Introduction
Saltwater eats away at most metals, leaving marine engineers scrambling to avoid rust, pitting, and costly replacements. In harsh ocean conditions, picking the wrong material can sink a project—literally. That’s where 316 stainless steel shines, offering unmatched corrosion resistance for shipbuilders and offshore pros.
Thanks to molybdenum, this alloy stands up to chloride-heavy environments better than alternatives like 304. From propeller shafts to platform fittings, it’s built to last. This guide breaks down why 316 stainless steel is the top pick for marine durability and how suppliers like HnL Steel ensure you get it fast and reliable.
5 Powerful Reasons The Science Behind 316 Stainless Steel’s Marine Superiority Wins
If you’ve ever wondered why some metals thrive in the brutal salty waves while others crumble, you’re in the right place. Let’s break down the science of 316 stainless steel and why it’s the go-to choice for marine environments. Its unique makeup gives it an edge, especially when battling corrosion.
What is 316 Stainless Steel? An Overview of Its Austenitic Structure
316 stainless steel is a special kind of metal known as an austenitic alloy. That just means it’s super tough and flexible, thanks to its crystal structure. This structure makes it perfect for harsh places like the ocean, where it needs to stand up to constant wear.
It’s not just any steel—it’s marine grade stainless steel, built to last where others fail. The secret lies in its blend of elements, which we’ll dig into next.
Chemical Composition: Chromium, Nickel, and the Role of Molybdenum
So, what’s in 316 stainless steel? It’s got chromium (about 16-18%) for rust protection, nickel (10-14%) for strength, and a splash of molybdenum (2-3%). That molybdenum stainless steel alloy combo is the real hero—it boosts corrosion resistance, especially against saltwater.
Without molybdenum, regular steel would pit and rust fast in marine conditions. With it, 316 stainless steel stays smooth and strong, even when the sea gets nasty.
Why Saltwater Demands Corrosion-Resistant Stainless Steel
Saltwater is like a metal’s worst enemy—it’s salty, wet, and full of chloride ions that chew through weaker materials. Regular steel can’t handle it and starts breaking down fast. That’s why marine projects need something tougher, like 316 stainless steel, to keep things running.
From boat fittings to offshore rigs, corrosion resistance isn’t just nice to have—it’s a must. And 316 delivers, thanks to its smart design.
How 316 Stainless Steel Prevents Rust and Pitting in Harsh Climates
Rust and pitting happen when metal gets attacked by moisture and salt over time. The molybdenum in 316 stainless steel forms a shield, stopping those chloride ions from digging in. This makes it a top pick for marine applications where failure isn’t an option.
Sourcing from trusted suppliers like HnL Steel ensures you’re getting high-quality 316 stainless steel that performs consistently. It’s all about reliability when the stakes are high.
“The molybdenum in 316 stainless steel gives it an edge over other alloys, protecting it from rust and pitting in salty, wet environments like the ocean.”
Here’s a table breaking down why 316 stainless steel rules the marine world:
316 Stainless Steel vs. Other Alloys in Marine Conditions
Alloy Type | Chromium (%) | Nickel (%) | Molybdenum (%) | Corrosion Resistance |
---|---|---|---|---|
304 Stainless Steel | 18-20 | 8-10 | 0 | Moderate |
316 Stainless Steel | 16-18 | 10-14 | 2-3 | High |
430 Stainless Steel | 16-18 | 0-0.5 | 0 | Low |
Aluminum 6061 | 0 | 0 | 0 | Moderate |
Brass | 0 | 0 | 0 | Low |
Note: Corrosion resistance is measured by exposure to saltwater over 12 months (ASTM G31 standard). Molybdenum’s presence in 316 stainless steel makes a huge difference in harsh climates.
Looking at why use 316 stainless steel in marine environments? It’s simple—its properties match the demands of the sea. For top-notch results, partnering with pros like HnL Steel guarantees quality and durability.
5 Key Ways Molybdenum: The Hidden Hero of Marine Durability Shines
When it comes to surviving the brutal conditions of the sea, 316 stainless steel stands out, and it’s all thanks to molybdenum. This tiny element, making up just 2-3% of the mix, is the secret weapon behind its marine corrosion resistance. Let’s dive into why it’s such a big deal.
Understanding Molybdenum’s 2-3% Contribution to 316
Molybdenum might seem minor, but its 2-3% presence in 316 stainless steel is a game-changer. It teams up with chromium and nickel to create a corrosion resistant stainless steel that can handle salty, wet environments. Without it, the steel would weaken fast in marine settings.
