Introduction
Corrosion and structural failures plague construction, threatening safety and spiking maintenance costs. For structural engineers and contractors, finding materials that endure harsh conditions without breaking the bank is a constant battle.
That’s where coated steel steps in. With coatings like zinc or aluminum, it fights rust, boosts load-bearing strength, and keeps large-scale projects stable for the long haul. This article breaks down how HnL Steel’s reliable supply and quality assurance make it a top choice for reinforcing infrastructure.
The Fundamentals of Coated Steel in Construction
Coated steel represents one of the most versatile and reliable building materials in modern construction. This engineered material combines the inherent strength of steel with specialized protective layers that significantly enhance its performance in demanding environments. Understanding these fundamentals is essential for architects, engineers, and construction professionals looking to optimize structural integrity.
“Coated steel in construction provides superior corrosion resistance while maintaining the structural strength of traditional steel, extending infrastructure lifespan by 15-25 years compared to uncoated alternatives.”
What is Coated Steel? Defining Its Protective Layers
At its core, coated steel consists of a carbon steel substrate with one or more protective layers applied to its surface. These coatings typically include zinc (galvanized), aluminum-zinc alloy (Aluzinc), or polymer-based materials. Each layer serves a specific function in the protection system, working together to create a “bulletproof vest” for the underlying steel.
The primary coating acts as a sacrificial layer, corroding preferentially to protect the base metal. Secondary layers often provide additional barrier protection, preventing moisture and corrosive elements from reaching the steel substrate. This multi-layer approach creates a comprehensive defense system that significantly extends the material’s service life.
How Coatings Enhance Steel’s Core Properties
The application of specialized coatings transforms ordinary steel into a superior construction material. Beyond corrosion resistance, these treatments can enhance fire resistance, thermal performance, and even aesthetic appeal. The right coating system can maintain steel’s structural integrity in environments that would quickly degrade unprotected metal.
Corrosion resistant steel exhibits significantly lower maintenance requirements compared to uncoated alternatives. This translates to reduced lifecycle costs and fewer disruptions during a structure’s operational life. The coating’s ability to prevent oxidation also maintains the steel’s dimensional stability, ensuring consistent performance over decades.
Comparative Performance of Different Steel Coating Systems
Coating Type | Corrosion Resistance (Years) | Temperature Tolerance (°C) | Impact Resistance | Initial Cost Factor | Lifecycle Cost Savings |
---|---|---|---|---|---|
Uncoated Steel | 2-5 | 550 | High | 1.0x | Baseline |
Hot-Dip Galvanized | 20-30 | 200 | High | 1.3x | 35-45% |
Zinc-Aluminum (Aluzinc) | 25-40 | 315 | Medium-High | 1.5x | 40-55% |
Epoxy-Coated | 15-25 | 120 | Medium | 1.4x | 25-40% |
Powder-Coated | 15-20 | 150 | Medium-Low | 1.6x | 30-45% |
Multi-Layer Premium System | 40-60 | 400 | Very High | 2.0x | 50-70% |
The Role of Coated Steel in Modern Construction
Coated steel has become indispensable in contemporary building projects, particularly in infrastructure that faces harsh environmental conditions. From bridges and highways to coastal buildings and industrial facilities, this material provides the durability needed for critical structures with minimal maintenance requirements.
Modern construction relies on coated steel to deliver predictable performance throughout a structure’s intended lifespan. The material’s resistance to moisture, chemical exposure, and temperature fluctuations makes it ideal for applications where failure could have serious consequences. This reliability factor explains why coated steel remains the go-to choice for projects where structural integrity cannot be compromised.
Why Structural Engineers Trust Coated Steel
Structural engineers specify coated steel when they need dependable performance under demanding conditions. The material’s proven track record in how coated steel improves structural integrity makes it a preferred choice for load-bearing components in everything from skyscrapers to bridges. Its consistent mechanical properties allow for precise calculations and predictable behavior under stress.
