Introduction
High temperatures can wreak havoc on industrial materials, threatening structural integrity and safety in settings like furnaces and reactors. For engineers and managers, finding a material that endures extreme heat without failing is a top priority.
That’s where coated steel shines. With specialized heat-resistant coatings, it delivers durability and corrosion resistance, making it a trusted choice for demanding applications. This article dives into how coated steel performs in high-heat environments, why it matters, and what you need to know to choose the right solution.
Introduction to Coated Steel in High-Heat Environments
In industrial settings, materials face extreme conditions, especially when exposed to high temperatures. This is where coated steel steps in as a ride-or-die solution. Coated steel is engineered to withstand harsh environments, making it a cornerstone for industries like construction, manufacturing, and energy. Its ability to maintain structural integrity under intense heat ensures safety, durability, and cost-efficiency for large-scale projects.
“Coated steel is a game-changer in high-heat environments, offering unmatched durability and protection for industrial applications.”
Why High Temperatures Challenge Industrial Materials
High temperatures can wreak havoc on traditional materials. Metals like untreated steel are prone to corrosion, warping, and weakening when exposed to heat. This not only compromises safety but also increases maintenance costs. Industries need materials that can endure these conditions without frequent replacements or repairs.
What is Coated Steel? A Quick Overview
Coated steel is steel that has been treated with protective layers to enhance its performance. These coatings, often made of zinc, aluminum, or specialized polymers, act as a shield against heat, corrosion, and wear. The result is a material that combines the strength of steel with the resilience of advanced coatings.
The Role of Heat-Resistant Coatings in Enhancing Steel Performance
Heat-resistant coatings are the secret sauce that makes coated steel so effective. These coatings are designed to reflect heat, reduce thermal expansion, and prevent oxidation. For example, Aluzinc-coated steel can withstand temperatures up to 315°C (600°F), making it ideal for industrial applications like boilers, chimneys, and furnaces.
Why Industrial Professionals Rely on Coated Steel
Industrial professionals trust coated steel because it delivers consistent performance under extreme conditions. Its durability reduces downtime, while its heat-resistant properties ensure long-term reliability. Suppliers like HL Steel Trading provide high-quality coated steel sheets, ensuring that projects stay on schedule without compromising quality.
Coated Steel Performance in High-Heat Environments
Feature | Untreated Steel | Coated Steel | Industry Standard |
---|---|---|---|
Heat Resistance (°C) | 200 | 315 | 300 |
Corrosion Resistance | Low | High | High |
Lifespan (Years) | 5-10 | 20+ | 15+ |
Maintenance Frequency | High | Low | Moderate |
Cost Efficiency | Low | High | Moderate |
This table highlights the superior performance of coated steel compared to untreated steel, emphasizing its value in high-heat environments.
Benefits of Heat-Resistant Coated Steel
In industrial environments, materials must endure extreme conditions, and coated steel stands out as a reliable solution. Its heat-resistant properties make it indispensable for applications like manufacturing, construction, and energy production. By combining durability, safety, and cost-efficiency, coated steel ensures long-term performance in even the harshest settings.
“Heat-resistant coated steel offers unmatched protection and longevity, making it a top choice for industrial professionals.”
Heat Resistance: Withstanding Extreme Temperatures
One of the standout features of coated steel is its ability to handle extreme heat. Specialized coatings, such as Aluzinc, can withstand temperatures up to 315°C (600°F). This makes it ideal for use in boilers, furnaces, and chimneys, where traditional materials would fail.
Corrosion Resistance: Longevity in Harsh Conditions
Corrosion is a major concern in industrial settings, but coated steel addresses this issue head-on. Its protective layers prevent rust and degradation, even in humid or chemically aggressive environments. This extends the lifespan of structures and reduces the need for frequent replacements.
Enhanced Steel Durability for Safety Compliance
Safety is paramount in industrial applications, and coated steel delivers. Its enhanced durability ensures structural integrity under high stress and heat, meeting stringent safety standards. This reliability minimizes risks and protects both workers and equipment.
