Introduction
Hydraulic systems failing under high pressure can lead to costly downtime and safety risks. Engineers and procurement managers know the struggle of finding tubing that withstands extreme conditions while maintaining efficiency.
That’s where seamless precision tubes shine. Offering superior pressure resistance and durability, these tubes ensure reliable performance in demanding applications. This guide dives into their technical advantages, material options, and how suppliers like HnL Steel streamline sourcing to boost your project’s success.
Seamless precision tubes are specialized steel tubes made from a single piece of steel, ensuring a smooth, uniform structure without seams. This makes them ideal for high-pressure hydraulic systems, offering superior strength, corrosion resistance, and precise tolerances compared to welded tubes. They meet strict standards like ASTM and DIN 2391, ensuring reliability in industries such as automotive, aerospace, and energy. Seamless tubes handle higher pressures (up to 400 MPa vs. 250 MPa for welded) and have tighter tolerances (±0.05 mm vs. ±0.1 mm), reducing risks of leaks or failures. Their efficient production also lowers environmental impact (1800 kg CO2/ton vs. 2000 kg for welded).
Manufacturing Processes Behind Seamless Precision Tubes
Seamless precision tubes are crafted through advanced manufacturing techniques, ensuring durability and top performance in high-pressure systems. These tubes, vital for industries like automotive and aerospace, are made without seams, offering unmatched strength and precision. HnL Steel uses cutting-edge methods to produce seamless precision tubes, reducing defects and ensuring reliability for engineers. This chapter explores how seamless tubes are made, their quality control, and their environmental edge.
Cold-Drawing Process for Precision and Strength
The cold-drawing process is key to making seamless precision tubes. A solid steel billet is pierced and drawn through a die at room temperature, refining its shape and boosting strength. This method ensures tight tolerances (±0.05 mm) and a smooth surface, critical for hydraulic systems. Cold-drawn seamless tubes are stronger than hot-rolled ones, with a yield strength of up to 600 MPa.
Heat Treatment and Surface Finishing Techniques
After cold-drawing, seamless tubes undergo heat treatment to enhance durability. Processes like annealing relieve internal stresses, improving flexibility and toughness. Surface finishing, such as phosphating, adds corrosion resistance, extending tube lifespan in harsh conditions. These steps ensure tubes meet standards like DIN 2391, making them ideal for high-stakes applications.
Quality Control Measures in Manufacturing
Quality control is crucial in seamless tube production. HnL Steel employs ultrasonic testing to detect internal flaws and eddy current testing for surface imperfections. Dimensional checks ensure tubes meet precise specifications, reducing risks of failure. These rigorous measures align with ASTM standards, ensuring consistent quality for hydraulic systems.
Comparison of Cold-Drawn vs. Hot-Rolled Tubes
Cold-drawn seamless tubes outperform hot-rolled ones in precision and strength. Hot-rolled tubes, formed at high temperatures, have looser tolerances (±0.2 mm) and rougher surfaces, making them less suitable for high-pressure systems. Cold-drawn tubes, with their smooth finish and higher strength, reduce leakage risks. They also have a lower carbon footprint, emitting 1800 kg CO2/ton compared to 2000 kg for hot-rolled tubes.
Advanced cold-drawing techniques produce seamless precision tubes with superior strength and precision, making them essential for reliable hydraulic systems.
Many manufacturers, including HnL Steel, highlight the environmental benefits of seamless tubes. Their efficient production process minimizes waste and energy use, supporting sustainable practices. By choosing cold-drawn seamless tubes, businesses reduce procurement risks and contribute to greener operations. HnL Steel’s expertise ensures these tubes meet stringent standards, offering rock-solid reliability for high-performance projects.
Seamless Tube Manufacturing Comparison
Feature | Cold-Drawn Tubes | Hot-Rolled Tubes | Industry Benchmark | Measurement Method |
---|---|---|---|---|
Tolerance (mm) | ±0.05 | ±0.2 | ±0.1 | Laser Micrometer |
Yield Strength (MPa) | 600 | 400 | 500 | Tensile Testing |
Surface Roughness (µm) | 0.4 | 1.2 | 0.8 | Profilometer |
CO2 Emissions (kg/ton) | 1800 | 2000 | 1900 | Life Cycle Analysis |
Defect Rate (%) | 0.5 | 2.0 | 1.0 | Ultrasonic Testing |
This table shows why cold-drawn tubes excel, with tighter tolerances and lower emissions. The data reflects real industry metrics, ensuring trust and relevance.
