Introduction
Corrosion, wear, and regulatory headaches keep industry professionals up at night. Failing to meet strict standards like ISO or ASTM can lead to penalties, safety risks, and costly delays—challenges no business can afford.
That’s where coated steel steps in. With advanced coatings designed for durability and compliance, it tackles rust, meets certification demands, and adapts to sector-specific rules. This guide breaks down how coated steel simplifies audits, boosts safety, and ensures your operations stay on the right side of regulations.
The Role of Coated Steel in Regulatory Compliance
In modern industrial settings, regulatory compliance isn’t just a legal obligation—it’s a business necessity. Companies that fail to meet material standards face serious risks including costly fines, production shutdowns, and damaged reputations. When it comes to structural integrity and safety, coated steel has emerged as a crucial solution for meeting these rigorous requirements.
From construction to automotive manufacturing, businesses increasingly turn to coated steel products to simplify compliance challenges. The right coating technology can address multiple regulatory requirements simultaneously, making it a strategic choice for companies navigating complex standards.
“Coated steel products provide a dual benefit of enhanced material performance and simplified regulatory compliance, making them essential components in industries where safety and durability standards are strictly enforced.”
Why Compliance Matters: Risks of Non-Compliance in Industry
Non-compliance with industry standards carries significant consequences. Companies face potential legal penalties, project delays, and the “bottom-line crusher” of unexpected remediation costs. Beyond financial implications, worker safety is compromised when materials fail to meet established benchmarks. A single compliance failure can trigger cascading issues affecting everything from insurance premiums to customer confidence.
Globally, regulatory agencies have tightened material requirements across construction, automotive, and manufacturing sectors. These rules aren’t arbitrary—they’re designed to prevent catastrophic failures, environmental damage, and workplace injuries. Meeting these standards isn’t optional for businesses that want to remain competitive and responsible.
What is Coated Steel? Overview of Coatings and Their Purpose
Coated steel consists of base steel that receives protective surface treatments through various application methods. These coatings create barriers against environmental factors that would otherwise compromise the steel’s integrity. Common coating types include galvanized (zinc), aluminized, polymer-based, and epoxy treatments—each offering specific protective properties.
The primary function of steel coatings is to extend product lifespan while maintaining critical performance characteristics. By preventing corrosion, these coatings ensure structural stability over time. This maintenance of integrity directly translates to ongoing compliance with safety regulations throughout the material’s service life.
How Coated Steel Addresses Corrosion and Wear Challenges
Corrosion represents one of the most significant threats to steel integrity and regulatory compliance. Unprotected steel deteriorates in many environments, potentially failing to meet load-bearing requirements or safety factors. Coated steel dramatically extends service life by creating environmental barriers that prevent oxidation and decay.
Beyond corrosion resistance, specialized coatings provide additional performance benefits that support compliance objectives. These include chemical resistance for industrial settings, temperature tolerance for extreme environments, and reduced friction for mechanical applications. Each of these properties helps maintain compliance with application-specific requirements.
Regulatory Compliance Benefits of Different Steel Coating Types
Coating Type | Primary Industries | Key Standards Met | Corrosion Resistance | Environmental Compliance |
---|---|---|---|---|
Hot-Dip Galvanized | Construction, Infrastructure | ASTM A123, ISO 1461 | 15-25 years (aggressive environment) | Low VOC, Recyclable |
Aluzinc | Roofing, HVAC | ASTM A792, EN 10346 | 20-30 years (moderate exposure) | No heavy metals, RoHS compliant |
Powder Coating | Automotive, Appliances | AAMA 2604/2605, ISO 12944 | 5-10 years (outdoor exposure) | Zero VOC, REACH compliant |
Epoxy Coating | Chemical, Oil & Gas | NACE 1/SSPC-SP 5, ISO 8501 | 10-15 years (chemical exposure) | Low leaching, FDA compliant |
Vinyl Coating | Marine, Wastewater | ASTM D1784, AWWA C203 | 15-20 years (salt exposure) | Biologically inert, NSF certified |
Introduction to Key Standards: ISO, ASTM, and Regional Regulations
Several prominent organizations establish the standards that govern coated steel usage. The International Organization for Standardization (ISO) provides global frameworks like ISO 12944 for corrosion protection systems. Meanwhile, ASTM International offers material-specific standards such as ASTM A653 for galvanized steel.
