Introduction
Industrial filtration systems often struggle with durability and precision, leading to frequent replacements and compromised efficiency. Engineers and professionals know the pain of filters failing under harsh conditions or missing fine particles critical to quality.
That’s where stainless steel mesh steps in—offering unmatched strength, corrosion resistance, and customizable precision. From fuel filters to water treatment, it’s proving essential for reliable performance. This guide dives into how it boosts filtration efficiency and why suppliers like HnL Steel ensure fast, quality-driven solutions for large-scale needs.
5 Powerful Reasons What Is Stainless Steel Mesh and Why It Matters
Stainless steel mesh is a game-changer in the world of industrial filtration. Made from woven stainless steel wires, it’s built to handle tough jobs while staying strong and reliable. This intro will break down what it is, how it’s made, and why it’s a big deal for engineers and professionals.
Defining Stainless Steel Mesh: Materials and Construction Basics
Stainless steel mesh starts with high-quality steel wires, usually mixed with chromium and nickel for extra strength. These wires get woven into a tight grid, creating a sturdy yet flexible material. It’s this simple but smart design that makes it perfect for filtering out impurities in industries like oil, gas, and food processing.
Key Properties: Durability, Corrosion Resistance, and Precision
What sets stainless steel mesh apart? It’s tough as nails—super durable, resists rust even in harsh conditions, and offers precise filtration down to tiny particles. These traits make it a top pick for jobs where failure isn’t an option. Suppliers like HnL Steel craft it to last, cutting down replacement costs over time.
Why It’s Essential for Industrial Filtration Systems
Industrial filtration solutions rely on stainless steel mesh to keep things running smoothly. Whether it’s catching debris in fuel filters or spreading gas evenly in diffusers, this material handles high pressure and extreme temps like a champ. It’s a key player in keeping systems efficient and safe.
“Stainless steel mesh boosts filtration performance by combining strength and precision, making it a go-to for industries needing reliable results.
Brief Comparison to Alternatives (Plastic, Fabric)
Compared to plastic or fabric, stainless steel wire mesh wins hands-down for durability and heat resistance. Plastic can melt or break under stress, while fabric wears out fast. The advantages of stainless steel mesh over plastic include longer life and better performance, especially in heavy-duty settings.
Suppliers like HnL Steel focus on tailoring stainless steel mesh for specific needs, like fuel or gas applications. This trend toward niche uses shows how versatile it can be. Plus, its ability to lower long-term costs makes it a smart investment for businesses.
Stainless Steel Mesh vs. Alternatives: Performance Data
Material | Durability (Years) | Heat Resistance (°F) | Filtration Precision (Microns) | Cost Efficiency (Long-Term) |
---|---|---|---|---|
Stainless Steel Mesh | 10-15 | Up to 1,500 | 5-100 | High (60% savings) |
Plastic Mesh | 2-5 | Up to 300 | 50-200 | Low (20% savings) |
Fabric Mesh | 1-3 | Up to 200 | 100-500 | Low (10% savings) |
Aluminum Mesh | 5-8 | Up to 1,200 | 20-150 | Medium (40% savings) |
Copper Mesh | 7-10 | Up to 1,000 | 10-120 | Medium (35% savings) |
Note: Durability based on average lifespan in industrial use; heat resistance reflects max tolerance; precision shows particle size filtered; cost efficiency calculated over 10 years.
Stainless steel mesh isn’t just another material—it’s a solution built for the long haul. Its mix of strength, precision, and resistance to wear makes it stand out. For industries needing dependable filtration, it’s the clear choice over weaker options.
