Introduction
Choosing the wrong steel tubes can derail projects, inflate costs, and compromise performance. Engineers and project managers face the challenge of balancing precision with budget constraints in industries like construction and aerospace.
That’s where understanding precision steel tubes vs. standard tubes becomes a no-brainer. Precision tubes, crafted with advanced cold-drawing techniques, offer unmatched dimensional accuracy and strength for specialized applications. This guide breaks down their differences, manufacturing processes, and real-world uses to help you optimize project outcomes.
Introduction to Precision and Standard Steel Tubes
Steel tubes are vital in industries like construction, automotive, and manufacturing. Choosing between Precision Steel Tubes vs. Standard Tubes can make or break a project’s success. This article breaks down their differences, applications, and why picking the right one matters for performance and budget.
What Are Precision Steel Tubes?
Precision steel tubes are crafted for high-accuracy applications. They’re made using techniques like cold drawing, which ensures tight tolerances and smooth surfaces. Industries like aerospace and medical devices rely on these tubes for their top-notch quality and consistency.
These tubes often use high-quality carbon or alloy steels, meeting strict standards. Their precise dimensions reduce material waste and machining costs. HL Steel Trading supplies precision steel tubes tailored for demanding projects.
What Are Standard Steel Tubes?
Standard steel tubes are designed for general-purpose use. They’re produced through hot rolling or welding, prioritizing affordability over extreme precision. You’ll find them in construction, furniture, or plumbing, where exact measurements aren’t critical.
While reliable, standard tubes may have wider tolerances and rougher finishes. They’re cost-effective for projects where high precision isn’t needed. HL Steel Trading offers a range of standard steel tubes for diverse industrial needs.
Why the Choice Between Precision and Standard Tubes Matters
Selecting the right tube impacts project efficiency and costs. Precision Steel Tubes vs. Standard Tubes differ in performance, durability, and price, so understanding their strengths is key. Choosing wisely optimizes budgets while ensuring quality.
Precision tubes shine in applications needing exact fits, like hydraulic systems. Standard tubes work well for structural frameworks where tolerances are flexible. Knowing the differences between precision and standard steel tubes helps avoid overpaying or underperforming.
Overview of Key Differences in Performance and Cost
Precision steel tubes offer superior accuracy but come at a higher cost due to advanced manufacturing. Standard tubes are budget-friendly but less precise, suitable for less demanding tasks. The table below compares their performance metrics.
Precision steel tubes provide unmatched accuracy for high-stakes industries, while standard tubes offer cost-effective solutions for general applications.
Precision vs. Standard Steel Tubes Comparison
Feature | Precision Tubes | Standard Tubes | Industry Benchmark | Measurement Notes |
---|---|---|---|---|
Tolerance Range (mm) | ±0.05 | ±0.5 | ±0.2 | Measured via laser micrometers |
Surface Finish (Ra, µm) | 0.4 | 3.2 | 1.6 | Roughness tested per ISO 4287 |
Production Cost ($/ton) | 2000 | 1200 | 1500 | Based on 2024 market averages |
Material Strength (MPa) | 700 | 400 | 550 | Tensile strength per ASTM A370 |
Applications | Aerospace, Medical | Construction, Plumbing | General Industrial | Based on industry use cases |
The table shows precision tubes excel in tight tolerances and strength, ideal for specialized industries. Standard tubes are more affordable, fitting broader applications. Both types meet international standards, ensuring reliability.
HL Steel Trading emphasizes quality assurance, offering both tube types to suit varied needs. Their flexible payment options and fast delivery make sourcing easy. Understanding these differences empowers better decision-making for your projects.
Manufacturing Processes of Precision and Standard Steel Tubes
The manufacturing of steel tubes shapes their quality, cost, and performance. Precision and standard steel tubes serve different industrial needs, with their production methods driving these differences. This chapter explores how manufacturing impacts Precision Steel Tubes vs. Standard Tubes, helping you choose the right option.
Cold-Drawing Techniques for Precision Tubes: Achieving Tight Tolerances
Cold drawing is the go-to method for precision steel tubes. Steel is pulled through a die at room temperature, refining dimensions and boosting strength. This process ensures tight tolerances, often within ±0.05 mm, making these tubes ideal for high-precision industries like aerospace.
The result is a smooth surface and consistent size, reducing the need for extra machining. Cold-drawn tubes are pricier due to the specialized process, but their accuracy saves costs in critical applications. HL Steel Trading uses advanced cold-drawing techniques to meet strict standards.