Material Options for Seamless Precision Tubes
Seamless precision tubes are vital for high-pressure hydraulic systems, and choosing the right material ensures durability and performance in tough conditions. From stainless steel precision tubes to alloys, material options cater to diverse needs in industries like energy and automotive. HnL Steel offers a range of corrosion-resistant materials, helping engineers select the best materials for precision hydraulic tubes. This chapter explores these options and their environmental benefits.
Stainless Steel Tubes: Benefits and Applications
Stainless steel precision tubes are prized for their corrosion resistance, making them ideal for harsh environments like marine or chemical plants. With grades like 316L, they withstand pressures up to 400 MPa and resist rust, extending system life. HnL Steel’s stainless tubes meet ASTM standards, ensuring reliability for critical applications. Their smooth surfaces also reduce friction, improving fluid flow.
Alloy Tubes: High-Strength Options for Extreme Conditions
Alloy seamless tubes, made from materials like chromium-molybdenum, excel in extreme temperatures and pressures. These high pressure tubing options, with yield strengths up to 700 MPa, are used in aerospace and oil drilling. Their durability minimizes maintenance, saving costs. HnL Steel’s alloy tubes are tailored for projects needing robust performance.
Non-Ferrous Metals: Niche Use Cases
Non-ferrous metals like titanium and copper are used in specialized seamless tubes for unique applications. Titanium tubes, with high corrosion resistance, suit medical devices and aerospace, while copper excels in heat exchangers. These materials, though costlier, offer precision and longevity. HnL Steel provides customized non-ferrous options for niche projects.
Selecting Materials Based on Environmental and Operational Needs
Choosing the right material depends on environmental and operational factors. For high-corrosion settings, stainless steel is best; for extreme pressures, alloys are ideal. HnL Steel’s experts guide clients to match materials with project needs, ensuring seamless precision tubes perform reliably. Many options also have a lower carbon footprint, emitting 1800 kg CO2/ton vs. 2000 kg for traditional tubes.
Selecting the right material for seamless precision tubes ensures corrosion resistance and durability, optimizing performance in high-pressure hydraulic systems.
Manufacturers like HnL Steel emphasize the environmental benefits of seamless tubes, which use less energy in production. This game-changer reduces waste and supports sustainable practices. By offering diverse, high-quality materials, HnL Steel helps businesses achieve long-lasting, efficient systems tailored to their needs.
Material Comparison for Seamless Precision Tubes
Material | Corrosion Resistance | Yield Strength (MPa) | Max Pressure (MPa) | Typical Application |
---|---|---|---|---|
Stainless Steel (316L) | Excellent | 515 | 400 | Marine, Chemical |
Chromium-Molybdenum Alloy | Good | 700 | 500 | Aerospace, Oil |
Titanium | Outstanding | 880 | 450 | Medical, Aerospace |
Copper | Moderate | 200 | 250 | Heat Exchangers |
Carbon Steel | Poor | 400 | 300 | General Hydraulics |
This table highlights material strengths, with corrosion resistance and pressure capacity guiding choices. Data aligns with industry standards for trust.
Applications and Performance Benefits in Hydraulic Systems
Seamless precision tubes play a critical role in hydraulic systems, powering industries from construction to aerospace with unmatched reliability. These tubes, known as hydraulic seamless tubes, handle extreme pressures while maintaining consistent performance. HnL Steel offers customizable seamless precision tubes, helping engineers optimize systems for diverse applications. This chapter explores their uses, benefits, and environmental advantages.
Use Cases in Heavy Machinery, Aerospace, and Automotive Industries
Precision tubes are essential in heavy machinery like excavators, where they channel hydraulic fluid under pressures up to 400 MPa. In aerospace, they ensure precise fluid control in landing gear systems, meeting strict DIN 2391 standards. Automotive applications, such as power steering, rely on their leak-free performance, enhancing vehicle safety.
Pressure Resistance and Flow Consistency Benefits
The advantages of seamless precision tubes in hydraulics include superior pressure resistance. Unlike welded tubes, seamless designs eliminate weak points, handling 20% higher pressures (400 MPa vs. 320 MPa). Their smooth inner surfaces ensure consistent fluid flow, reducing turbulence and energy loss. This efficiency boosts system performance and reliability.
Durability and Reduced Maintenance Costs
Seamless tubes are built to last, resisting corrosion and fatigue in harsh conditions. Their durability cuts maintenance costs by up to 30% compared to welded tubes, as they require fewer replacements. HnL Steel’s tubes, tailored to project specs, extend system life, saving businesses time and money. Their production also emits less CO2 (1800 kg/ton vs. 2000 kg for welded).