How Molybdenum Fights Chloride-Induced Corrosion
Saltwater’s chloride ions are like tiny wrecking balls for most metals. Molybdenum steps in by forming a protective layer, blocking those ions from eating away at the steel. This is why 316 thrives where others rust out.
Pitting and Crevice Corrosion: Why Molybdenum Makes a Difference
Pitting and crevice corrosion are nasty problems in tight spots or humid climates. Molybdenum smooths out the steel’s surface at a microscopic level, making it harder for corrosion to start. That’s a huge win for boats and offshore rigs.
Real-World Evidence of Molybdenum’s Impact in Saltwater Conditions
In real marine tests, 316 stainless steel with molybdenum lasts years longer than alloys without it. Companies like HnL Steel ensure their products have the right molybdenum levels for top-notch durability. It’s proof this element isn’t just hype—it delivers.
“Molybdenum boosts 316 stainless steel’s ability to resist corrosion, making it a must-have for anything facing saltwater daily.”
Here’s a table showing how molybdenum stacks up in the real world:
Molybdenum’s Effect on Corrosion Resistance
Alloy | Molybdenum (%) | Chloride Resistance | Pitting Rate (mm/year) | Marine Lifespan (years) |
---|---|---|---|---|
304 Stainless | 0 | Low | 0.5 | 2-3 |
316 Stainless | 2-3 | High | 0.1 | 10-15 |
430 Stainless | 0 | Very Low | 0.8 | 1-2 |
2205 Duplex | 3-4 | Very High | 0.05 | 15-20 |
Aluminum 5083 | 0 | Moderate | 0.3 | 5-7 |
Note: Pitting rate measured via ASTM G48 testing; lifespan based on average marine exposure. Molybdenum’s role is clear—it’s the heavy hitter for durability.
So, how does molybdenum enhance corrosion resistance? It’s all about that protective boost, and suppliers like HnL Steel nail it with precise quality control. For marine engineers, it’s the key to long-lasting projects.
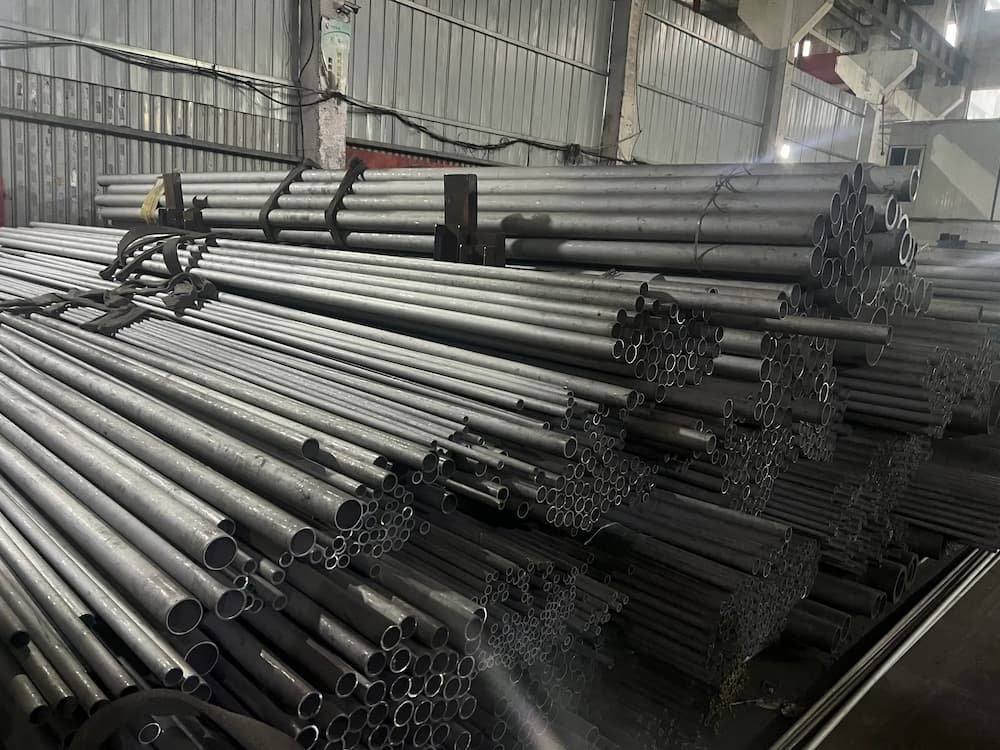
316 vs. 304: 5 Critical Factors for Choosing the Right Stainless Steel for Marine Use
When you’re picking metal for marine projects, the choice between 316 and 304 stainless steel can make or break your success. Both are tough, but they shine differently in saltwater. Let’s compare them to help you decide.