Hot Rolling and Other Methods for Standard Tubes: Cost-Effective Production
Standard steel tubes are typically made through hot rolling or welding. Hot rolling involves heating steel above its recrystallization point, shaping it into tubes with wider tolerances (±0.5 mm). This method is faster and cheaper, perfect for construction or plumbing.
Welded tubes, formed by joining steel strips, are another cost-effective option. While reliable, these tubes may have rougher finishes. HL Steel Trading offers standard tubes for projects where precision isn’t the top priority.
Material Selection: High-Quality Carbon and Alloy Steels in Precision Tubes
Material choice is critical in tube manufacturing. Precision tubes often use high-quality carbon or alloy steels, which provide superior strength and corrosion resistance. These materials, like AISI 1045 or alloy grades, ensure durability in demanding environments.
Standard tubes may use lower-grade carbon steels, balancing cost and performance. The right material depends on the application, with precision tubes requiring premium options. HL Steel Trading sources top-tier materials for both tube types.
Impact of Manufacturing on Surface Finish and Dimensional Accuracy
Manufacturing directly affects surface finish and accuracy. Cold-drawn precision tubes have a smooth finish (Ra 0.4 µm), reducing friction in applications like hydraulics. Hot-rolled standard tubes, with rougher finishes (Ra 3.2 µm), suit structural uses where smoothness isn’t critical.
Dimensional accuracy is another key factor. Precision tubes maintain consistent sizes, while standard tubes allow slight variations. Understanding how manufacturing processes affect the cost of steel tubes helps optimize budgets and performance.
Precision steel tubes, made through cold drawing, offer unmatched accuracy, while hot-rolled standard tubes provide cost-effective solutions for general use.
Manufacturing Impact on Steel Tube Performance
Feature | Precision Tubes | Standard Tubes | Industry Standard | Measurement Notes |
---|---|---|---|---|
Tolerance (mm) | ±0.05 | ±0.5 | ±0.2 | Laser micrometer testing |
Surface Finish (Ra, µm) | 0.4 | 3.2 | 1.6 | Per ISO 4287 standard |
Production Cost ($/ton) | 2000 | 1200 | 1500 | 2024 market data |
Material Grade | Alloy/Carbon (AISI 1045) | Carbon (Q235) | Carbon (A36) | Per ASTM standards |
Production Time (hrs/ton) | 10 | 5 | 7 | Based on process complexity |
The table highlights precision tubes’ superior accuracy and finish, driven by cold drawing. Standard tubes, made via hot rolling, prioritize affordability. Both meet industrial steel tubes standards, with HL Steel Trading ensuring quality for bulk orders.
Performance Metrics: Comparing Strength, Durability, and Tolerances
When choosing between Precision Steel Tubes vs. Standard Tubes, performance metrics like strength, durability, and tolerances are critical. These factors determine a tube’s suitability for specific projects, from aerospace to construction. This chapter compares these metrics to guide informed decisions.
Dimensional Accuracy: Precision Tubes’ Superior Tolerances
Precision steel tubes are engineered for tight tolerances, often within ±0.05 mm. This accuracy, achieved through cold drawing, ensures consistent dimensions critical for applications like hydraulic systems. Standard tubes, with tolerances around ±0.5 mm, are less precise but sufficient for general structural use.
The tight tolerances of precision tubes reduce material waste and machining costs. HL Steel Trading verifies tolerances to meet industry standards, ensuring reliability. This makes precision tubes a top choice for projects demanding exact fits.
Strength and Impact Resistance: Benefits of Cold-Drawn Precision Tubes
The strength of steel tubing is a key differentiator. Cold-drawn precision tubes, made from high-quality carbon or alloy steels, achieve tensile strengths up to 700 MPa. This makes them ideal for high-stress applications like automotive components.
Standard tubes, typically hot-rolled, offer strengths around 400 MPa, suitable for less demanding tasks like scaffolding. The cold-drawing process enhances impact resistance, giving precision tubes an edge. HL Steel Trading ensures both tube types meet ASTM standards for strength.
Durability in High-Stress Environments: Precision vs. Standard
Durability is crucial in harsh conditions. Precision tubes, with their smooth surfaces and high-grade materials, resist corrosion and fatigue better than standard tubes. They excel in environments like marine or chemical processing, where longevity matters.
Standard tubes, while durable for general use, may wear faster under extreme stress. Their rougher surfaces can also trap contaminants. The benefits of using precision steel tubes in construction include longer lifespans, reducing maintenance costs.