HnL Steel specializes in supplying high-quality coated steel sheets engineered specifically for these demanding applications. Their products undergo rigorous quality control to ensure they meet or exceed international standards for structural performance. This attention to detail makes their materials particularly suitable for large-scale infrastructure projects where reliability is paramount.
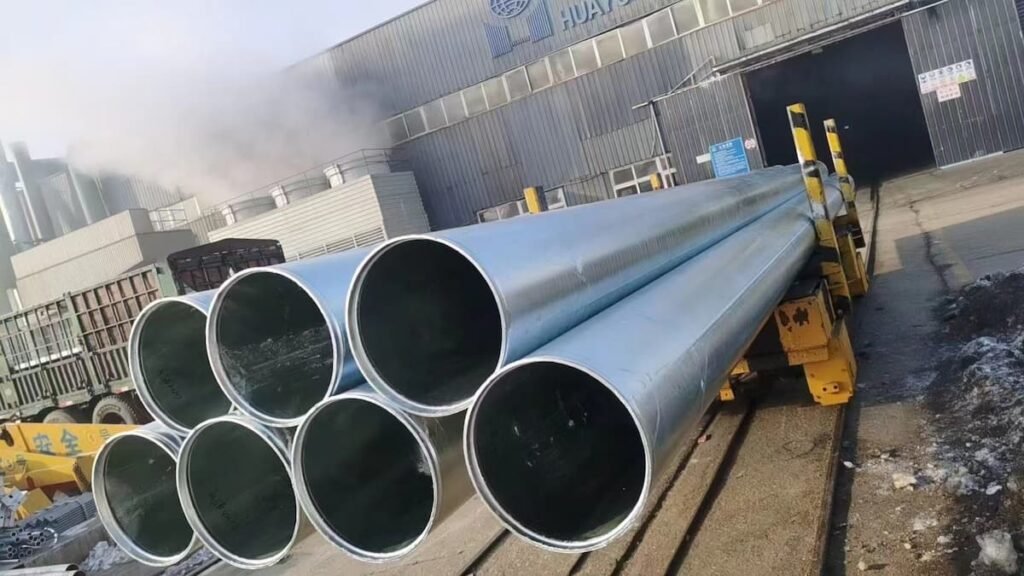
Types of Coatings for Steel: Options and Benefits
The protective coating applied to steel can dramatically alter its performance characteristics, making coating selection a critical decision in construction projects. Various coating technologies offer different advantages in terms of corrosion resistance, durability, and performance in specific environments. Understanding these options helps engineers and builders select the optimal solution for each application.
“Steel coatings extend structural lifespan by creating sacrificial or barrier protection, with each coating type offering specific benefits for different environmental challenges and performance requirements.”
Galvanized Steel: Zinc Coating for Corrosion Resistance
Zinc coated steel remains one of the most widely used protective systems in construction. The zinc layer creates a sacrificial barrier that corrodes preferentially, protecting the underlying steel. This electrochemical protection continues even when small areas of the coating are damaged, as the zinc migrates to cover exposed steel surfaces.
Hot-dip galvanizing creates the most durable zinc coating, with typical thicknesses ranging from 45-200 microns depending on the application requirements. These coatings can provide 50+ years of maintenance-free performance in moderate environments. For less demanding applications, continuous galvanizing processes produce thinner coatings suitable for “everyday heroes” like roofing, siding, and interior structural components.
Aluminized Steel: Heat and Wear Protection
Aluminized steel offers exceptional performance in high-temperature environments. The aluminum coating forms a stable oxide layer that resists scaling and maintains integrity at temperatures up to 800°C. This makes aluminized steel ideal for exhaust systems, heat shields, and industrial equipment exposed to elevated temperatures.
Beyond thermal resistance, aluminized coatings provide excellent reflectivity, reducing heat absorption and improving energy efficiency in building envelopes. The coating also delivers solid corrosion protection, though typically not as robust as galvanized steel in standard atmospheric conditions. For specialized applications requiring both heat and corrosion resistance, aluminized steel provides an optimal balance of properties.