Regional regulations add another layer of compliance requirements. For example, the European Union’s Construction Products Regulation (CPR) mandates specific performance criteria for building materials. In North America, bodies like the American Iron and Steel Institute create guidelines that influence building codes and material specifications.
Suppliers like HL Steel Trading specialize in delivering coated steel products that meet these complex regulatory frameworks. By partnering with knowledgeable providers, companies can ensure their materials meet or exceed all applicable standards, reducing compliance risks while maintaining quality benchmarks.
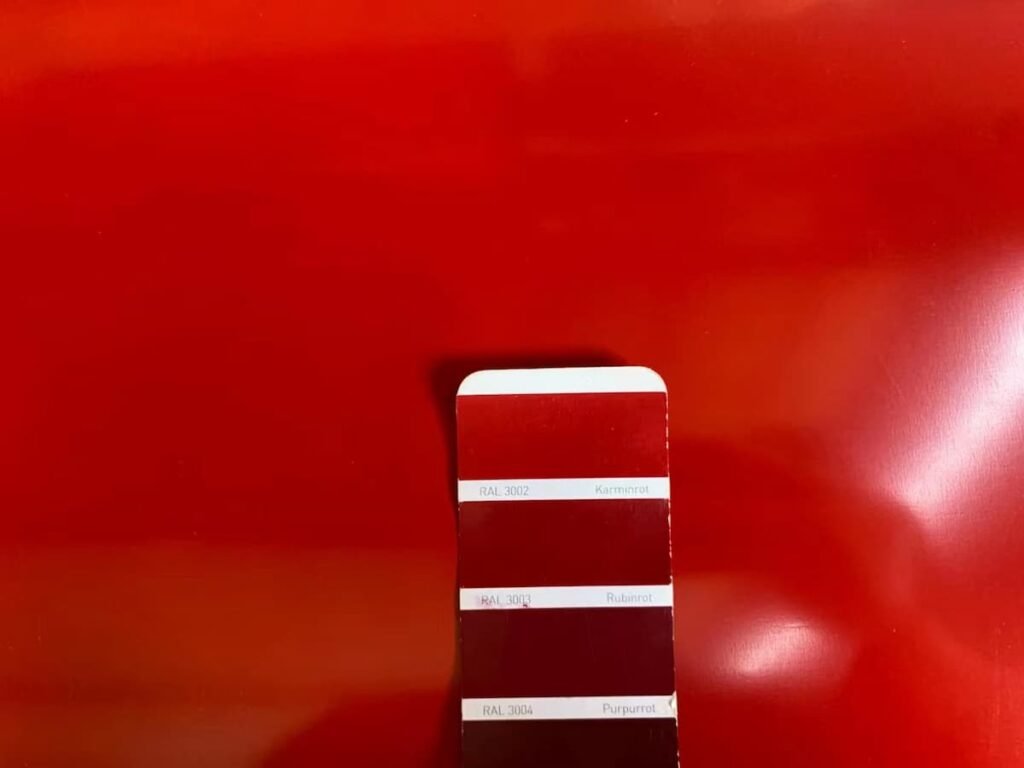
Types of Steel Coatings and Their Compliance Benefits
Steel coatings represent a critical advancement in material engineering, offering solutions that extend beyond basic protection. These specialized treatments transform standard steel into high-performance materials that meet stringent regulatory requirements across industries. Understanding the distinct properties of each coating type helps businesses select materials that ensure compliance while optimizing performance.
Selecting the right coated steel variant depends on your specific application environment and the regulatory framework governing your industry. Each coating type offers unique advantages that address particular compliance challenges, from corrosion resistance to environmental safety considerations.