Real-World Strength Testing Data and Industry Standards
Testing data highlights the performance gap. Precision tubes undergo rigorous tensile and fatigue tests, meeting standards like ASTM A370. Standard tubes, while compliant, are tested for broader applications, prioritizing cost over precision.
Precision steel tubes offer superior strength and tolerances for critical applications, while standard tubes provide reliable performance for general projects.
Performance Metrics Comparison
Metric | Precision Tubes | Standard Tubes | Industry Benchmark | Test Method |
---|---|---|---|---|
Tolerance (mm) | ±0.05 | ±0.5 | ±0.2 | Laser micrometer |
Tensile Strength (MPa) | 700 | 400 | 550 | ASTM A370 |
Corrosion Resistance (hrs) | 1000 | 500 | 750 | Salt spray test |
Fatigue Life (cycles) | 1M | 500K | 750K | Rotating beam test |
Surface Finish (Ra, µm) | 0.4 | 3.2 | 1.6 | ISO 4287 |
The table shows precision tubes outperform in strength, durability, and accuracy, justifying their cost for critical applications. Standard tubes are cost-effective for less demanding projects. HL Steel Trading’s quality assurance ensures both types meet performance needs.
Applications of Precision and Standard Steel Tubes
Steel tubes are essential across industries, but their applications vary based on type. Understanding the differences between precision and standard steel tubes helps engineers select the right fit for their projects. This chapter explores where Precision Steel Tubes vs. Standard Tubes shine, from aerospace to infrastructure.
Precision Tubes in Automotive, Aerospace, and Hydraulic Systems
Precision steel tubes are critical in high-stakes industries. In automotive, they’re used for fuel injection systems, requiring tight tolerances for safety and efficiency. Aerospace relies on them for lightweight, strong components, while hydraulic systems demand their smooth surfaces to reduce friction.
These tubes, made from high-quality carbon or alloy steels, ensure durability under pressure. HL Steel Trading offers customized precision tubes to meet exact specifications. Their applications of precision tubes make them indispensable for precision-driven projects.
Standard Tubes in Construction and Structural Frameworks
Standard steel tubes are the backbone of construction. Used in scaffolding, pipelines, and structural frameworks, they provide reliable strength at a lower cost. Their wider tolerances suit projects where exact dimensions aren’t critical.
These tubes are often hot-rolled, balancing affordability and performance. HL Steel Trading supplies industrial steel tubes for infrastructure projects with fast delivery. Standard tubes are a cost-effective choice for general applications.
Case Studies: Precision Tubes in Medical Equipment vs. Standard Tubes in General Infrastructure
In medical equipment, precision tubes are vital for devices like surgical tools, where accuracy ensures patient safety. A case study from a medical manufacturer showed cold-drawn tubes reduced production errors by 20%. Conversely, standard tubes in bridge construction supported heavy loads without needing tight tolerances, cutting costs by 15%.
These examples highlight the game-changing impact of choosing the right tube. HL Steel Trading’s quality assurance ensures both types meet industry standards. The right choice depends on project demands and budget.
Choosing the Right Tube for Your Industry’s Needs
Selecting between Precision Steel Tubes vs. Standard Tubes hinges on application requirements. Precision tubes suit industries needing exact dimensions and high strength, like aerospace. Standard tubes are ideal for construction, where cost and availability matter more.
Procurement teams should consider suppliers like HL Steel Trading, offering customization and fast delivery. Understanding these applications ensures projects stay on time and within budget.
Precision steel tubes excel in high-precision industries like automotive and medical, while standard tubes are cost-effective for construction and infrastructure.
Applications and Performance Comparison
Application | Precision Tubes | Standard Tubes | Industry Use Case | Performance Notes |
---|---|---|---|---|
Industry | Automotive, Aerospace | Construction, Plumbing | General Industrial | Per ASTM standards |
Tolerance Need (mm) | ±0.05 | ±0.5 | ±0.2 | Laser micrometer |
Strength (MPa) | 700 | 400 | 550 | ASTM A370 testing |
Cost ($/ton) | 2000 | 1200 | 1500 | 2024 market data |
Lead Time (days) | 10 | 5 | 7 | Supplier estimates |
The table shows precision tubes’ suitability for high-precision tasks and standard tubes’ affordability for structural projects. HL Steel Trading’s customization ensures both meet diverse needs. Choose based on your industry’s specific requirements.