Comparative Performance of Steel Coating Technologies
Coating Type | Corrosion Resistance | Heat Resistance (°C) | UV Stability | Chemical Resistance | Relative Cost |
---|---|---|---|---|---|
Hot-Dip Galvanized | Excellent | 200 | Good | Moderate (pH 6-12) | Medium |
Aluminized Type 1 | Good | 800 | Excellent | Good (Low Sulfur) | Medium-High |
Aluminized Type 2 | Very Good | 650 | Excellent | Moderate | Medium-High |
Zinc-Aluminum (55%) | Superior | 315 | Very Good | Good | High |
Zinc-Aluminum (5%) | Very Good | 250 | Good | Good | Medium-High |
Polymer-Coated | Excellent | 120 | Variable | Excellent | Highest |
Zinc-Aluminum Alloys: Balancing Strength and Aesthetics
Zinc-aluminum alloy coatings represent a significant advancement in coated steel technology. By combining zinc’s sacrificial protection with aluminum’s barrier properties, these coatings deliver superior performance in challenging environments. Formulations typically contain 5-55% aluminum, with higher aluminum content providing enhanced corrosion resistance.
These hybrid coatings offer 2-4 times the lifespan of standard galvanized steel in similar environments. The aluminum component creates a more stable passive layer that resists breakdown in industrial and coastal settings. HnL Steel’s Aluzinc coils exemplify this technology, providing exceptional durability while maintaining the formability needed for complex structural components.
Choosing the Right Coating for Environmental Challenges
Selecting the optimal coatings for steel against corrosion requires careful assessment of environmental factors. Coastal environments demand highly resistant coatings due to constant salt spray exposure. Urban and industrial settings introduce different challenges, with chemical pollutants and acid rain accelerating corrosion of inadequately protected steel.
Beyond environmental factors, functional requirements influence coating selection. Load-bearing structures benefit from thicker, more durable coatings, while decorative elements might prioritize appearance and finish quality. HnL Steel offers customization capabilities across their product range, ensuring engineers can match coating specifications precisely to project requirements and expected service conditions.
Advantages of Coated Steel for Structural Reinforcement
Structural reinforcement demands materials that deliver exceptional performance under demanding conditions. Coated steel has emerged as a premier solution for engineers and contractors seeking to enhance building durability while maintaining structural integrity. The strategic application of protective coatings transforms standard steel into a superior construction material with significantly extended service life.
“Coated steel in structural applications can extend infrastructure lifespan by 30-50 years while reducing maintenance costs by up to 40% compared to unprotected steel alternatives.”
Superior Corrosion Resistance for Longevity
Corrosion represents the primary threat to steel structures, potentially compromising both safety and aesthetics over time. Corrosion resistant steel addresses this vulnerability through specialized coatings that create both barrier and sacrificial protection. These coatings isolate the base metal from environmental factors while providing electrochemical defense against oxidation processes.
In coastal environments, where salt-laden air accelerates deterioration, properly coated steel can maintain structural integrity for decades without significant intervention. HnL Steel’s coating processes ensure comprehensive protection by controlling coating thickness, adhesion, and uniformity – critical factors that determine long-term performance in challenging environments. Their products are “tough as nails” even in the most demanding settings.
Enhanced Load-Bearing Strength Under Stress
While uncoated steel offers excellent initial strength, its load-bearing capacity can degrade as corrosion progresses. Coated steel maintains its structural properties throughout its service life, ensuring consistent performance under mechanical stress. This durability translates to safer buildings and infrastructure with predictable performance characteristics even decades after installation.
The protective coatings prevent section loss that would otherwise reduce effective thickness and compromise load distribution. In reinforced concrete applications, coated rebar maintains its bond strength with surrounding concrete, preventing the expansive corrosion that leads to cracking and spalling. This preservation of structural integrity is paramount in regions with seismic activity or extreme weather events.