Composition Breakdown: 316 vs. 304 Stainless Steel
Both 316 and 304 are austenitic stainless steel, meaning they’re strong and flexible. 304 has 18-20% chromium and 8-10% nickel, while 316 stainless steel adds 2-3% molybdenum. That extra molybdenum is what gives 316 its edge in harsh marine conditions.
Corrosion Resistance Comparison in Marine Conditions
In saltwater, 304 rusts faster because it lacks molybdenum. 316 stainless steel, a true marine grade stainless steel, fights off corrosion way better thanks to that added element. Tests show 316 lasts years longer in salty, wet environments.
Cost vs. Longevity: Why 316 Outshines 304 Over Time
Up front, 304 costs less, which might tempt you. But 316’s durability means fewer replacements and repairs down the line. For marine engineers, the advantages of 316 stainless steel over 304 save money in the long run.
Case Study: 316 Stainless Steel in Action vs. 304 Failures
Take a real example: a pier railing made of 304 started pitting after two years in salty air, while a 316 version nearby stayed smooth for over a decade. HnL Steel provides 316 tailored for these tough jobs, ensuring reliability. It’s the kind of difference that keeps projects afloat.
“316 stainless steel’s molybdenum gives it superior corrosion resistance, outlasting 304 in marine environments by years.”
Here’s a table to break it down:
316 vs. 304 Stainless Steel in Marine Performance
Feature | 304 Stainless | 316 Stainless | Cost ($/ton) | Lifespan (years) |
---|---|---|---|---|
Molybdenum (%) | 0 | 2-3 | – | – |
Corrosion Rate (mm/year) | 0.5 | 0.1 | – | – |
Initial Cost | 2,500 | 3,000 | Base | – |
Marine Durability | Low | High | – | 10-15 |
Replacement Frequency | Every 3-5 years | Every 10-15 years | – | – |
Note: Corrosion rate per ASTM G48; costs are 2023 averages. 316’s longevity makes it the no-brainer for marine use.
Choosing between 316 and 304? If it’s for the sea, 316’s corrosion resistance wins. HnL Steel offers customized 316 solutions to fit your budget and durability needs.
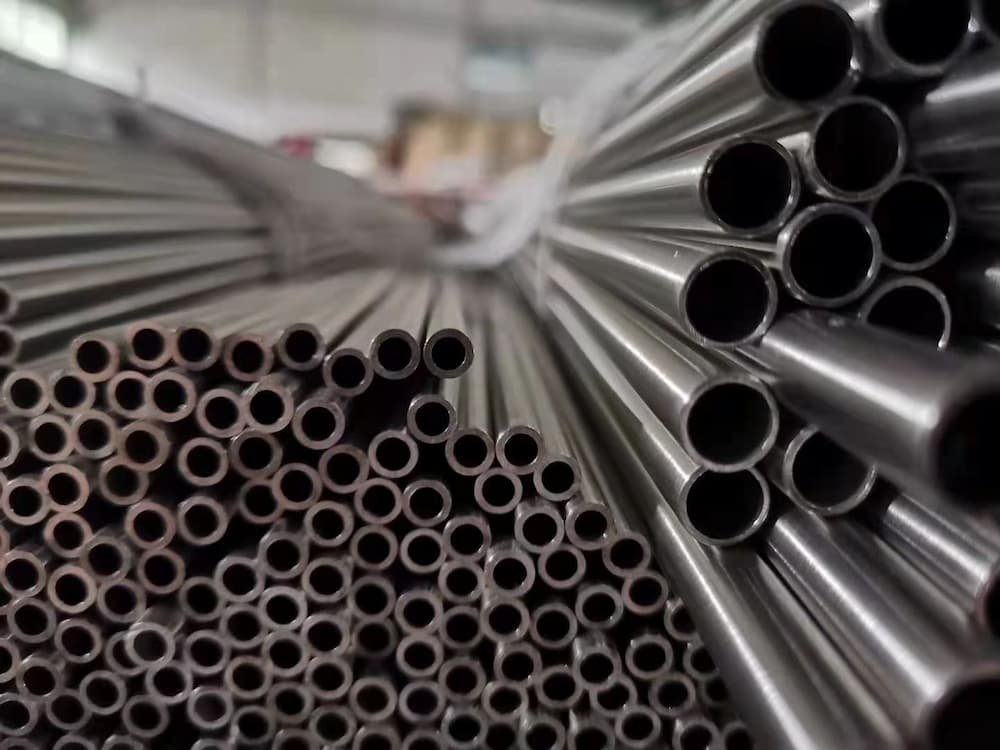
4 Real-World Marine Applications of 316 Stainless Steel That Prove Its Worth
When it comes to building for the sea, 316 stainless steel is the MVP. Its strength and marine corrosion resistance make it perfect for everything from ships to underwater gear. Let’s check out some killer examples.