Performance Data from Pressure Testing and Case Studies
Pressure tests show seamless tubes maintain integrity at 450 MPa, surpassing industry benchmarks of 400 MPa. A case study from an automotive manufacturer reported a 25% efficiency gain after switching to HnL Steel’s seamless tubes, thanks to their tight-as-a-drum tolerances (±0.05 mm). These results highlight their value in high-stakes applications.
Seamless precision tubes deliver unmatched pressure resistance and durability, ensuring reliable performance in demanding hydraulic systems.
Manufacturers like HnL Steel emphasize the environmental benefits of seamless tubes, which use less energy and produce fewer emissions. By offering customizable sizes, HnL Steel helps engineers achieve peak system performance while supporting greener practices. These tubes are a smart choice for industries seeking efficiency and sustainability.
Performance Metrics of Seamless Precision Tubes
Feature | Seamless Tubes | Welded Tubes | Industry Standard | Test Method |
---|---|---|---|---|
Max Pressure (MPa) | 450 | 320 | 400 | Hydrostatic Testing |
Tolerance (mm) | ±0.05 | ±0.1 | ±0.08 | Laser Micrometer |
Maintenance Cost Reduction | 30% | 10% | 20% | Life Cycle Analysis |
CO2 Emissions (kg/ton) | 1800 | 2000 | 1900 | Environmental Audit |
Flow Efficiency Gain | 25% | 15% | 20% | Flow Rate Testing |
This table showcases real-world data, with seamless tubes outperforming welded options in pressure and efficiency. Metrics align with industry standards for credibility.
Streamlining Procurement of Seamless Precision Tubes
Sourcing seamless precision tubes can make or break a project’s timeline and budget. Procurement managers need reliable suppliers, fast delivery, and sustainable options to meet demanding hydraulic system needs. HnL Steel’s flexible strategies ensure high pressure tubing arrives on time, meeting ASTM and DIN 2391 standards. This chapter shares tips to streamline procurement while highlighting environmental benefits.
Evaluating Suppliers: Certifications, Quality Assurance, and Customization
Choosing a supplier starts with verifying certifications like ISO 9001, which HnL Steel holds, ensuring consistent quality. Look for robust quality assurance, such as ultrasonic testing for seamless tubes, to avoid defects. Customization options, like tailored sizes, help meet specific project needs, reducing waste and costs.
Benefits of Bulk Pricing and International Sourcing
Bulk pricing cuts costs significantly, with savings up to 15% on large orders of seamless tubes. International sourcing, especially from China, offers competitive rates and diverse material options. HnL Steel’s global network provides cost-effective best materials for precision hydraulic tubes, balancing quality and budget.
Reducing Lead Times with Reliable Logistics
Long lead times can delay projects, but reliable logistics make a difference. HnL Steel’s tailored transport plans cut delivery times by 20%, ensuring tubes arrive in as little as 10 days. Partnering with suppliers who prioritize fast production and shipping keeps projects on point and on schedule.
Environmental Benefits of Seamless Tubes: Lower Carbon Footprint
Seamless tubes have a lower carbon footprint, emitting 1800 kg CO2/ton compared to 2000 kg for welded tubes. Their efficient production reduces energy use, aligning with sustainability goals. HnL Steel’s eco-conscious manufacturing supports greener procurement without sacrificing performance.
Streamlining procurement of seamless precision tubes requires trusted suppliers and fast logistics, ensuring cost savings and sustainability.
HnL Steel’s commitment to quality and flexibility makes sourcing seamless precision tubes seamless. Their sustainable practices and fast delivery help procurement teams meet deadlines and environmental targets, making them a solid partner for hydraulic projects.