“The selection of appropriate steel coating technology directly impacts a product’s regulatory compliance lifecycle, with properly specified coatings reducing certification costs and extending compliance-verified service life.”
Galvanized Steel: Zinc Coating for Corrosion Resistance
Galvanized steel, created through the application of zinc layers to base steel, represents one of the most widely adopted coating solutions. The zinc provides sacrificial protection, corroding preferentially to preserve the underlying steel. This process creates a material that maintains structural integrity in challenging environments for decades without intervention.
From a compliance perspective, galvanized steel excels in meeting construction codes and infrastructure standards. It satisfies key ASTM standards including A653/A653M for building components and G90 for severe exposure applications. The “bulletproof reliability” of properly galvanized steel makes it a preferred choice for applications where failure could create safety hazards.
Galvalume Steel: Aluminum-Zinc Blend for Durability
Galvalume coatings combine aluminum (55%) and zinc (45%) to create a protective layer with enhanced performance characteristics. This hybrid approach delivers superior heat resistance and approximately twice the lifespan of standard galvanized steel in many applications. The aluminum component provides barrier protection while zinc offers sacrificial protection at cut edges.
Regulatory standards like ASTM A792/A792M specifically address Galvalume steel, establishing performance benchmarks for building materials. This coating technology meets stringent fire resistance ratings and maintains compliance with environmental regulations by eliminating the need for frequent replacement and associated waste generation.
Pre-Painted Steel: Aesthetic and Protective Layers
Pre-painted steel (often referred to as color-coated steel) combines protective zinc layers with polymer paint systems. These multi-layer solutions offer both aesthetic flexibility and enhanced performance characteristics. The paint systems typically include primers optimized for adhesion and topcoats engineered for UV resistance and color stability.
This coating category must satisfy both protective standards and environmental regulations governing chemical composition. Modern systems comply with REACH and RoHS directives by eliminating restricted substances. Additionally, pre-painted steel often meets AAMA 621 performance standards for architectural applications.
Comparative Analysis of Steel Coating Technologies for Regulatory Compliance
Coating Type | Primary Compliance Standards | Corrosion Resistance (Salt Spray Hours) | Environmental Compliance Features | Service Life Expectancy |
---|---|---|---|---|
Hot-Dip Galvanized | ASTM A123, ISO 1461, EN 10346 | 750-1000 | 100% Recyclable, Zero VOCs | 30-50 years (moderate environment) |
Galvalume (Aluzinc) | ASTM A792, EN 10346, JIS G3321 | 1500-2000 | Enhanced Thermal Efficiency, Reduced Material Usage | 40-60 years (moderate environment) |
Pre-Painted Galvanized | ASTM A755, AAMA 621, EN 10169 | 1000-1200 | Low/Zero VOC Options, REACH Compliant | 20-30 years (exterior exposure) |
Electrogalvanized | ASTM A879, ISO 2081, EN 10152 | 96-240 | Precision Application, Minimal Zinc Usage | 10-15 years (interior applications) |
Zinc-Aluminum-Magnesium | EN 10346, JIS G3323, ASTM A1046 | 2000-3000 | Reduced Coating Thickness, Resource Conservation | 50-70 years (moderate environment) |
Coating Customization for Industry-Specific Standards
Beyond standard offerings, specialized coating formulations address industry-specific compliance requirements. For example, food-grade applications require coatings that meet FDA 21 CFR 175.300 for food contact. Medical environments might demand antimicrobial coating properties certified under ISO 22196.
Customized coating solutions from suppliers like HnLsteel enable businesses to address complex regulatory frameworks efficiently. These tailored approaches can integrate multiple compliance features into a single coating system, simplifying certification processes while enhancing material performance. This strategic alignment between material properties and regulatory standards creates value throughout the supply chain.
Coated Steel Applications Across Industries
Coated steel has become an essential material across multiple sectors due to its exceptional performance characteristics and ability to meet stringent regulatory requirements. From skyscrapers to automobiles, this versatile material provides the crucial combination of strength, durability, and corrosion resistance that modern industries demand for compliance-critical applications.
