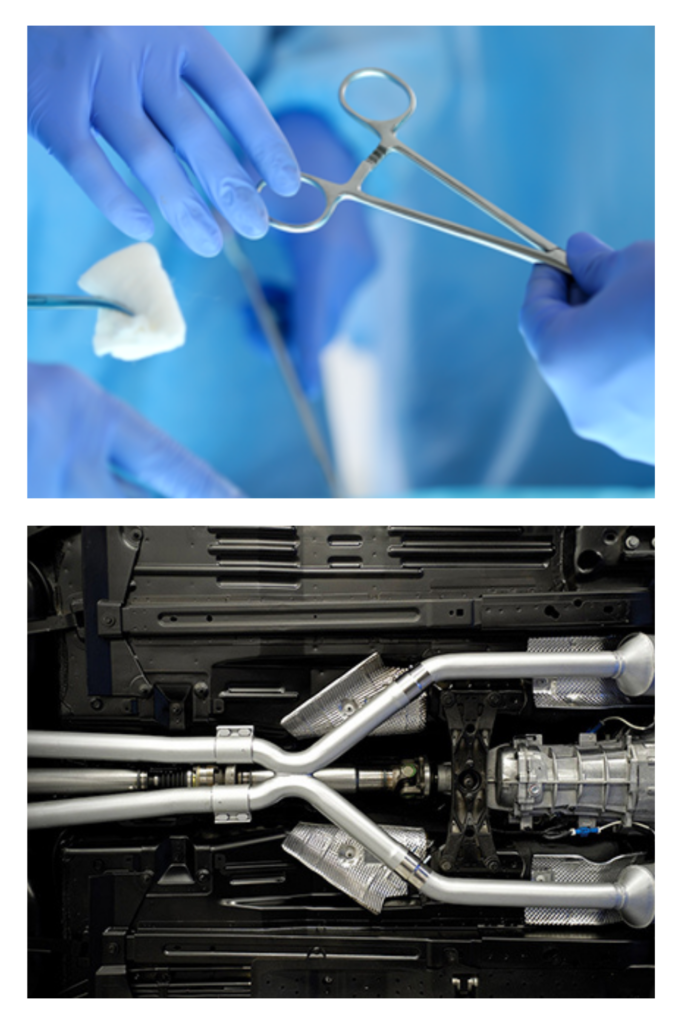
Choosing the Right Stainless Steel for Your Project
Decision Drivers: Strength, Corrosion Resistance, and Budget
Selecting the right type of stainless steel means balancing several key factors. Your decision should start with three main questions: How strong does the material need to be? What level of corrosion resistance do you require? And what’s your budget? Austenitic and ferritic stainless steels offer different advantages in each area. The environment where your material will operate matters greatly—chemicals, temperature changes, and moisture levels all affect performance. A stainless steel comparison should always include these factors to ensure you’re making an informed choice.
Selecting between austenitic and ferritic stainless steel requires balancing performance needs against budget constraints, with austenitic grades offering superior corrosion resistance for critical applications while ferritic grades provide cost-effective solutions for less demanding environments.
When to Choose Austenitic: High-Stakes Applications
Austenitic stainless steel shines in demanding environments where failure isn’t an option. Its excellent corrosion resistance makes it ideal for chemical processing equipment, food production machinery, and marine applications. The nickel content in austenitic stainless steel creates a stable structure that maintains strength across a wide temperature range. Choose austenitic grades like 304 or 316 when your application faces acidic conditions, chloride exposure, or needs to maintain cleanliness standards. These grades are among the best use cases for austenitic stainless steel when safety, hygiene, or reliability are “deal-breakers” in your project requirements.
When to Choose Ferritic: Cost-Effective Solutions
Ferritic stainless steel offers a more budget-friendly option without sacrificing quality for the right applications. With lower nickel content, ferritic grades cost substantially less while still providing good corrosion resistance in milder environments. Consider ferritic stainless steel for indoor applications, architectural elements, and automotive components that experience heat but not extreme chemical exposure. Grades like 430 and 441 perform well in high-temperature settings like heat exchangers and exhaust systems. The magnetic properties of ferritic steel can also be an advantage where this feature is desired.
Procurement Tips: Partnering with Suppliers like HnL Steel for Success
Finding the right supplier is as important as selecting the right material. Look for partners who offer both austenitic and ferritic options and can provide technical guidance. HnL Steel specializes in supplying various types of stainless steel that meet international standards including GB/T, ASTM, and JIS. When evaluating suppliers, consider their ability to provide material certifications, consistent quality, and responsive service. Established relationships with suppliers often lead to better pricing, priority delivery schedules, and technical support that can prevent costly mistakes.