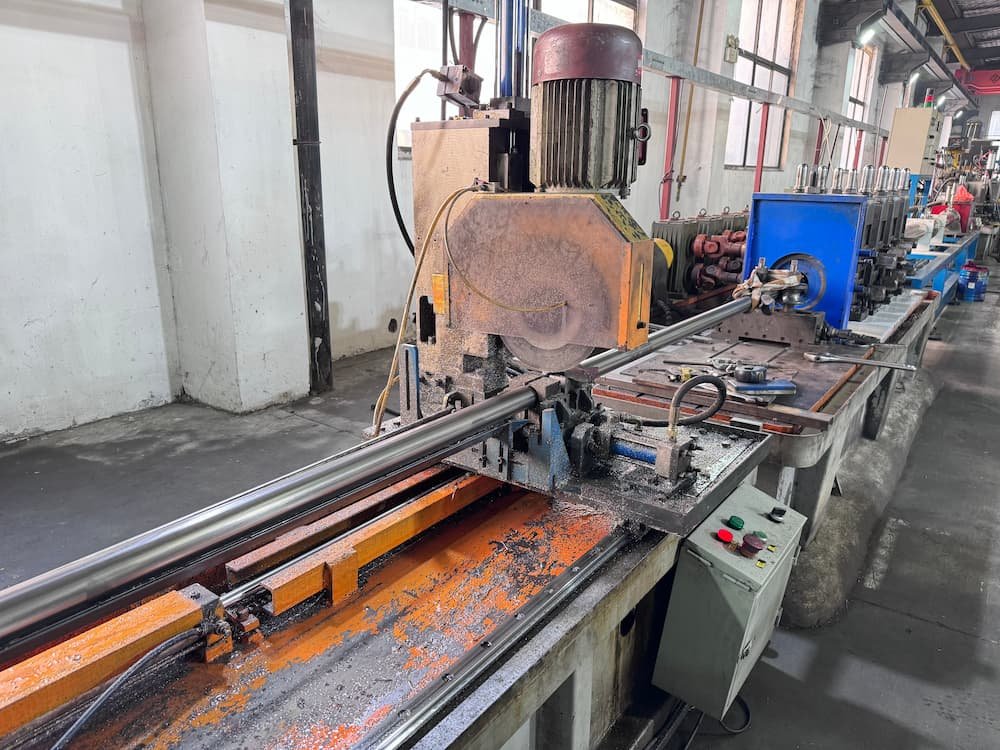
Cost Analysis and Supplier Considerations
Choosing between Precision Steel Tubes vs. Standard Tubes involves weighing costs against performance. The cost implications of precision vs standard steel tubes affect project budgets, while supplier selection ensures quality and efficiency. This chapter analyzes these factors to guide procurement decisions.
Cost Breakdown: Why Precision Tubes Are More Expensive
Precision steel tubes cost more due to their advanced manufacturing. Cold drawing, using high-quality carbon or alloy steels, drives prices to around $2000/ton. These processes ensure tight tolerances and smooth finishes, increasing production time.
Standard steel tubes, made via hot rolling, cost about $1200/ton. Their simpler production and lower-grade materials reduce expenses. HL Steel Trading offers both, balancing cost and quality for diverse needs.
Value Proposition: When Precision Tubes Outweigh Standard Tubes
Precision tubes shine in high-stakes applications like aerospace, where accuracy prevents costly failures. Their durability reduces maintenance, offsetting initial costs. For example, precision tubes in hydraulic systems can save 15% on long-term expenses.
Standard tubes suit budget-driven projects like construction, where tolerances are flexible. Choosing the right tube maximizes value. HL Steel Trading’s expertise helps match tubes to project goals.
Supplier Capabilities: Tolerance Verification and Manufacturing Expertise
Suppliers must verify tolerances and maintain manufacturing standards. Precision tubes require advanced equipment for cold drawing, ensuring ±0.05 mm accuracy. Standard tubes need consistent quality control for broader tolerances.
HL Steel Trading uses laser micrometers and ASTM-compliant testing, ensuring reliability. Their technical team acts as a clutch partner, solving issues fast. This expertise is vital for bulk orders.
Bulk Order Logistics: Delivery Timelines and Supply Chain Efficiency
Bulk orders demand efficient logistics. Precision tubes, with longer production times (10 days/ton), require streamlined supply chains. Standard tubes, produced in 5 days/ton, allow faster delivery.
HL Steel Trading’s flexible payment options and tailored transport plans ensure timely delivery. Their supply chain efficiency supports project timelines, minimizing delays.