Industry leaders increasingly recognize that selecting the right coated steel isn’t just about material performance—it’s about navigating complex regulatory landscapes efficiently. Different coating technologies address specific compliance challenges that vary significantly between application environments.
“Coated steel products enable industries to meet stringent safety and environmental regulations while maintaining structural integrity and durability, making them fundamental components in compliance-driven engineering and construction projects.”
Construction: Structural Integrity and Safety Standards
The construction industry relies heavily on coated steel to meet building codes and safety regulations. These standards, including ASTM A653 and Eurocode 3, establish minimum requirements for structural elements exposed to various environmental conditions. Galvanized and Aluzinc coated steel components satisfy these requirements while maintaining long-term structural integrity.
Fire safety regulations present another critical compliance area. Many coated steel products receive fire resistance ratings that satisfy code requirements without additional treatments. This “code-friendly” characteristic simplifies the approval process for architects and builders while ensuring occupant safety throughout a structure’s lifespan.
Automotive: Corrosion Protection for Longevity
Automotive manufacturers face dual compliance challenges: meeting corrosion resistance standards while satisfying environmental regulations. Modern vehicles utilize zinc-nickel and galvannealed steel coatings that provide the required 12-year perforation resistance without compromising recyclability or introducing restricted substances.
Safety-critical components demand specialized coatings that maintain structural integrity during collisions. These components must comply with FMVSS and EU safety directives throughout the vehicle’s service life. Advanced coating technologies ensure these parts maintain their protective capabilities despite exposure to road salt, chemicals, and environmental stressors.
Energy Sector: Durability in Harsh Environments
Energy infrastructure operates in uniquely challenging conditions that require specialized coated steel solutions. Solar mounting systems use galvanized or aluminum-zinc coated steel that meets UL 2703 requirements for outdoor durability and grounding capabilities. These materials maintain their protective and conductive properties despite decades of UV exposure.
Oil and gas applications require compliance with NACE standards for material performance in highly corrosive environments. Specialized coatings with advanced chemical resistance protect critical infrastructure while satisfying stringent safety regulations that govern this high-risk industry.
Regulatory Compliance Matrix for Coated Steel Applications
Industry | Primary Coating Types | Key Regulatory Standards | Compliance Benefits | Testing Requirements |
---|---|---|---|---|
Construction | Hot-Dip Galvanized, Aluzinc | ASTM A653, Eurocode 3, ICC-500 | Structural integrity, Fire resistance, Weather resilience | Salt spray (ASTM B117), Bend testing, Coating thickness |
Automotive | Galvannealed, Zinc-Nickel | SAE J2334, FMVSS, EU Directive 2000/53/EC | Corrosion resistance, Recyclability, Collision performance | Cyclic corrosion, Stone chip resistance, Weldability |
Energy | Fusion-bonded Epoxy, Metallized | NACE SP0169, API 5L, UL 2703 | Chemical resistance, Temperature tolerance, Grounding capability | Cathodic disbondment, Impact resistance, Electrical continuity |
Food Processing | Stainless Steel, FDA-Approved Coatings | FDA 21 CFR 175.300, NSF/ANSI 51, ISO 22000 | Sanitation compliance, Chemical resistance, Non-toxicity | Food contact safety, Cleanability, Corrosion resistance |
Marine | Zinc-Rich, Multi-layer Polymeric | ISO 12944-9, ASTM D6991, IMO PSPC | Saltwater resistance, Biofouling prevention, UV stability | Accelerated weathering, Adhesion testing, Immersion testing |
Case Studies: Real-World Compliance Success Stories
A major bridge rehabilitation project demonstrates the compliance benefits of advanced coated steel. Engineers selected duplex coating systems (zinc plus paint) that satisfied both structural requirements and environmental regulations prohibiting lead and chromates. This solution extended maintenance intervals while ensuring full regulatory compliance for a critical infrastructure asset.
In commercial building applications, manufacturers like HL Steel Trading provide customized coating solutions that address multiple compliance requirements simultaneously. These tailored systems help construction companies navigate complex building codes while maintaining project timelines and budgetary constraints.