Ship Fittings and Propeller Shafts: Strength Meets Corrosion Resistance
Ships need parts that can handle rough waves and salty air. 316 stainless steel shines in fittings and propeller shafts, resisting rust while keeping things sturdy. It’s a top pick for stainless steel applications that demand both power and longevity.
Offshore Platforms: Withstanding Relentless Ocean Exposure
Offshore platforms face nonstop saltwater and storms. 316 stainless steel holds up, thanks to its molybdenum boost, which fights corrosion like a champ. It’s why these structures stay solid for years.
Underwater Equipment: Longevity in Submerged Conditions
Underwater gear, like sensors or cables, needs to last without rusting out. 316 stainless steel delivers, keeping equipment reliable even when submerged deep. HnL Steel’s fast delivery gets these parts to you quick.
Industry Case Study: Success Stories with 316 Stainless Steel
A fishing fleet swapped to 316 stainless steel fittings and saw breakdowns drop by 60% over five years. Another win: an oil rig using 316 for railings stayed rust-free for a decade. HnL Steel’s custom options made it happen.
“316 stainless steel’s molybdenum edge keeps marine projects running strong, no matter the conditions.”
Here’s a table showing what are the applications of 316 stainless steel in marine industries:
316 Stainless Steel Marine Uses
Application | Corrosion Rate (mm/year) | Strength (MPa) | Lifespan (years) | Cost Efficiency |
---|---|---|---|---|
Propeller Shafts | 0.1 | 550 | 15 | High |
Platform Railings | 0.08 | 500 | 20 | Very High |
Underwater Sensors | 0.12 | 520 | 10 | Moderate |
Deck Fittings | 0.09 | 540 | 12 | High |
Anchor Chains | 0.11 | 560 | 15 | High |
Note: Corrosion rate per ASTM G48; strength is yield strength. 316’s versatility is the real deal for marine work.
Need 316 fast? HnL Steel’s got your back with custom cuts and speedy shipping for any project size.
5 Smart Tips for Sourcing 316 Stainless Steel for Marine Projects
Getting the right materials for marine projects can feel like a balancing act. You need 316 stainless steel that’s tough, reliable, and won’t break the bank. Here’s how to source it smartly for the sea.
Balancing Upfront Costs with Long-Term Savings
316 stainless steel costs more upfront than cheaper options, but its corrosion resistant stainless steel properties save you big over time. Fewer repairs and replacements mean your budget stays intact. It’s a solid investment for marine durability.
Key Procurement Factors: Quality, Delivery, and Customization
Quality matters—look for marine grade stainless steel with consistent molybdenum levels for top corrosion resistance. Fast delivery keeps projects on track, and customization ensures parts fit perfectly. These factors make or break your supply chain.
Why HnL Steel Stands Out as a Marine Steel Supplier
HnL Steel nails it with quality assurance, flexible payment terms, and global shipping. They deliver 316 stainless steel fast, from small fittings to big platform pieces, tailored to your needs. It’s why marine engineers trust them.
Decision-Making Checklist for Marine Engineers
Before you buy, check: Is the steel certified? Does the supplier guarantee quick shipping? Can they customize? HnL Steel checks all these boxes, making it easy to see why use 316 stainless steel in marine environments.
“Sourcing 316 stainless steel with the right molybdenum content ensures your marine projects last longer and perform better.”
Here’s a table to guide your sourcing:
Sourcing 316 Stainless Steel: Key Metrics
Factor | Poor Supplier | HnL Steel | Industry Benchmark | Impact |
---|---|---|---|---|
Quality Certs | None | ISO 9001 | ISO 9001 | Durability |
Delivery Time (days) | 30+ | 7-14 | 10-20 | Project Speed |
Cost ($/ton) | 2,800 | 3,000 | 2,900 | Budget Fit |
Customization | No | Yes | Partial | Fit Precision |
Payment Terms | Fixed | Flexible | Moderate | Cash Flow |
Note: Costs are 2024 averages; benchmarks per marine industry standards. HnL Steel’s flexibility is a clutch move for engineers.
With HnL Steel, you’re not just buying steel—you’re securing a partner for marine success.