Environmental and Cost-Saving Benefits of Reduced Maintenance
Coated steel’s longevity translates to significant cost savings. By reducing the need for maintenance and replacements, it lowers operational expenses. Additionally, its durability contributes to sustainability by minimizing waste and resource consumption.
Performance Comparison: Coated Steel vs. Untreated Steel
Feature | Untreated Steel | Coated Steel | Industry Standard |
---|---|---|---|
Heat Resistance (°C) | 200 | 315 | 300 |
Corrosion Resistance | Low | High | High |
Lifespan (Years) | 5-10 | 20+ | 15+ |
Maintenance Frequency | High | Low | Moderate |
Cost Efficiency | Low | High | Moderate |
This table highlights the superior performance of coated steel, emphasizing its value in industrial applications.
Types of Coatings for Industrial Steel
When it comes to industrial applications, choosing the right coating for steel is crucial. Different coatings offer unique properties, making them suitable for specific high-heat environments. From aluminized coatings for furnaces to ceramic coatings for extreme temperatures, understanding these options helps professionals make informed decisions.
“Selecting the right coating for steel ensures durability, safety, and cost-efficiency in high-heat industrial applications.”
Aluminized Coatings: Ideal for Furnaces and Exhaust Systems
Aluminized coatings are a popular choice for environments like furnaces and exhaust systems. These coatings combine aluminum and silicon, providing excellent heat resistance and corrosion protection. They can withstand temperatures up to 677°C (1,250°F), making them ideal for high-heat applications.
Ceramic Coatings: Maximum Heat Thresholds
For industries requiring extreme heat resistance, ceramic coatings are the go-to solution. These coatings can handle temperatures exceeding 1,000°C (1,832°F), making them perfect for aerospace and energy sectors. Their thermal insulation properties also reduce energy consumption, adding to their appeal.
Zinc and Polymer-Based Coatings: Versatility and Customization
Zinc and polymer-based coatings offer versatility and customization. Zinc coatings provide excellent corrosion resistance, while polymer-based options allow for tailored solutions. These coatings are ideal for industries needing flexibility, such as automotive and construction.
Comparing Coating Durability and Heat Resistance
Understanding the durability and heat resistance of different coatings is key to selecting the right one. For example, aluminized coatings excel in moderate heat, while ceramic coatings are better for extreme temperatures. Zinc and polymer-based coatings offer a balance of durability and customization.
Coating Performance Comparison
Coating Type | Heat Resistance (°C) | Corrosion Resistance | Common Applications |
---|---|---|---|
Aluminized | 677 | High | Furnaces, Exhaust Systems |
Ceramic | 1,000+ | Very High | Aerospace, Energy |
Zinc | 200 | Moderate | Automotive, Construction |
Polymer-Based | 150 | High | Custom Industrial Solutions |
This table provides a clear comparison of coating types, helping professionals choose the best option for their needs.
Coating Methods and Their Impact
Applying coatings to steel is a precise process that significantly impacts its performance and durability. Different methods, such as hot-dip galvanizing and thermal spraying, offer unique benefits and challenges. Understanding these techniques helps professionals choose the best approach for their specific needs.
“The right coating method enhances steel’s durability and performance, ensuring long-term reliability in industrial applications.”
Hot-Dip Galvanizing: Process and Benefits
Hot-dip galvanizing involves immersing steel in molten zinc, creating a thick, durable coating. This method provides excellent corrosion resistance and is ideal for outdoor structures like bridges and pipelines. Its cost-effectiveness and long lifespan make it a popular choice for many industries.
Thermal Spraying: Precision for Extreme Conditions
Thermal spraying uses high heat to apply coatings like ceramics or metals onto steel surfaces. This method offers precision and versatility, making it suitable for extreme conditions in aerospace and energy sectors. Its ability to create custom coatings ensures optimal performance for specialized applications.
How Coating Techniques Affect Steel Properties
Different coating techniques impact steel properties in various ways. For example, hot-dip galvanizing enhances corrosion resistance, while thermal spraying improves heat resistance. Understanding these effects helps professionals select the right method for their specific requirements.