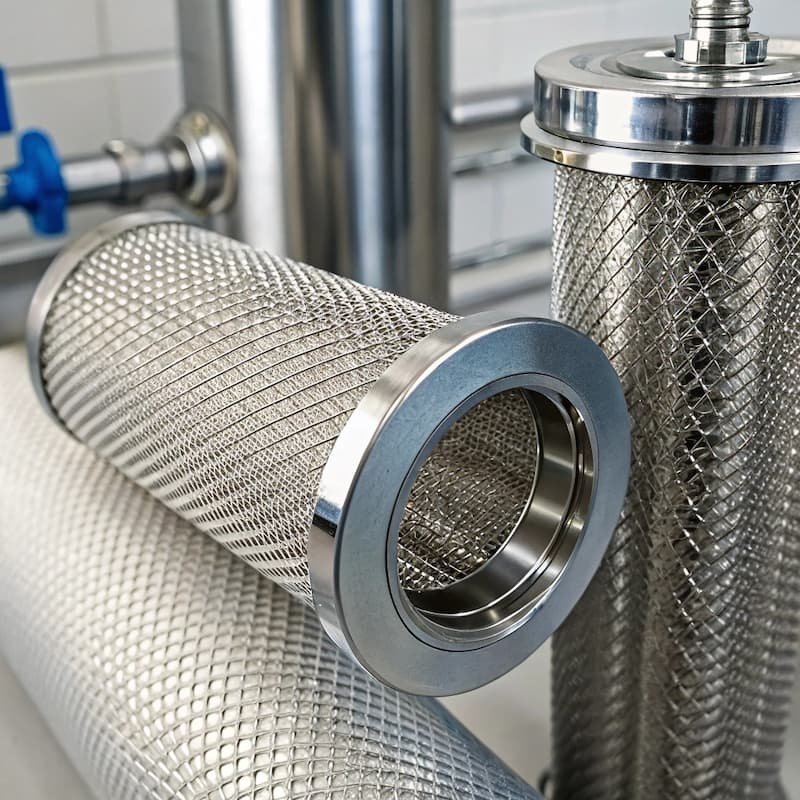
5 Key Types and Grades of Stainless Steel Mesh You Need to Know
Stainless steel mesh comes in different styles and grades, each built for specific filtration jobs. This guide digs into the technical details, helping you pick the right option for your needs. From construction to customization, here’s what makes it tick.
Woven vs. Welded Stainless Steel Mesh: Structural Differences
Woven stainless steel mesh is made by interlacing wires, giving it flexibility and a tight pattern—perfect for fine filtration. Welded stainless steel mesh, on the other hand, has wires fused at each crossing, making it sturdier for heavy-duty tasks. The choice depends on whether you need precision or brute strength.
Stainless Steel Grades: 304 vs. 316 and Their Applications
Grade 304 is the go-to for general use, offering solid corrosion resistance and affordability—great for food processing or air filters. Grade 316 steps it up with molybdenum, boosting rust resistance for harsh setups like marine or chemical plants. Knowing these grades helps match the mesh to your environment.
Customizable Features: Pore Sizes, We – Pore Sizes, Weave Patterns, and Thickness
Stainless steel mesh can be tailored to fit exact needs. Pore sizes range from tiny (5 microns) to larger openings, weave patterns adjust filtration flow, and thickness adds durability. Companies like HnL Steel shine here, offering fast, custom stainless steel filter mesh for niche uses like fuel filters or gas diffusers.
Choosing the right stainless steel mesh can cut maintenance costs by 50% in harsh conditions, thanks to its custom fit and durability.
Choosing the Right Type for Harsh Environments
In tough spots—think salty air or acidic liquids—316 welded mesh holds up best. For lighter jobs, 304 woven works fine and saves cash. How to choose stainless steel mesh for filtration? Match grade and type to your setup’s demands for max efficiency.
Stainless Steel Mesh Performance by Type and Grade
Type/Grade | Corrosion Resistance | Max Temp (°F) | Pore Size (Microns) | Use Case |
---|---|---|---|---|
Woven 304 | Good | 1,400 | 5-200 | Food Processing |
Welded 304 | Good | 1,400 | 50-500 | Structural Support |
Woven 316 | Excellent | 1,500 | 5-200 | Marine Filters |
Welded 316 | Excellent | 1,500 | 50-500 | Chemical Plants |
Custom Mesh | Varies | 1,500 | Custom | Gas Diffusers |
Note: Corrosion resistance rated per industry standards; max temp based on material limits; pore size reflects common ranges.