Performance Comparison of Structural Steel Systems
Performance Metric | Unprotected Steel | Painted Steel | Hot-Dip Galvanized | Zinc-Aluminum Coated | Duplex System |
---|---|---|---|---|---|
Service Life (Moderate Environment) | 5-7 years | 10-15 years | 50+ years | 60+ years | 75+ years |
Load Capacity Retention (25yr) | 70-80% | 85-90% | 98-100% | 99-100% | 99-100% |
Maintenance Frequency | Every 2-3 years | Every 5-7 years | 15-20 years | 20+ years | 25+ years |
Initial Cost Index | 1.0 | 1.2 | 1.4 | 1.5 | 1.7 |
Lifecycle Cost Index (50yr) | 3.0 | 2.2 | 1.5 | 1.4 | 1.3 |
Aesthetic Appeal Meets Functional Resilience
Modern architectural design often exposes structural elements as visual features. Metal coated construction materials offer the perfect blend of form and function, providing both aesthetic appeal and structural performance. These materials come in various finishes and colors, allowing designers to incorporate exposed structural elements without compromising the visual concept.
The benefits of coated steel in construction extend beyond mere practicality. Contemporary buildings often feature exposed steel as design elements, and coating technologies allow these components to maintain their appearance without developing unsightly rust or degradation. This durability of appearance contributes to maintaining property values and reducing the need for cosmetic renovations over time.
Cost Savings Through Reduced Maintenance
The initial investment in quality coated steel yields substantial long-term financial benefits. Structures utilizing these materials require significantly less maintenance, avoiding costly repairs, scaffolding, business disruptions, and reapplication of protective systems. This lifecycle approach to cost assessment demonstrates the superior economic value of properly protected steel.
HnL Steel’s quality assurance processes ensure their coated products meet or exceed international standards, providing confidence in long-term performance. Their focus on delivering materials that drive contractor profitability aligns with the economic benefits of reduced maintenance cycles. By eliminating frequent recoating or replacement needs, projects utilizing these high-performance materials deliver better return on investment throughout their operational lifespan.
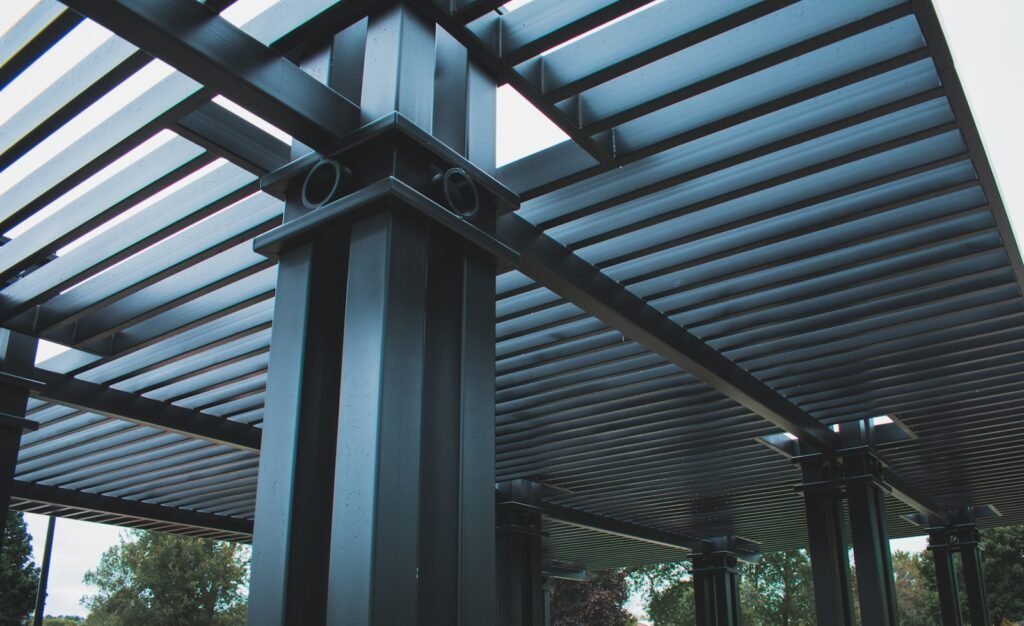
Real-World Applications of Coated Steel in Infrastructure
The theoretical advantages of coated steel translate into remarkable performance in real-world infrastructure projects. From towering skyscrapers to expansive bridges, these materials have proven their value in the most demanding applications. Examining actual implementations provides valuable insights into how engineers leverage these materials to overcome significant structural and environmental challenges.