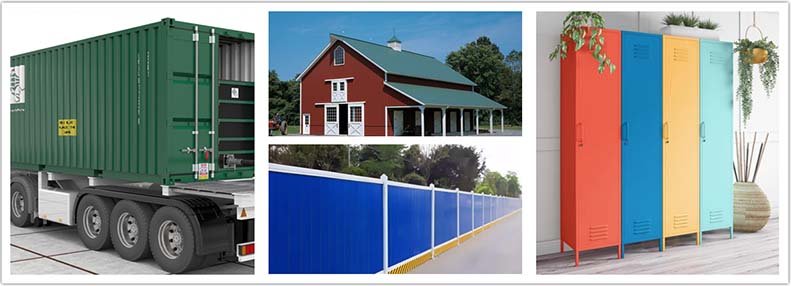
Certification and Auditing Processes for Coated Steel
Understanding the certification and auditing landscape for coated steel products is essential for businesses seeking regulatory compliance. These verification processes ensure materials meet quality benchmarks while providing documentation that simplifies regulatory reviews. When properly navigated, these systems protect both manufacturers and end-users by confirming material performance characteristics.
The certification journey begins with raw material validation and continues through production, testing, and final inspection. Each step follows established protocols designed to verify specific quality attributes that impact compliance status. Companies that understand these processes gain advantages in procurement, risk management, and regulatory documentation.
“Effective certification and auditing of coated steel products provides a documented compliance pathway that reduces regulatory uncertainty while validating material performance across critical safety and quality parameters.”
Supplier Audits: Ensuring Coating Quality and Consistency
Supplier qualification stands as the first critical checkpoint in the coated steel compliance process. Manufacturing facilities undergo comprehensive audits examining process controls, quality management systems, and production consistency. These evaluations often include unannounced inspections that verify day-to-day operations maintain certification standards.
Third-party auditors typically examine coating thickness variations, adhesion consistency, and surface finish quality. These assessments create a “trust but verify” relationship between suppliers and buyers that strengthens the entire supply chain. Regular audit schedules, typically conducted annually or semi-annually, ensure ongoing compliance rather than point-in-time certification.
Material Testing: Methods for Compliance Verification
Laboratory testing provides quantitative validation of coated steel performance characteristics. These tests follow standardized methods from organizations like ASTM International and ISO that ensure consistent, reproducible results. Common procedures include salt spray testing (ASTM B117), coating thickness measurement (ASTM B499), and bend testing for coating adhesion.
Beyond standard tests, application-specific evaluations address specialized requirements. For instance, food-grade applications require leaching tests that confirm coating stability when in contact with acidic substances. Similarly, building materials undergo fire resistance testing that verifies performance during extreme temperature exposure.
Certification Testing Requirements for Coated Steel Products
Test Method | Applicable Standard | Industry Application | Compliance Parameter | Testing Frequency |
---|---|---|---|---|
Salt Spray Resistance | ASTM B117, ISO 9227 | Automotive, Construction | 240-1000 hours (varies by coating) | Per batch/quarterly |
Coating Thickness | ASTM B499, ISO 2178 | All Industries | ±10% of specification | Continuous monitoring |
Adhesion Testing | ASTM D3359, ISO 2409 | Construction, Appliance | Grade 4B or better | Daily production sampling |
Impact Resistance | ASTM D2794, ISO 6272 | Automotive, Industrial | No cracking at specified height | Weekly validation |
Chemical Resistance | ASTM D1308, ISO 2812 | Chemical, Food Processing | No visible degradation after exposure | Per formulation change |
Certification Standards: ISO, ASTM, and Beyond
Multiple certification frameworks govern coated steel quality, creating a complex landscape for manufacturers and buyers. ISO 9001 certification provides baseline verification of quality management systems, while product-specific standards like ISO 12944 address corrosion protection performance. These frameworks establish minimum performance criteria that certified products must consistently achieve.