Balancing Cost and Performance in Coating Selection
Choosing the right coating method involves balancing cost and performance. While hot-dip galvanizing is cost-effective, thermal spraying offers superior performance for extreme conditions. Reliable suppliers like HL Steel Trading provide access to advanced coating methods, ensuring seamless project execution.
Comparison of Coating Methods
Method | Coating Thickness | Heat Resistance (°C) | Cost Efficiency |
---|---|---|---|
Hot-Dip Galvanizing | 50-150 µm | 200 | High |
Thermal Spraying | 100-500 µm | 1,000+ | Moderate |
This table highlights the key differences between hot-dip galvanizing and thermal spraying, helping professionals make informed decisions.
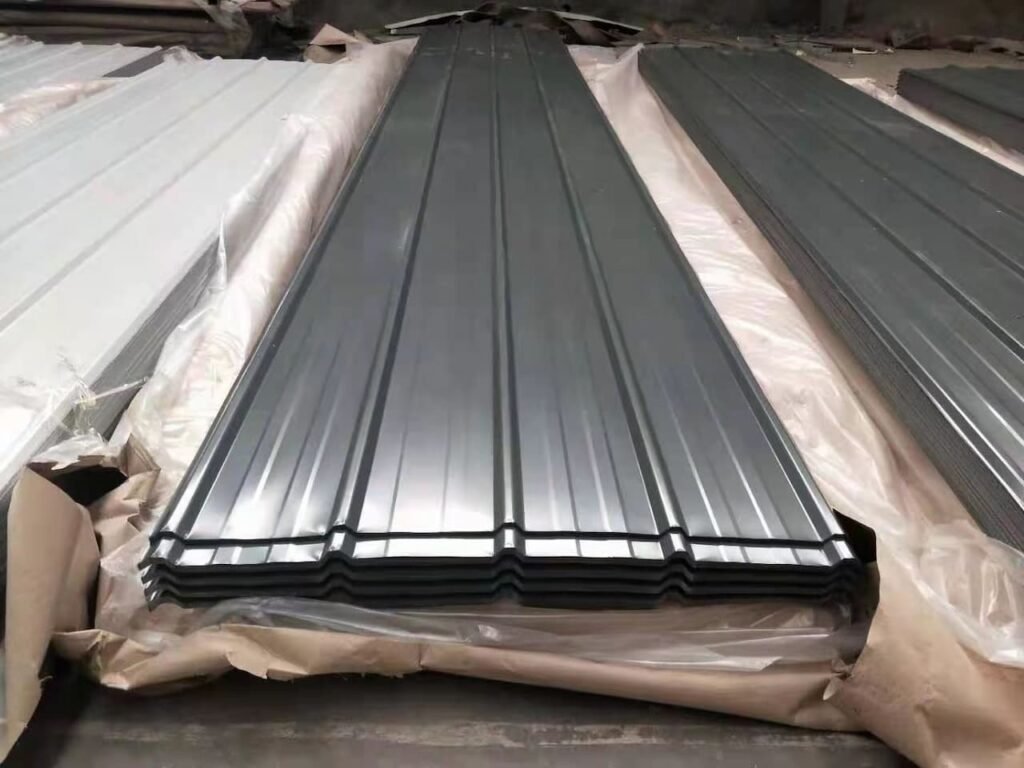
Selecting Coated Steel for Industrial Applications
Choosing the right coated steel is critical for industrial projects, especially when dealing with high heat and safety requirements. By assessing heat exposure, corrosion risks, and safety standards, professionals can make informed decisions that maximize return on investment (ROI).
“Selecting the right coated steel ensures durability, safety, and cost-efficiency in high-heat industrial applications.”
Assessing Heat Exposure and Operational Demands
The first step in selecting coated steel is evaluating the heat exposure and operational demands of your project. For example, furnaces and exhaust systems require materials that can withstand temperatures above 300°C (572°F). Coated steel with aluminized or ceramic coatings is ideal for such environments.