“Properly specified coated steel in infrastructure applications can reduce lifetime maintenance costs by 30-40% while extending service life by decades compared to traditional unprotected alternatives.”
Bridges and Highways: Stability in Harsh Conditions
Bridge structures represent one of the most challenging applications for construction materials, facing constant exposure to weather, traffic vibration, and often corrosive environments. Galvanized steel has revolutionized bridge construction by providing long-term protection against these elements. The Millau Viaduct in France and the Hong Kong-Zhuhai-Macau Bridge exemplify how coated steel enables both structural integrity and impressive spans in demanding settings.
Highway infrastructure similarly benefits from steel coatings that protect against road salt, moisture, and temperature fluctuations. Guardrails, sign structures, and reinforcement in concrete roadways all incorporate protective coatings to ensure decades of reliable service. These applications demonstrate how coated steel improves structural integrity even under the “daily grind” of heavy traffic and environmental assault.
High-Rise Buildings: Strength and Visual Appeal
Modern skyscrapers rely heavily on coated steel for both their primary structure and architectural features. The Burj Khalifa in Dubai incorporates specially coated structural steel to withstand the region’s extreme heat and sand-laden winds. Similarly, Beijing’s CCTV Headquarters features exposed structural elements with advanced protective systems that preserve both appearance and structural properties.
Beyond structural applications, architectural elements such as façade systems frequently utilize coated steel for both aesthetic appeal and durability. These applications highlight the dual benefits of these materials – delivering both visual impact and long-term performance. The coating technologies allow architects to incorporate exposed steel elements without worrying about degradation or discoloration over time.
Infrastructure Applications and Performance Metrics
Application | Coating Type | Typical Service Life | Environmental Challenge | Key Performance Benefit | ROI Factor |
---|---|---|---|---|---|
Bridge Structures | Hot-Dip Galvanized | 75+ years | Marine/Road Salt | Minimal Maintenance | 3.2x |
Highway Guardrails | Continuous Galvanized | 30+ years | Impact/Road Spray | Impact Resistance | 2.7x |
High-Rise Structures | Zinc-Aluminum Alloy | 50+ years | Urban Pollution | Fire Resistance | 2.5x |
Industrial Platforms | Thermally Sprayed Zinc | 25+ years | Chemical Exposure | Chemical Resistance | 3.0x |
Coastal Infrastructure | Duplex System | 60+ years | Salt Spray/UV | Corrosion Prevention | 3.8x |
Transmission Towers | Hot-Dip Galvanized | 80+ years | Remote Locations | Low Maintenance Need | 4.1x |
Industrial Facilities: Durability Under Heavy Loads
Industrial environments present some of the most aggressive conditions for structural materials. Chemical processing plants, power generation facilities, and manufacturing operations all rely on galvanized steel and other coated metals to withstand corrosive atmospheres while supporting heavy equipment. These facilities demonstrate the critical role of proper material selection in ensuring both safety and operational continuity.
Petrochemical facilities often utilize specialized coating systems to protect against specific chemical exposures. The BASF plant in Ludwigshafen, Germany, incorporates multiple protective systems based on exposure zones, optimizing both performance and cost-effectiveness. HnL Steel’s fast delivery capabilities and flexible payment terms make them an ideal partner for these complex projects with ambitious timelines and precise material specifications.