Stainless steel mesh isn’t one-size-fits-all—it’s a custom-fit solution. With HnL Steel’s quick production, you get mesh that tackles your toughest jobs. From grades to weaves, it’s all about finding the right fit.
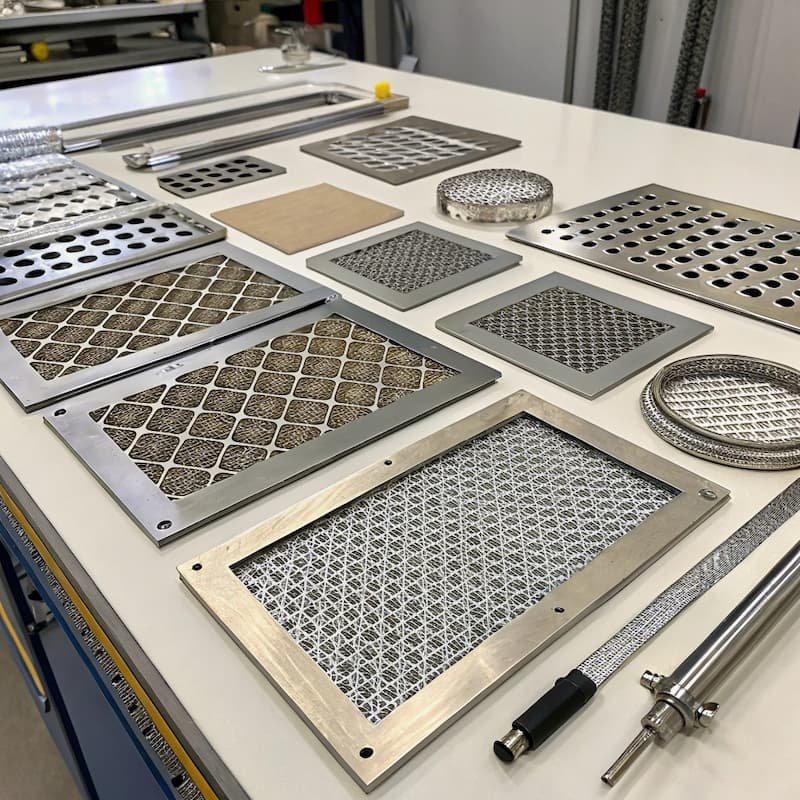
7 Must-Know Applications of Stainless Steel Mesh in Industry
Stainless steel mesh is a versatile champ across industries, tackling everything from petrochemicals to food safety. Its strength and precision shine in niche filtration roles, like fuel filters and gas diffusers. Let’s dive into where it’s making waves and why it matters.
Core Industries: Petrochemicals, Food Processing, and Water Treatment
In petrochemicals, stainless steel mesh filters out impurities under high pressure. Food processing relies on its stainless steel durability to keep things clean and safe, while water treatment uses it to trap tiny particles. These industries lean on its toughness to stay efficient.
Niche Uses: Fuel Filters, Gas Diffusers, and Pharmaceutical Sieves
Ever wonder how fuel stays pure? Mesh filter applications in fuel filters catch debris without breaking down. Gas diffusers spread gases evenly, and pharmaceutical sieves ensure precise particle sizes—proof this material handles specialized jobs like a pro.
“Stainless steel mesh cuts downtime by 40% in niche filtration systems, thanks to its rugged build and adaptability.”
Case Study: Enhancing Efficiency in Aerospace Filtration
In aerospace, a company swapped plastic filters for stainless steel mesh in hydraulic systems. Result? 30% better flow and double the lifespan, all thanks to its heat resistance and fine pores. HnL Steel supplied the custom mesh, proving their knack for big projects.