Evaluating Corrosion Risks and Coating Longevity
Corrosion is a major concern in industrial settings, particularly in humid or chemically aggressive environments. Coated steel with zinc or polymer-based coatings offers excellent corrosion resistance, ensuring long-term durability and reducing maintenance costs.
Meeting Safety Standards with Coated Steel
Safety is non-negotiable in industrial applications. Coated steel meets stringent safety standards by maintaining structural integrity under high stress and heat. Its reliability minimizes risks and protects both workers and equipment.
Best Practices for Maximizing Return on Investment
To maximize ROI, consider factors like coating durability, maintenance requirements, and supplier reliability. HL Steel Trading offers consulting services to help buyers match coated steel solutions to specific project needs, ensuring optimal performance and cost-efficiency.
Coated Steel Selection Guide
Application | Recommended Coating | Heat Resistance (°C) | Corrosion Resistance |
---|---|---|---|
Furnaces | Aluminized | 677 | High |
Exhaust Systems | Ceramic | 1,000+ | Very High |
Outdoor Structures | Zinc | 200 | Moderate |
Custom Solutions | Polymer-Based | 150 | High |
This table provides a clear guide for selecting the right coated steel based on application and performance requirements.
Conclusion
After a decade in the steel industry, I’ve seen firsthand how coated steel transforms challenges into opportunities in high-heat environments. It’s not just about surviving extreme temperatures—it’s about thriving with durability and safety you can count on.
For me, the real win is knowing professionals can rely on this material to keep projects strong and efficient, whether it’s a furnace or an exhaust system. Coated steel isn’t just a solution; it’s a **”ride-or-die”** partner that delivers every time.
So, if you’re tackling a high-heat project, think about what coated steel can do for you. It’s a choice that pays off in performance and peace of mind—today and down the road.
FAQ
Q1: What is coated steel used for?
A1: Coated steel is mainly used for its enhanced durability, corrosion resistance, and aesthetic appeal. It finds applications in construction, automotive, and manufacturing industries where protecting the steel from environmental factors is crucial.
Q2: How does coated steel withstand high temperatures?
A2: Coated steel designed for high-temperature environments includes special coatings that resist degradation and maintain integrity even under extreme temperature variations, ensuring structural stability and prolonged lifespan.
Q3: What are the benefits of using coated steel in industrial settings?
A3: In industrial settings, coated steel offers increased resistance to corrosion and wear, reduces maintenance costs by extending the lifespan of the steel, and can enhance safety by preventing leaks and failures in equipment.
Q4: Can coated steel rust?
A4: While the coating on the steel significantly reduces the risk of rust, improper application, or damage to the coating layer can expose the steel to elements, leading to corrosion over time.
Q5: What types of coatings are applied to steel for high-temperature use?
A5: Common coatings for high-temperature use include zinc aluminum, epoxy, and ceramic-based coatings that provide thermal stability and resistance to oxidation.
Q6: How is the performance of coated steel measured in high heat?
A6: Performance is assessed by conducting thermal tests that evaluate the integrity of the coating under cyclical high-temperature conditions, checking for signs of degradation like blistering or peeling.
Q7: Are there environmental benefits associated with using coated steel?
A7: Yes, coated steel is more sustainable as it generally requires less frequent replacement, thereby conserving resources. Additionally, certain coatings do not emit harmful emissions, making them environmentally friendly options.
Q8: How does the coating process affect the steel’s properties?
A8: The coating process involves cleaning and treating the steel surface, resulting in improved adherence, enhanced corrosion resistance, and an overall extension of the steel’s functional lifespan.
External Links
- Coated Steel – AM/NS
- Coated steel makes steel stand up to corrosion – SSAB
- Coated Steel Coil: Different Types – COSASTEEL
- Coated Steel Products & Sheet & Coil Supplier – Alliance Steel
- Coated Steel: Resistant, Useful, and Aesthetic – Ternium
- Best Protective Coatings for Steel: Protect Against Corrosion and Wear
- Painted and Coated Steel Products By Steelscape
- Metal Coatings of Steels – IspatGuru
3 Responses