Emerging Trends in Coated Steel Usage
The infrastructure sector continues to develop innovative applications for coated steel. Modular construction techniques increasingly rely on factory-finished coated components that arrive at the job site ready for rapid assembly. This approach reduces field welding and touch-up requirements while accelerating project timelines – a significant advantage for time-sensitive infrastructure projects.
Sustainability considerations are also driving new applications, with lifecycle assessment demonstrating the environmental benefits of durable coated steel. The recyclability of these materials, combined with their extended service life, contributes to reduced environmental impact compared to alternatives requiring frequent replacement. This alignment with green building principles is expanding the material’s use in environmentally conscious projects worldwide.
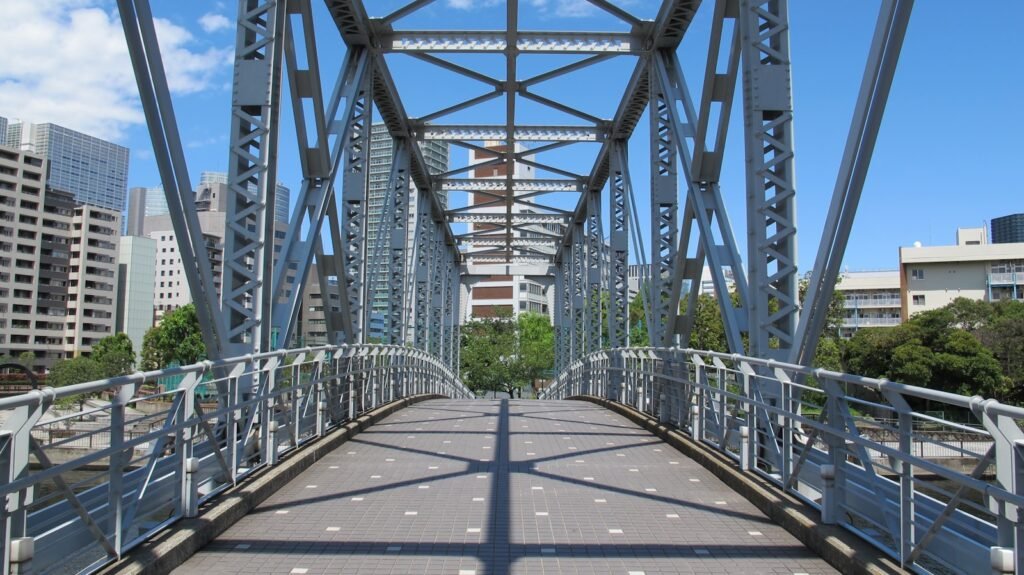
Integrating Coated Steel into Your Next Project
Selecting the right materials for construction projects involves balancing performance requirements, budget constraints, and long-term sustainability goals. Integrating coated steel into your building plans requires careful consideration of environmental factors, load requirements, and aesthetic considerations. This practical guidance will help engineers and contractors make informed decisions when specifying these high-performance materials.
“Proper selection and procurement of coated steel can reduce maintenance costs by up to 40% over a structure’s lifetime while ensuring optimal performance in challenging environments.”
Assessing Project Needs: Coating Type and Thickness
The first step in material selection involves thoroughly analyzing your project’s specific requirements. Environmental exposure represents the primary consideration – coastal locations demand more robust protection than inland sites, while industrial zones may require specialized chemical resistance. Temperature fluctuations, UV exposure, and expected service life all influence the optimal coating specification.
Coating thickness directly correlates with protection duration, but thicker isn’t always better. Excessively thick coatings may affect formability or welding characteristics, potentially complicating fabrication. Corrosion resistant steel options should be evaluated based on both initial performance requirements and anticipated maintenance schedules. HnL Steel can provide detailed guidance on optimal thickness specifications for your specific application environment.