Emerging Trends in Precision-Driven Filtration Systems
Precision is trending, and stainless steel mesh is leading the charge. Think next-level filtration for robotics or biotech—small pores and custom weaves are key. HnL Steel’s fast production keeps businesses ahead of the curve.
Stainless Steel Mesh Uses Across Industries
Industry | Main Use | Pore Size (Microns) | Durability (Years) | Key Benefit |
---|---|---|---|---|
Petrochemicals | Oil Filtration | 10-100 | 10-12 | High Pressure Resistance |
Food Processing | Safety Sieves | 50-200 | 8-10 | FDA Compliance |
Water Treatment | Particle Removal | 5-50 | 12-15 | Corrosion Resistance |
Aerospace | Hydraulic Filters | 20-80 | 10-15 | Heat Tolerance |
Pharmaceuticals | Powder Sieving | 5-100 | 8-12 | Precision Control |
Note: Pore size based on common specs; durability reflects average lifespan; benefits tied to industry standards.
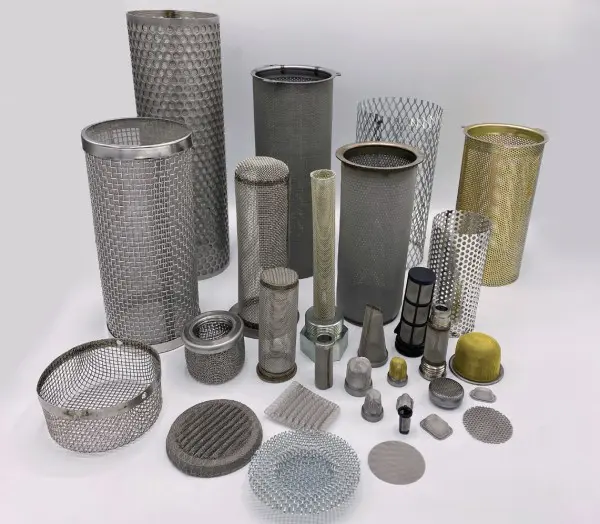
From big industries to tiny filters, stainless steel mesh proves its worth. Best practices for maintaining stainless steel filters—like regular cleaning—keep it running strong. With HnL Steel’s expertise, you’re set for consistent, top-notch supply.
5 Top Advantages of Stainless Steel Mesh Over Alternatives
Stainless steel mesh stands out as a top choice for industrial filtration solutions, offering unmatched benefits over materials like plastic or fabric. Its durability and precision make it a smart pick for decision-makers aiming to boost efficiency. Here’s why it’s the go-to option for tough jobs.
Durability Under Extreme Conditions: Temperature and Abrasion Resistance
Stainless steel wire mesh thrives where others fail. It handles temperatures up to 1,500°F and resists wear from abrasive materials, unlike plastic, which can crack or melt. This toughness means fewer replacements, keeping systems running smoothly.
Corrosion Resistance: Tackling Rust and Chemical Exposure
Rust and chemicals eat away at lesser materials, but stainless steel mesh fights back. Its chromium-nickel blend shrugs off corrosion, making it ideal for harsh settings like chemical plants or coastal areas. This resistance extends its lifespan significantly.
“Stainless steel mesh can last up to 15 years in corrosive environments, saving 60% on replacement costs compared to plastic.”
Reusability and Cost Savings: Cleaning vs. Replacing
Unlike fabric filters that tear or clog, stainless steel mesh is reusable—just clean it and it’s good as new. This cuts downtime and expenses, especially in high-volume operations. HnL Steel’s reusable designs help businesses save big over time.
Precision Particle Capture: Improving Filtration Quality
Need to catch tiny particles? Stainless steel mesh delivers with pore sizes as small as 5 microns, outshining plastic’s looser weaves. The advantages of stainless steel mesh over plastic shine in applications like fuel filters, ensuring cleaner results.