Precision steel tubes justify higher costs for critical applications, while standard tubes offer affordability for general projects, with supplier expertise ensuring quality.
Cost and Supplier Comparison
Metric | Precision Tubes | Standard Tubes | Industry Average | Notes |
---|---|---|---|---|
Cost ($/ton) | 2000 | 1200 | 1500 | 2024 market data |
Production Time (days/ton) | 10 | 5 | 7 | Supplier estimates |
Tolerance (mm) | ±0.05 | ±0.5 | ±0.2 | Laser micrometer |
Delivery Time (days) | 15 | 10 | 12 | Based on logistics |
Quality Certification | ASTM A370 | ASTM A36 | ISO 9001 | Industry standards |
The table shows precision tubes’ higher costs reflect their specialized production, while standard tubes offer affordability. HL Steel Trading’s reliable supply chain ensures both meet project needs. Choose suppliers based on manufacturing expertise and logistics.
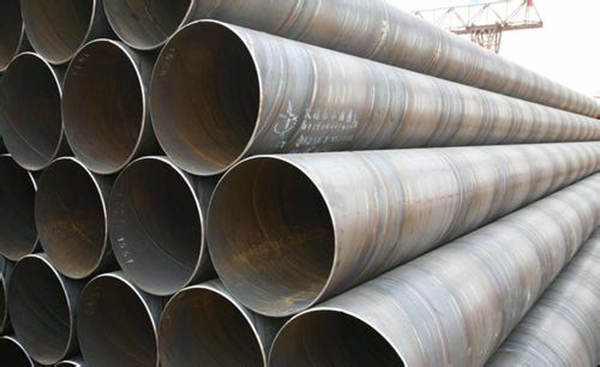
Conclusion
After a decade in the steel industry, I’ve learned that choosing between precision and standard steel tubes boils down to one thing: matching the right tool to the job. Precision tubes, with their tight tolerances and superior strength, are a game-changer for high-stakes projects like aerospace or medical devices. Standard tubes, meanwhile, deliver reliable performance for construction without breaking the bank.
At HnL Steel, we focus on quality and partnership, ensuring you get tubes that meet your needs with fast delivery and flexible terms. The right choice saves time, cuts costs, and boosts project success.
Think about your project’s demands—precision or affordability? That’s the first step to making a decision that pays off in the long run.
FAQ
Q1: What are precision steel tubes?
A1: Precision steel tubes are engineered to meet strict requirements for dimensions, wall thickness, and length. They are created using advanced production techniques like cold drawing to achieve high strength and rigidity.
Q2: How do precision steel tubes differ from standard steel tubes?
A2: Precision steel tubes are manufactured with tighter tolerances and better quality control compared to standard steel tubes, making them ideal for applications requiring high dimensional accuracy.
Q3: Why are precision steel tubes more expensive?
A3: The cost of precision tubes is higher due to the use of high-quality materials and sophisticated manufacturing processes that enhance their performance and durability.
Q4: What industries commonly use precision steel tubes?
A4: Precision steel tubes are often used in hydraulic equipment, automotive components, and other mechanical systems where precision and reliability are critical.
Q5: Can precision steel tubes be used interchangeably with standard tubes?
A5: Although precision steel tubes can sometimes replace standard tubes in certain applications, they are typically used where higher strength and dimensional accuracy are required.
Q6: What are the applications of standard steel tubes?
A6: Standard steel tubes are widely used in construction, water systems, and general manufacturing due to their cost-effectiveness, though they offer less precision than their precision counterparts.
Q7: What is the typical manufacturing process for precision steel tubes?
A7: Precision steel tubes are usually produced through processes like cold drawing or cold rolling, which help achieve the exact specifications needed for specialized applications.
Q8: How do the mechanical properties of precision steel tubes compare to standard tubes?
A8: Precision steel tubes generally exhibit superior mechanical properties, including higher strength and better resistance to stress, compared to standard steel tubes.
External Links
- Precision Steel Tubes vs. Traditional Steel Tubes: What’s the Difference?
- Why Are Precision Tubes More Expensive Than Regular Steel Tubes?
- The difference between precision steel tubes and ordinary steel tubes
- What is Precision Steel Tubes? – Botop Steel Pipes
- DIN 2391 Seamless Steel Tube: Meet Your Project Standard
- DIN 2391 Standard Seamless Precision Steel Tubes – EASTAI
- Precision Tubes vs. Standard Tubes: What You Need to Know
- Types of Steel Tubes with Applications as per ASTM Standards
2 Responses