Comparing Coated Steel to Alternatives
When evaluating material options, comparing coated steel against alternatives such as stainless steel, aluminum, or composite materials provides valuable perspective. The benefits of coated steel in construction include exceptional strength-to-weight ratios, durability in demanding environments, and typically lower initial and lifecycle costs compared to alternatives offering similar performance.
Metal coated construction materials offer particular advantages in applications requiring both strength and corrosion resistance. While stainless steel provides excellent corrosion protection, its higher cost can be prohibitive for large-scale projects. Coated carbon steel delivers comparable performance at a fraction of the cost for many applications, making it the “smart money” choice for budget-conscious projects without compromising quality.
Material Selection Decision Matrix for Construction Projects
Selection Criteria | Coated Steel | Stainless Steel | Aluminum | Concrete | Timber |
---|---|---|---|---|---|
Initial Cost ($/m²) | 45-80 | 120-250 | 65-110 | 30-65 | 40-90 |
Lifecycle Cost (50yr) | Medium | Low | Medium | Medium-High | High |
Strength-to-Weight | Excellent | Excellent | Good | Poor | Good |
Corrosion Resistance | Very Good | Excellent | Good | Excellent | Poor |
Fire Resistance | Good | Excellent | Poor | Excellent | Poor |
Sustainability Index | High | Medium | Medium | Low | Very High |
Procurement Tips: Sourcing Reliable Suppliers
Finding dependable suppliers represents a critical aspect of successful project execution. When sourcing coated steel products, verify that manufacturers follow international standards such as ASTM A653 for galvanized steel or EN 10346 for continuously coated products. Request test certificates documenting coating weight, adhesion, and uniformity to ensure you receive materials meeting your specifications.
Delivery timelines can significantly impact project schedules, making supplier reliability as important as material quality. Establishing relationships with suppliers capable of meeting tight deadlines provides valuable flexibility when projects face unexpected challenges. Additionally, consider suppliers offering technical support during both specification and implementation phases to maximize value.
Partnering with HnL Steel for Optimal Results
HnL Steel has established itself as a trusted partner for construction professionals worldwide, offering comprehensive solutions for structural reinforcement needs. Their global supply chain capabilities ensure consistent availability even for large-scale projects, while their technical expertise helps clients navigate complex material decisions with confidence. Their commitment to quality assurance means every shipment meets rigorous standards.
The company’s flexible payment terms and expedited delivery options accommodate diverse project requirements and timeline constraints. By focusing on building long-term relationships rather than transactional sales, HnL Steel delivers both immediate value and ongoing support throughout your project lifecycle. Their diverse product catalog ensures you’ll find precisely the right specifications for your unique application requirements.