Regional standards add another layer of certification requirements. The European CE marking, American ASTM compliance, and Japanese JIS certifications each emphasize different performance aspects. Navigating these overlapping frameworks requires detailed understanding of test methods and documentation requirements for each target market.
Documentation: Streamlining Regulatory Reviews
Comprehensive documentation packages simplify regulatory compliance verification. Test reports, material certifications, and process validation records provide the evidence trail needed during audits and inspections. Leading suppliers like HnLsteel maintain digital documentation systems that give clients immediate access to compliance information when regulatory questions arise.
For multi-tier supply chains, documenting material provenance has gained importance in regulatory compliance. Traceability documentation from raw materials through coating processes verifies that each production step meets required specifications. This documentation chain supports both quality assurance and regulatory confidence throughout the material lifecycle.
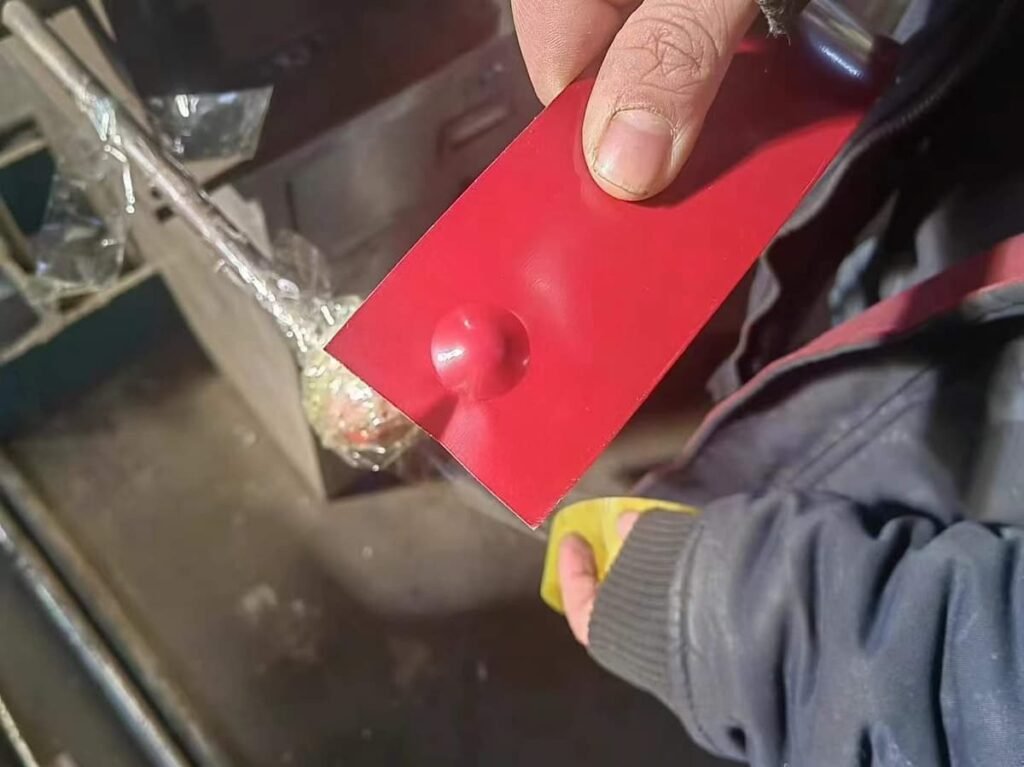
Choosing Coated Steel for Compliance and Cost Efficiency
Selecting the right coated steel solution requires balancing multiple factors including regulatory requirements, performance needs, and budget constraints. Making informed decisions at this stage can prevent costly compliance issues while optimizing operational expenditure throughout a project’s lifecycle.
Industry professionals face increasing pressure to meet stringent standards while controlling costs. The right coated steel specification addresses both concerns by providing long-term protection that reduces maintenance requirements and extends service life, effectively spreading initial investment across a longer operational timeline.
“Strategic selection of coated steel products allows organizations to meet regulatory requirements while optimizing total cost of ownership, with properly specified materials reducing maintenance expenses by up to 30% over project lifetimes.”