Selection Guide for Stainless Steel Types by Application Requirements
Selection Factor | Austenitic Advantage | Ferritic Advantage | Critical for Industry | Cost Impact | Decision Weight |
---|---|---|---|---|---|
Corrosion Resistance | Superior (especially in chemicals) | Good (in atmospheric conditions) | Chemical, Food, Medical | Higher initial investment, lower maintenance | High |
Heat Resistance | Good up to 870°C | Better thermal conductivity | Automotive, Energy | Application-specific | Medium-High |
Formability | Excellent (deep drawing) | Limited (may crack) | Manufacturing, Construction | Higher fabrication costs for ferritic | Medium |
Magnetic Properties | Non-magnetic | Magnetic | Electronics, Medical Equipment | Minimal | Application-specific |
Material Cost | Higher (nickel content) | Lower (30-40% less) | All industries | Direct impact on project budget | High |
Weldability | Excellent | Good with precautions | Construction, Manufacturing | Higher labor costs for ferritic | Medium-High |
HnL Steel offers competitive pricing on both austenitic and ferritic stainless steel products while maintaining strict quality standards. Our commitment to honest, long-term relationships means we work closely with clients to understand their specific needs. Whether your project requires the superior corrosion resistance of austenitic grades or the cost-effectiveness of ferritic options, we provide reliable solutions backed by technical expertise and prompt delivery.

Conclusion
After diving into the world of stainless steel for over a decade, I can tell you picking between austenitic and ferritic isn’t just about specs—it’s about what your project demands. Austenitic’s my go-to for tough, corrosive environments; it’s got the resilience I trust for high-stakes jobs. Ferritic, though, wins when budgets tighten and heat’s the main challenge—it’s a **”no-brainer”** for cost-effective durability.
From my experience at HnL Steel, I’ve seen how the right choice shapes a project’s success. It’s not just metal—it’s the backbone of your work. So, weigh your needs: corrosion resistance, strength, or cost? That’s the key to making a call you won’t regret.
FAQ
Q1: What is austenitic stainless steel?
A1: Austenitic stainless steel is a type of iron-based alloy with high chromium and nickel content that forms an austenite crystalline structure. It is known for excellent corrosion resistance, formability, and strength, making it widely used in various industries.
Q2: How does austenitic stainless steel compare to ferritic stainless steel in terms of corrosion resistance?
A2: Austenitic stainless steel generally has superior corrosion resistance compared to ferritic stainless steel due to its higher nickel and chromium content.
Q3: What are the primary applications of austenitic stainless steel?
A3: Austenitic stainless steel is used in medical, automotive, aerospace, and industrial applications due to its strength, corrosion resistance, and formability.
Q4: What are the key characteristics of austenitic stainless steel?
A4: Key characteristics include non-magnetic properties, high ductility, and resistance to corrosion and temperature-induced scaling.
Q5: What are the main alloying elements in austenitic stainless steel?
A5: The main alloying elements are chromium (usually 16-26%) and nickel (8-20%). Some grades also include molybdenum and manganese.
Q6: Is austenitic stainless steel suitable for high-temperature environments?
A6: Yes, austenitic stainless steel can maintain its integrity and strength at elevated temperatures, making it suitable for heat-resistant applications.
Q7: What are the differences between 304 and 316 austenitic stainless steel?
A7: The main difference is that 316 contains molybdenum, which gives it increased corrosion resistance, especially against chlorides and chlorinated environments, making it more costly than 304.
Q8: Why does austenitic stainless steel have good formability?
A8: Austenitic stainless steel has good formability due to its face-centered cubic crystal structure and high ductility, which allows it to be formed into complex shapes without losing strength.
External Links
- What is Austenitic Stainless Steel? – Ulbrich
- A Comprehensive Guide to Austenitic Stainless Steel – Enze Mfg
- Austenitic Stainless Steel: Definition, Composition, Properties, Grades
- Austenitic stainless steel – Wikipedia
- Austenitic Stainless Steel – Density – Strength – Hardness – Melting Point
- Austenitic vs Ferritic Stainless Steel: Key Differences and…
- Austenitic Stainless Steel: Properties, Applications, and Advancements…
- Understanding Austenitic Stainless Steel: Key Grades
2 Responses