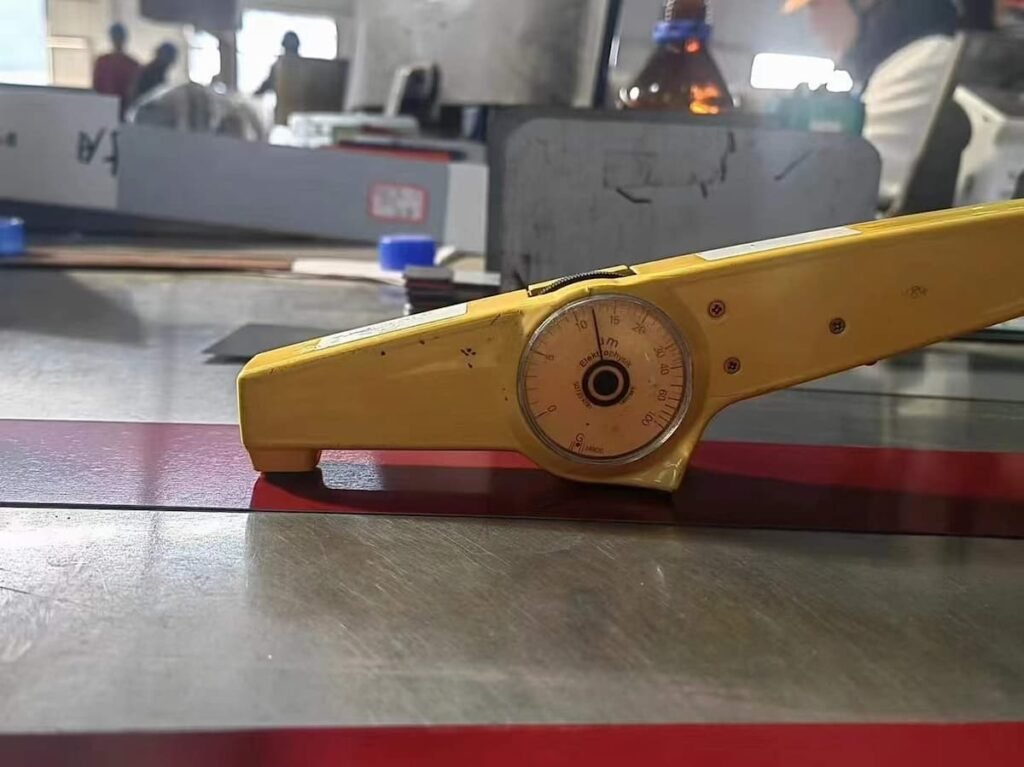
Conclusion
After a decade in the steel game, I’ve seen firsthand how coated steel changes the equation for structural integrity. It’s not just about slapping on a protective layer—it’s about giving buildings and bridges the stamina to stand tall against rust, stress, and time.
For me, the real win is knowing a material like this keeps projects safe and solid for decades. HnL Steel’s focus on quality and reliable supply only seals the deal—pun intended. It’s the kind of partnership I trust to deliver.
So, if you’re planning your next build, I’d say opting for coated steel is a “no-brainer”. It’s about building something that lasts—something you can point to years from now and say, ‘Yeah, I got that right.’
FAQ
Q1: What are the main benefits of coated steel?
A1: Coated steel offers superior protection against corrosion and environmental damage, extending the life of steel structures. It also provides aesthetic flexibility and reduces maintenance costs.
Q2: How does zinc coating enhance the performance of steel?
A2: Zinc coating acts as a sacrificial anode, providing protection against corrosion even at cut edges and scratches. It prolongs steel durability, especially in harsh environments.
Q3: Why is coated steel preferred in construction?
A3: Coated steel is preferred in construction for its increased durability, reduced maintenance, and aesthetic versatility. It offers protection against corrosion, which is critical in structural applications.
Q4: What types of coatings are commonly used for steel?
A4: Common types of coatings include galvanization, aluminizing, and the use of alloys like Zinc-Aluminum-Magnesium. These coatings offer varying degrees of corrosion protection and resistance to environmental factors.
Q5: How does aluminum coating benefit steel?
A5: Aluminum coating provides excellent heat and corrosion resistance, making it ideal for applications exposed to high temperatures and chemical exposure.
Q6: Are there environmental advantages to using coated steel?
A6: Yes, coated steel can extend the lifespan of products, reducing the need for replacement and minimizing waste. Some coatings, like Zinc-Aluminum-Magnesium, are also eco-friendly in production.
Q7: What industries benefit most from using coated steel?
A7: The construction, automotive, and manufacturing industries benefit significantly from coated steel due to its durability, cost-effectiveness, and protective properties.
Q8: Is coated steel cost-effective compared to other materials?
A8: Yes, while initial costs may be higher, coated steel offers long-term savings by reducing maintenance and replacement costs, making it more cost-effective over time.
External Links
- Coated Steel: Resistant, Useful, and Aesthetic – Ternium
- Coated steel – stavianmetal.com
- Coated Steel Products & Sheet & Coil Supplier – Alliance Steel
- Coated Steel – Randall Metals Corporation
- Coated Metals Group
- Coated steel makes steel stand up to corrosion – SSAB
- Vietnam Coated Steel
- Best Protective Coatings for Steel: Protect Against Corrosion and Wear
5 Responses