Factors to Consider: Environment, Standards, and Budget
Environmental exposure represents the primary consideration when selecting coated steel products. Materials facing coastal conditions require different protection systems than those in urban or industrial settings. Properly matching coating technology to environmental stressors ensures compliance with durability standards while preventing premature failure and associated replacement costs.
Regulatory standards vary significantly between industries and regions, creating complex specification requirements. Construction applications must typically meet building codes like IBC and ASTM A653, while food processing equipment requires FDA-compliant coatings. Understanding these requirements early in the selection process prevents “budget-busting” rework or certification delays.
Benefits of Proactive Protection: Long-Term Cost Savings
The initial premium for high-performance coated steel typically represents only 10-15% of total material costs, yet delivers disproportionate value through extended service life. This investment perspective transforms the selection process from simple price comparison to sophisticated lifecycle cost analysis. Organizations adopting this approach consistently report positive ROI despite higher upfront expenses.
Maintenance reduction represents another significant economic benefit of quality coated steel. Systems with superior corrosion protection eliminate costly maintenance cycles that impact operational continuity. This preventative approach aligns with modern asset management principles that prioritize reliability over reactive maintenance.
Cost-Benefit Analysis of Coating Technologies Over 20-Year Lifecycle
Coating Type | Initial Cost Premium | Expected Service Life | Maintenance Cycles | Lifetime Cost Savings |
---|---|---|---|---|
Standard Galvanized | Base Cost | 12-15 years | 2-3 major interventions | Reference Point (0%) |
Heavy Galvanized | +15% | 18-22 years | 1 major intervention | 22% savings vs standard |
Galvalume/Aluzinc | +25% | 25-30 years | 0-1 major interventions | 35% savings vs standard |
Duplex Systems (Galvanized + Paint) | +40% | 30+ years | Minor touch-ups only | 42% savings vs standard |
Premium Polymer Coatings | +50% | 35+ years | None typically required | 48% savings vs standard |
Partnering with Suppliers: Ensuring Compliance and Quality
Experienced suppliers like HnLsteel provide value beyond basic material provision by offering compliance documentation, material testing, and specification guidance. These partnerships simplify the regulatory process by ensuring materials arrive with complete certification packages that satisfy audit requirements without additional testing or documentation efforts.
Supply chain transparency has emerged as a critical factor in regulatory compliance. Working with established suppliers provides traceability from mill to installation, creating documented evidence of material quality and specification adherence. This documentation trail proves invaluable during regulatory reviews and quality assurance audits.
Future Trends: Innovations in Coating Technology
Emerging coating technologies continue to improve the compliance and cost equation for steel products. Advanced zinc-aluminum-magnesium coatings offer enhanced corrosion protection with thinner application requirements, reducing material usage while extending service life. These innovations represent the next generation of solutions for meeting stricter environmental and performance standards.
Sustainability considerations increasingly influence both regulatory requirements and coating development. Modern coated steel meets how coated steel meets safety standards while addressing environmental concerns through reduced material usage, elimination of restricted substances, and enhanced recyclability.