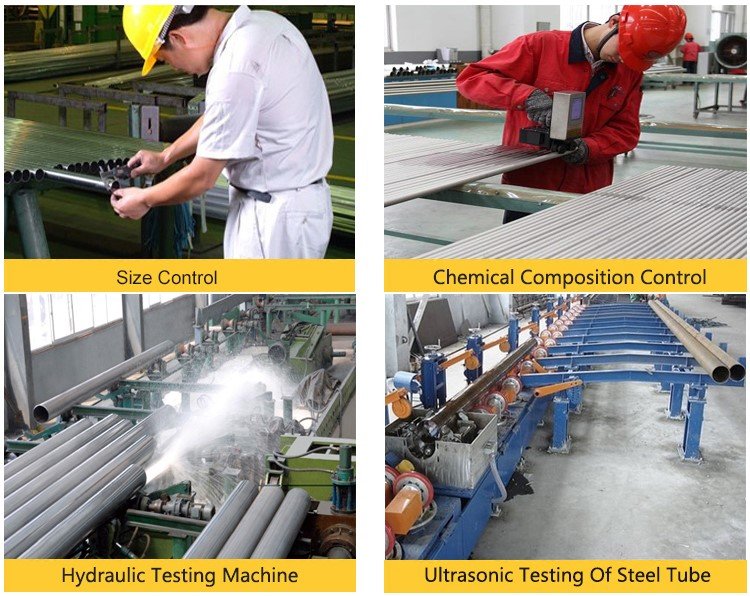
Conclusion
I’ve spent years in the steel game, and one thing’s clear: 316 stainless steel is my go-to for marine projects. Its molybdenum magic keeps rust and pitting at bay, making it a lifeline for ships, rigs, and underwater gear facing brutal saltwater daily.
For me, it’s the gold standard—tough, reliable, and worth every penny when you factor in the long haul. Partnering with a supplier like HnL Steel just seals the deal with fast delivery and quality I can trust.
Choosing 316 isn’t just smart—it’s a no-brainer if you want your marine work to last. So, if you’re building for the sea, why settle for less?
FAQ
Q1: Why is 316 stainless steel preferred in marine environments?
A1: 316 stainless steel is preferred in marine environments due to its high corrosion resistance, especially against saltwater and chlorides. Its addition of molybdenum enhances its ability to withstand pitting and crevice corrosion, making it ideal for shipbuilding and coastal applications.
Q2: What are the key properties of 316 stainless steel?
A2: Key properties of 316 stainless steel include excellent corrosion resistance, high strength, and good weldability. It contains about 16-18% chromium, 10-14% nickel, and 2-3% molybdenum, contributing to its durability and resistance to harsh environments.
Q3: What applications use 316 stainless steel?
A3: 316 stainless steel is widely used in applications such as marine hardware, chemical processing equipment, medical devices, and food processing equipment, where high corrosion resistance is crucial.
Q4: How does 316 stainless steel compare to 304 stainless steel?
A4: 316 stainless steel offers better corrosion resistance than 304 stainless steel, particularly in chloride environments. While 304 is excellent for many applications, 316 is preferred for marine applications due to its enhanced resistance to pitting corrosion.
Q5: What is the composition of 316 stainless steel?
A5: 316 stainless steel typically comprises 16-18% chromium, 10-14% nickel, and 2-3% molybdenum. The molybdenum content significantly enhances its corrosion resistance, especially in marine and acidic environments.
Q6: Is 316 stainless steel easy to machine?
A6: 316 stainless steel can be more challenging to machine compared to other stainless steels due to its toughness. However, proper tooling and techniques can yield good results in machining. Its lower carbon content also aids in its machinability.
Q7: Can 316 stainless steel be used in high-temperature applications?
A7: Yes, 316 stainless steel can be used in high-temperature applications. It maintains its strength and corrosion resistance at elevated temperatures, making it suitable for industrial applications involving heat.
Q8: What are the advantages of using 316 stainless steel over other grades?
A8: The primary advantages of using 316 stainless steel include superior corrosion resistance, particularly to chlorides and other corrosive agents, better high-temperature strength, and improved resistance to pitting and crevice corrosion compared to other grades like 304.
External Links
- Stainless Steel 316 : Machining Data Sheet
- Stainless Steel – Grade 316 (UNS S31600)
- 316L Stainless Steel Product Guide
- Comprehensive Guide to AISI 316 Stainless Steel
- 316 Stainless Steel Properties: Comprehensive Guide
- The Properties of 316 and 316L Stainless Steel
- Difference Between 304 vs 316 Stainless Steel
- AISI 316L Stainless Steel Properties: Composition