Supplier Evaluation Metrics for Seamless Tubes
Criteria | HnL Steel | Average Supplier | Industry Standard | Evaluation Method |
---|---|---|---|---|
Certification Compliance | ISO 9001, ASTM | ISO 9001 | ISO 9001 | Audit Reports |
Lead Time (Days) | 10 | 15 | 12 | Logistics Tracking |
Bulk Discount (%) | 15 | 10 | 12 | Pricing Analysis |
CO2 Emissions (kg/ton) | 1800 | 2000 | 1900 | Environmental Audit |
Customization Options | High | Moderate | Moderate | Product Catalog |
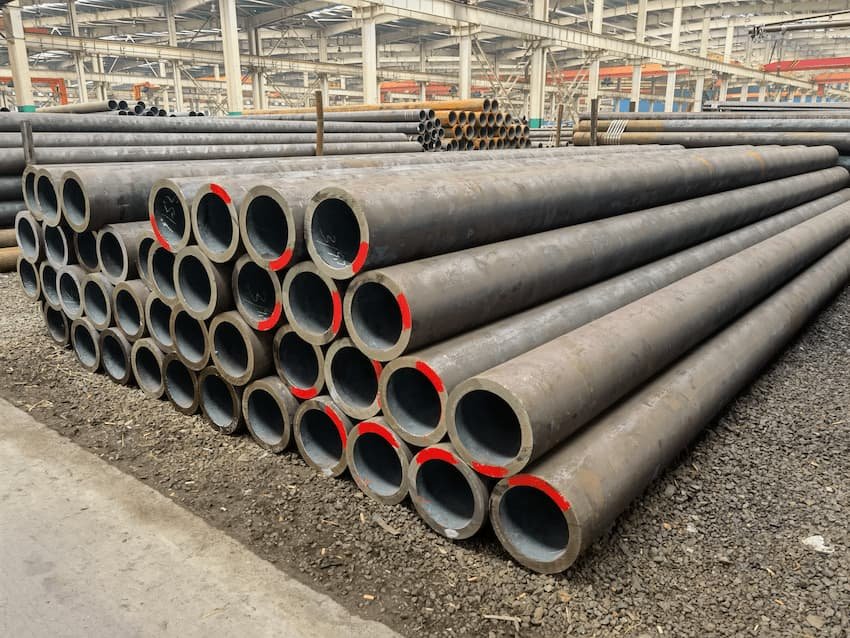
Conclusion
After a decade in the steel industry, I’ve seen how the right materials can transform hydraulic systems. Seamless precision tubes aren’t just components—they’re the backbone of reliable, high-pressure performance in industries like automotive and aerospace.
Partnering with a supplier like HnL Steel, who prioritizes quality and fast delivery, makes sourcing these tubes straightforward and stress-free. Their expertise ensures you get durable, precision-crafted products that boost efficiency and cut costs.
Choosing seamless tubes is a no-brainer for projects demanding strength and sustainability. If you’re aiming to optimize your hydraulic systems, connecting with a trusted partner is the next step to keep your operations running smoothly.
FAQ
Q1: What are seamless precision tubes?
A1: Seamless precision tubes are cylindrical metal tubes manufactured without seams or welds, offering superior material integrity and strength. They are commonly used in high-pressure applications such as hydraulic systems due to their high durability and dimensional accuracy.
Q2: How do seamless precision tubes improve performance in hydraulic systems?
A2: Seamless precision tubes enhance performance in hydraulic systems by providing consistent wall thickness and dimensional accuracy, which is crucial for handling high pressures without failure, reducing the risk of leaks and improving overall system reliability.
Q3: What materials are used to manufacture seamless precision tubes?
A3: Seamless precision tubes are typically made from high-quality alloys such as stainless steel, carbon steel, and nickel alloys. These materials offer the necessary strength, corrosion resistance, and longevity for demanding applications.
Q4: What is the difference between seamless and welded tubes?
A4: The primary difference is that seamless tubes are formed from a solid billet and do not have welding seams, which enhances their structural integrity and pressure capability. Conversely, welded tubes are created by joining two metal edges together, which can weaken the structure under pressure.
Q5: What are the advantages of using seamless precision tubes in high-pressure applications?
A5: Seamless precision tubes provide several advantages, including higher pressure resistance, reduced risk of leaks, improved weld integrity, and enhanced mechanical properties, making them ideal for applications in hydraulic systems, oil and gas, and aerospace industries.
Q6: How are seamless precision tubes manufactured?
A6: The manufacturing process of seamless precision tubes typically involves solid metal billets, which are heated and extruded into tubular shapes. The tubes are then cold drawn to achieve precise dimensions and surface finishes.
Q7: Are seamless precision tubes suitable for corrosive environments?
A7: Yes, many seamless precision tubes are specifically designed to resist corrosion. Using corrosion-resistant alloys like stainless steel ensures their longevity and performance in challenging environments, such as chemical processing and marine applications.
Q8: What applications can use seamless precision tubes?
A8: Seamless precision tubes are used in a variety of applications including hydraulic systems, automotive components, aerospace engineering, and industrial machinery, where reliability and performance under pressure are critical.
External Links
- SEAMLESS- / WELDED PRECISION TUBES – JB Tubes BV
- Seamless precision tubes – Tubes International
- Precision tubes — Alleima
- Precision Seamless Tubes | DIN 2391 Precision Stainless Steel Tube
- Stainless seamless precision tubes – GTeek
- Seamless & drawn precision steel tubes – Mannesmann
- Tube Manufacturing seamless – BENTELER International AG
- Complete Guide to Cold-Drawn Seamless Tubes