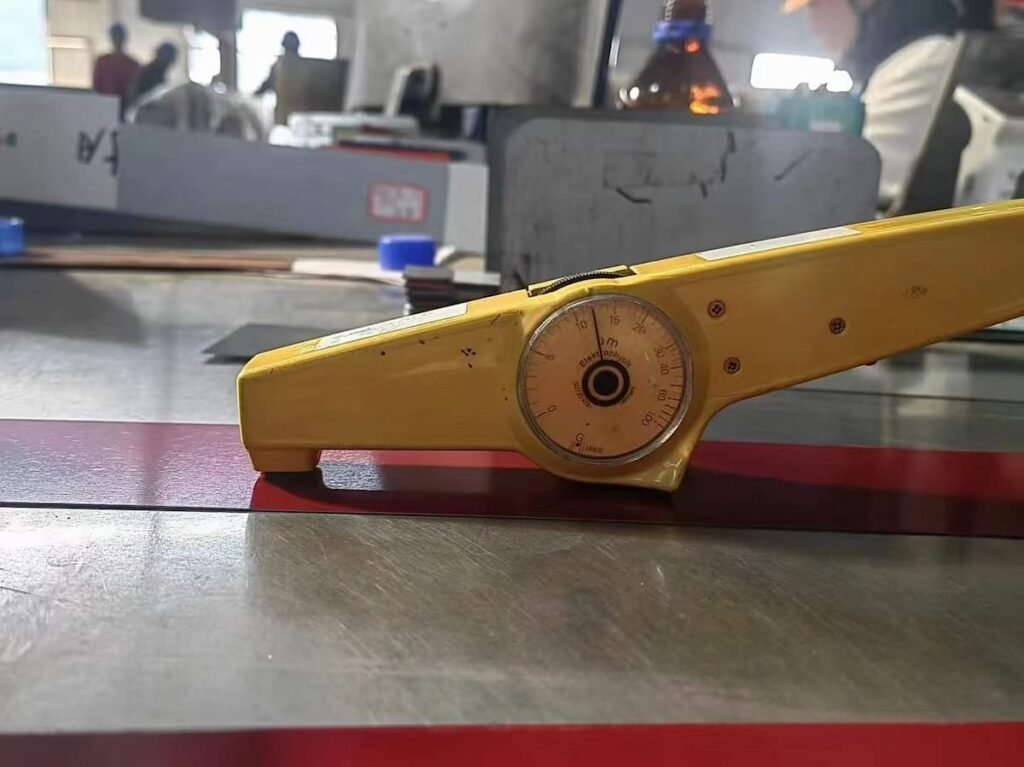
Conclusion
After a decade in the steel game, I’ve seen how coated steel turns regulatory headaches into a walk in the park. It’s not just about dodging rust—it’s about keeping your projects safe, compliant, and built to last, no matter the industry.
I can tell you from experience: picking the right coating isn’t optional—it’s the backbone of meeting standards like ISO or ASTM without breaking a sweat. It’s a **”no-brainer”** for anyone serious about quality and avoiding costly rework.
So, as you weigh your options, think about this: the right coated steel doesn’t just check boxes today—it sets you up for smoother audits and bigger wins down the road. What’s your next move?
FAQ
Q1: What are the benefits of using coated steel?
A1: Coated steel offers enhanced durability, corrosion resistance, and aesthetic appeal. It is widely used in various applications due to these benefits.
Q2: How does coated steel resist corrosion?
A2: Coated steel resists corrosion primarily through the application of metallic coatings like zinc or aluminum, which act as a protective barrier against environmental factors.
Q3: What types of coatings are used on steel?
A3: Common coatings include zinc (galvanization), aluminum, and polymers. These coatings provide different levels of protection and are selected based on the intended application.
Q4: Is coated steel compliant with ISO standards?
A4: Yes, coated steel can be manufactured to comply with ISO standards, ensuring high quality and adherence to international requirements.
Q5: Why is coated steel preferred in construction?
A5: Coated steel is preferred in construction due to its high resistance to environmental degradation, which enhances the longevity of structures.
Q6: What are the applications of coated steel?
A6: Coated steel is used in roofing, structural components, automotive parts, appliances, and more due to its durability and resistance to wear.
Q7: How does coated steel contribute to sustainability?
A7: Coated steel contributes to sustainability by extending the life of steel products, reducing the need for replacements, and minimizing waste.
Q8: Can coated steel be recycled?
A8: Yes, coated steel can be recycled. The coatings do not affect the recyclability of the underlying steel material.
External Links
- Coated Steel: Resistant, Useful, and Aesthetic
- Coated Products – Mill Steel
- Coated steel – Stavian Industrial Metal
- Coated Steel Products & Sheet & Coil Supplier – Alliance Steel
- Coated Steel – Randall Metals Corporation
- Coated steel makes steel stand up to corrosion – SSAB
- Zam ® Corrosion Resistant Steel – Wheeling-nippon Steel
- The Different Types of Coated Steel Tubes and Their Uses
4 Responses