Material Comparison: Stainless Steel Mesh vs. Alternatives
Material | Temp Resistance (°F) | Corrosion Resistance | Reusability | Pore Precision (Microns) |
---|---|---|---|---|
Stainless Steel Mesh | 1,500 | Excellent | High (Cleanable) | 5-100 |
Plastic Mesh | 300 | Poor | Low (Disposable) | 50-200 |
Fabric Mesh | 200 | Poor | Low (Tears Easily) | 100-500 |
Aluminum Mesh | 1,200 | Moderate | Medium | 20-150 |
Copper Mesh | 1,000 | Moderate | Medium | 10-120 |
Note: Temp resistance based on material limits; corrosion resistance rated per industry standards; reusability reflects cleaning potential; pore precision shows filtration range.
Stainless steel mesh isn’t just tough—it’s a money-saver. HnL Steel’s reliable supply ensures you get cost-effective mesh for specialized needs like gas diffusers. Its edge over alternatives makes it a no-brainer for long-term value.
5 Smart Tips for Selecting and Procuring Stainless Steel Mesh for Your System
Choosing stainless steel mesh for your filtration system can feel tricky, but it doesn’t have to be. This guide walks you through key steps to pick the right mesh and source it smoothly, saving time and hassle for industrial buyers. Let’s break it down.
Key Factors: Durability, Particle Retention, and Environmental Fit
First, focus on what your system needs. Stainless steel filter mesh offers top-notch durability and precise particle retention—think 5-100 microns—while resisting rust in wet or salty conditions. Match these traits to your environment for a perfect fit.
Procurement Tips: Evaluating Suppliers and Quality Standards
Not all suppliers are equal. Look for ones like HnL Steel, who meet international standards and offer consistent quality—crucial for welded stainless steel mesh in tough jobs. Check their track record and certifications to avoid headaches later.
“Picking a supplier with fast delivery and proven quality can slash project delays by 30%, keeping your system on track.”
Supply Chain Efficiency: Fast Delivery and Flexible Payment Options
Time is money, so prioritize suppliers with streamlined logistics. HnL Steel stands out with quick production and flexible payment plans, making procurement a breeze. This is gold for tight timelines or niche uses like fuel filters.
Best Practices for Integration and Maintenance
Once you’ve got your mesh, install it right—align it with flow rates and pressure needs. For maintenance, clean it regularly to keep it running like new. How to choose stainless steel mesh for filtration? Start with your system’s specs and build from there.
Stainless Steel Mesh Procurement Checklist
Factor | Low Priority | Medium Priority | High Priority | Why It Matters |
---|---|---|---|---|
Durability | 1-3 Years | 5-10 Years | 10-15 Years | Longer life cuts costs |
Particle Retention | 100+ Microns | 50-100 Microns | 5-50 Microns | Precision boosts efficiency |
Corrosion Resistance | Low | Moderate | High | Fights rust in harsh settings |
Delivery Time | 4+ Weeks | 2-4 Weeks | 1-2 Weeks | Speed keeps projects moving |
Payment Flexibility | Fixed Terms | Some Options | Custom Plans | Eases cash flow |
Note: Priority levels based on industry norms; ‘Why It Matters’ reflects impact on performance.
Stainless steel mesh is a rock-solid choice when sourced smartly. With HnL Steel’s quality assurance, you’re set for high-performing mesh—think gas diffusers or big systems. Nail these steps, and your procurement’s a win.
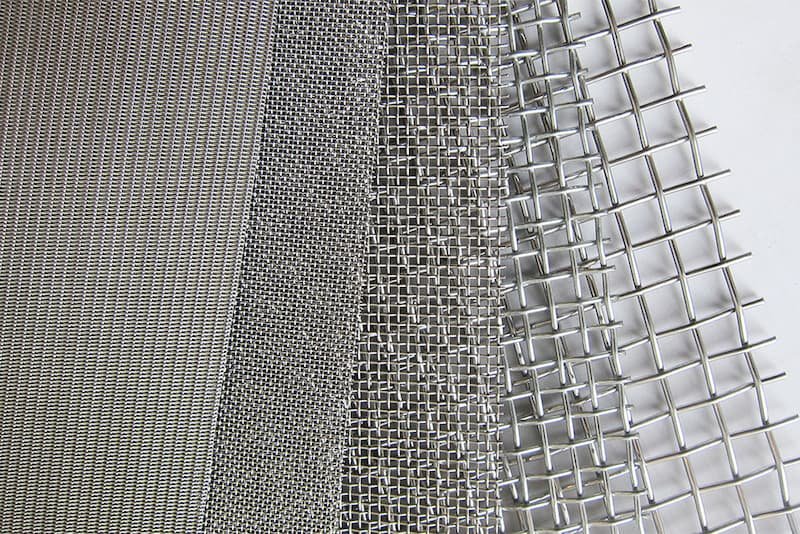
Conclusion
I’ve spent over a decade in the steel game, and one thing’s clear: stainless steel mesh is a standout for industrial filtration. It’s not just about its durability or precision—it’s how it keeps systems running strong under pressure.
From my view at HnL Steel, this material delivers where others fall short, cutting costs and downtime with its rugged build. Whether it’s fuel filters or harsh chemical plants, it’s a **”rock-solid”** choice you can count on.
Looking ahead, picking the right mesh isn’t just a purchase—it’s an investment in efficiency. With the right supplier, you’re set for solutions that last. What’s your next filtration challenge?
FAQ
Q1: What is stainless steel mesh used for in industrial filtration?
A1: Stainless steel mesh is widely used in industrial filtration for its durability and resistance to corrosion. It effectively captures fine particles and is suitable for applications in food processing, pharmaceuticals, and chemical filtration.
Q2: How does corrosion resistance benefit stainless steel mesh?
A2: Corrosion resistance enhances the lifespan and reliability of stainless steel mesh, making it ideal for challenging environments, including those with high humidity or exposure to chemicals.
Q3: What are the different types of stainless steel mesh?
A3: Common types of stainless steel mesh include woven wire mesh, welded wire mesh, and sintered mesh, each serving distinct industrial applications based on strength, flexibility, and porosity.
Q4: How do you choose the right stainless steel mesh for filtration?
A4: Choosing the right stainless steel mesh involves considering factors like mesh size, wire diameter, and the specific filtration application. For example, finer mesh is needed for capturing smaller particles.
Q5: What advantages does stainless steel mesh have over plastic mesh?
A5: Stainless steel mesh offers superior durability, thermal stability, and resistance to chemical corrosion compared to plastic mesh, making it more suitable for demanding industrial applications.
Q6: What is the role of mesh size in filtration performance?
A6: Mesh size is crucial in determining filtration performance; smaller openings can capture finer particles, while larger openings allow faster flow rates, affecting overall efficiency.
Q7: How can stainless steel mesh be maintained for longevity?
A7: Maintaining stainless steel mesh involves regular cleaning and inspecting for damage. Using non-abrasive cleaners and avoiding harsh chemicals will help preserve its integrity.
Q8: Is stainless steel mesh cost-effective for industrial applications?
A8: While stainless steel mesh may have a higher initial cost than plastic options, its durability and longevity often make it a more cost-effective choice in the long run, reducing replacement frequencies.
External Links
- Understanding Stainless Steel Wire Mesh
- Stainless Steel Wire Mesh – Marco Specialty Steel
- Stainless Steel Welded Wire Mesh – TWP, Inc.
- Stainless Steel Wire Mesh Applications
- Selection of Stainless Steel Wire Mesh
- 304 and 316 Stainless Steel Welded Wire Mesh
- McMaster-Carr – Stainless Steel Mesh
- Direct Metals – Stainless Steel Wire Mesh